Plasma deposition is a simple, one-step process used to apply a thin, uniform film as a conformal coating, requiring no curing or use of solvents. In some cases, this eliminates the need for masking contacts and connectors, decreasing labor for what is normally a time intensive step in a coating process. A conformal coating is applied to any component requiring protection, and this coating seals over, in, and around all the elements on a device, delivering nano-level protection.
Semblant, the Chandler, Ariz.-based company offering its advanced plasma deposited process, is looking to change how components within medical devices – or even the entire medical device – will be coated to withstand a range of liquids it may encounter.
“It is not so much waterproofing as liquid-proofing. If you think about a hospital operating room or a regular hospital room, and you look at some of the equipment in that room, well, they all typically get wiped down with isopropyl alcohol (IPA),” says Steve McClure, vice president worldwide sales and marketing, Semblant. “As just one example, today’s devices needing protection from IPA seeping into the system during cleaning often will be enclosed within a protective housing. However, this adds an extra expense to that device.”
As an answer to help eliminate extra expenses while protecting sensitive componentry, Semblant offers its conformal coatings. The method implemented – plasma polymerization – and the means by which the material is deposited on the component came about in 2009 as Semblant was spun-out of U.K.-based PA Consulting. The polymer used for the coating process originally was geared toward protecting printed circuit boards, but soon it was obvious that it could be used elsewhere in the electronics supply chain.
“PA does a lot of research for government agencies in the UK, and one of the byproducts of their contract work was the development of this technology. In addition, through their agreements, the work and technology they develop they own, and with this research they saw its importance and decided to start a company around it,” McClure explains. “With the initial angle toward protecting printed circuit boards, it was realized rather quickly that this had applications in many other sectors, which is where we are today.”
McClure explains that they are currently in commercialization with various manufacturers who make instruments and devices. Some are evaluating the process to implement the conformal coat process while assembling the units in order to prevent gas-induced corrosion before the product is hermetically sealed.
So, how does the coating process work?
One-Step Deposition
With the technology developed, the next step in commercializing the process was collaborating with Nordson March for customized machinery. Taking some of the Nordson March base models and modifying them to Semblant’s plasma deposition requirement resulted in a set of customized machines delivering the coating required to the nano-level.
In a rather simplified explanation of the process, with the customized machinery in place, engineers at Semblant place the components on trays, load the trays into the machine (chamber), and close the doors. Next, the chamber is evacuated of all room oxygen until the inside of the chamber is a near-vacuum situation. Then, fluoropolymer process gas is pumped into the chamber and a RF voltage is generated, which energizes the gas and converts it to a solid polymer material, which attaches the devices in the chamber.
According to McClure, “Compared to traditional coating and finishing processes, this process uses 98% less energy, requires very little floor space, and eliminates the need for toxic chemicals. What results is a process that greatly reduces coating costs, risk to employees, and the chance of environmental concerns; reduces the need for high-trained operators; and simplifies the manufacturing process.
Differences, Benefits
McClure explains that anyone who is using a conformal coat process today could consider using Semblant’s technology. Beyond that, the segments where the costs or manufacturing process has been traditionally prohibitive to use a conformal coat, well, those sectors are now looking at this process because of the affordability and consistency of the results. One of the key differences between a traditional coating process and Semblant’s process is the need to mask certain areas in order to prevent the coating from negatively impacting its functioning. A traditional coating can affect the electrical, thermal, or mechanical performance of certain components, such as RF, LEDs, test points, etc. If they are coated, their functioning may diminish.
However, with Semblant’s process, these types of components can be coated without losing their performance requirements, saving time and money.
“Often, if a product has been coated with a traditional method during the manufacturing stage, but the final product requires testing and perhaps additional rework and fine-tuning, this traditional conformal coating will have to be completely removed to do the rework required, and then that entire section requires a recoat,” McClure notes. “So, additional labor-intensive work is required for both the removal and rework. However, with the Semblant process, users can simply remove whatever component is requiring this rework/fine-tuning, and then recoat the entire product with no heavy build-up. There is no need to waste labor removing a coating first.”
McClure compares the Semblant coating to Teflon, where it is very thin, compared to a parylene, which is thicker and more mechanically stiff. In addition, if thermal expansion is a concern, using a parylene could result in cracked solder joints, whereas Semblant’s coating is not affected by thermal expansion issues.
Down the Road
Some medical companies really began to take note as the conformal coat technology from Semblant gained traction in protection, McClure states. That is where Semblant’s engineers started to see some applications to offer device makers the mixed flowing gas protection. Not only is the technology and process RoHS and REACH compliant, but Semblant’s coating technology has the ability to protect any surface metal while delivering the corrosion protection needed.
Furthering their steps into the medical arena are various testing with device makers to see how the process performs beyond the need to protect from wash downs with IPA.
“The more we move into this, the more we are able to show that we are delivering the performance manufacturers need and are simplifying their work when using with Semblant’s conformal coat process. Still, in the future, we see many interesting uses for our process and materials within the medical sector. We have not yet studied human contact of our material, but you never know what will happen down the road,” McClure concludes.
Semblant
Chandler, Ariz.
www.semblant.com
