![]() STREAMWAY System mounts on a wall, connects to a facility’s vacuum supply, and pulls fluid from a patient’s body directly into the sewer system. |
During an operation, doctors drain between 30mL and 60L of fluid from the patient. The fluid is led through a tube connected to the patient and, most times into a canister. When that is full, a nurse, still garbing a mask, scrubs, and gloves, takes the canister, sometimes across hallways, and disposes of the fluid into a designated destination. The Environmental Protection Agency (EPA) suggests that discarding fluid waste through a sewer system is a safe option. The agency discourages incineration and prefers facilities to consider on-site treatment or disposal, rather than transport and dump regulated medical waste (RMW) into landfills. Oftentimes, however, that means nurses dump the fluid in drains and sinks, possibly exposing them to dangerous infectious diseases.
BioDrain Medical, a Minnesota-based medical device company has introduced a product that its officials say will make disposing of fluid waste in a surgical facility safer for hospital employees, as well as the environment.
Representatives from BioDrain Medical Inc. say the company’s STREAMWAY System is an automated, direct-to-drain fluid waste disposal system. The system mounts on a wall, connects to the facility’s vacuum supply, and pulls fluid from a patient’s body directly into the sewer system. This, says Dave Johnson, COO, BioDrain, eliminates the need to handle canisters and allows for unlimited capacity to ensure a procedure is not interrupted, which can be the case for powered canister systems.
“We are very safety-oriented for both the hospital and the worker,” Johnson says. “The staff and the patient, they are no longer going to have to be exposed to blood-borne pathogens when they open up the top of some contaminated fluid.”
Johnson explains that BioDrain engineers set out to build this type of system after seeing what they considered to be faults in other systems. They worked with a number of other companies, including SMC and Solidworks, to compile components, to design the machine, and to overcome challenges they faced during the manufacturing process.
Canning the Canister
Most healthcare facilities use canisters to collect body waste fluid during an operation. They are typically between 1L and 3L in size, meaning many of them could be filled during a procedure. If a surgical jar fills up during an operation, the operation is stopped until it can be replaced. After the fluid waste is dumped down a sink or drain, the canister is rinsed and thrown away as medical waste.
Instead of using disposable canisters, the STREAMWAY System uses a vessel assembly, which Johnson describes as something of a “complex canister” that has an unlimited capacity and never has to be thrown away. The vessel assembly collects fluid from the surgical field, and sensors on the side of the system keep the vacuum suctioning at a safe pace.
“It is a pretty complex canister, you might say, where we have to have our input, and our output, and our valving, and our sensor attached to it,” Johnson says.
Precision Vacuuming
The amount of vacuuming and pressure involved with an automated surgical waste fluid system is paramount. Stryker, a manufacturer of medical devices and equipment, recently recalled three versions of its automated fluid waste system, the Neptune, within the last year, after reports of serious injury and death. The Federal Drug Administration (FDA) has recommended all healthcare systems stop using the Neptune, which it has not approved.
Johnson is very clear about how the STREAMWAY System, which is FDA approved, differs from the recalled Stryker products. He says BioDrain’s device has a single regulator that can be adjusted manually and has a digital readout of the setting.
In comparison, the Stryker units had dual regulators, which sometimes resulted in hospital employees inadvertently using the wrong vacuum setting during a procedure. According to the FDA, this caused hemorrhaging and damage to soft tissue and muscle, and, in some cases, death.
To ensure these types of accidents do not occur, “BioDrain in-services each installation and trains all the users on how the system works, including how to adjust the vacuum level for each procedure,” Johnson says. “We have had no issues of incorrect use.”
Like a surgical cut, the vacuum and pressure of an automated fluid waste system must be precise. When designing the STREAMWAY System, engineers at BioDrain consulted experts in the automation field. SMC Corp. of America, which produces pneumatic technology to support automation, helped make the system accurate.
“We were able to utilize their knowledge base,” Johnson says. “We told them what we wanted to do. We wanted to shut this valve off as we were draining over here. We wanted to make sure that we have the continuous suction – how do we do this? They were very helpful, and they kind of steered us toward the type of valving that we needed, the kind of tubing that we needed. They basically made shorter work of our design.”
Custom Design
Engineers realized a lot of parts was necessary to make the STREAMWAY System function, from the tubing and the valves, to the software program. They also realized that it had to be designed to fit well in an operating room.
“There are currently a couple of powered canister system that are transported between OR procedure rooms,” Johnson says. “These systems are large units on wheels, very bulky, and take up precious space around the OR table.”
To avoid constructing a clunky machine, the engineers at BioDrain contracted an outside manufacturer for the original design. They told the manufacturer they wanted something compact that could be hung on a wall, or at least put out of the way of doctors and nurses. They said it had to look good, yet still hold all the components. And, according to Johnson, the manufacturer delivered.
![]() The machine offers continuous suction, and the collected liquid passes through a two-port filter system to prevent bone chips or other large materials from interrupting the machine from functioning. |
“We had a lot of help on that enclosure from our manufacturer,” Johnson explains. “They were very integral in helping us design that.
“They basically looked at what dimension we wanted to do. They took a peek and said, ‘Here are some ideas that we got. Here are the dimensions you have given us. Maybe we want to have this type of hinge on it? Maybe you want this to be the external piece?’ They actually did the CAD work on that for us, and we approved it.”
BioDrain also worked with Siemens to figure out how to program its proprietary software into the STREAMWAY System to power the device.
“From that point on, through them, we were able to contract out with some very knowledgeable programs that had worked with their products in the past and come up with their own in-house custom program,” Johnson says. “But they helped steer us the right way.”
CAD Systems
The STREAMWAY System incorporates more than 150 separate parts, including:
- PLC with HMI display
- PLC controlled solenoid valves
- Capacitive sensors for pump activation
- Peristaltic pump for evacuations
- Volume sensors for fluid measurement
- Polyurethane tubing
Before it became available to the market, though, the STREAMWAY System went through years of development and testing. Throughout the whole design process, BioDrain used Solidworks 3D modeling systems to create models to send to outside manufacturers who were designing parts for the machine. This ensured that each molded component had the proper fit. Johnson says CAD systems made sure the machine turned out according to the engineers’ specifications.
“Within two to three days we had an actual component that we could touch, feel, and look at,” Johnson says. “Our product managers and sales guys can show it to our customers and say, ‘Is this going meet what your requirements are?’ It has been very helpful.”
Final Product
The STREAMWAY System sucks operative fluid directly from the surgical field into the machine, which automatically measures and records volume before it disposes of the fluid directly into the facility’s plumbing system. The machine offers continuous suction, and the collected liquid passes through a two-port filter system to prevent bone chips or other large materials from interrupting the machine from functioning. The product includes automated cleaning, so a hospital employee never has to go near any potentially infectious material.
For Johnson, though, two of the STREAMWAY Systems’ biggest strengths come from its ability to reduce hospital costs and its ability to reduce a hospital’s environmental impact. Both of these benefits stem from eliminating the canister.
Aside from having to buy, replace, and handle canisters, hospitals also have to pay to get rid of them, because they are considered regulated medical waste (RMW). According to Johnson, RMWs typically cost 40 cents per pound to dispose of, meaning hospitals have to pay every time they throw away a canister.
Johnson also says the STREAMWAY System offers a green alternative to traditional fluid canisters, because “you do not have 50 million canisters a year going into the landfills.”
Result
Despite receiving FDA 501(k) clearance in 2009, BioDrain has not pushed the product until recently.
“We wanted to ensure that our product was top-notch before beginning the aggressive sales efforts,” Johnson explains.
![]() Engineers wanted a device that was compact and looked good, but still held all the components in an efficient manner. |
Representatives from the company showcased the STREAMWAY System at a booth at this year’s AORN (Association of periOperative Registered Nurses) Congress in San Diego, Calif. The annual event is the largest surgical products trade show in the United States. Thousands of nurses from across the world attend the event – exactly the type of audience BioDrain targets.
“Our booth was full all the time,” Johnson says. “We had a lot of nurses who typically handle the fluid waste management. They handle the canisters. They have to push these other powered canisters up and down the hall.”
Especially with the problems other automated systems are facing, designing, testing, and bringing a product like this to market can be draining. Using outside help from contract manufacturers, who can help with programming and modeling, can relieve some of the stress of the process, but until you get a thumbs up from a potential client, you are not completely unburdened. Johnson, even speaking over a telephone, cannot hide his excitement for how nurses received the STREAMWAY System at the AORN Congress.
“When they saw our product they were like, ‘You mean I do not have to touch anything? I do not need to handle anything? I do not have to mask up?’ They were very impressed.”
BioDrain Medical Inc., changed name to Skyline Medical
Eagan, Minn.
https://www.skylinemedical.com/
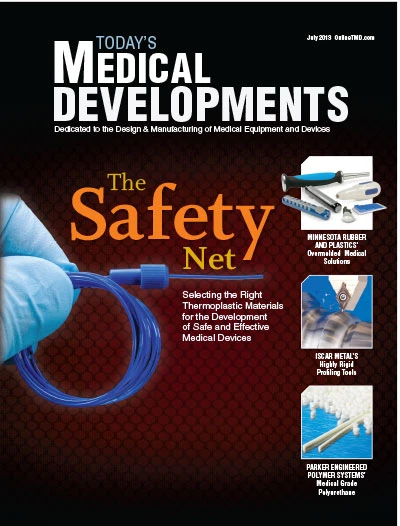
Explore the July 2013 Issue
Check out more from this issue and find your next story to read.
Latest from Today's Medical Developments
- Americhem’s EcoLube MD PFAS-free internally lubricated compounds
- German robotics and automation in a downturn
- Blueshift’s AeroZero
- November USMTO grow from October
- Platinum Tooling’s custom and special tooling
- Top 5 global robotics trends 2025
- Accumold’s micro molding innovations
- Methods Machine Tools, Multiaxis, announce AI solution investment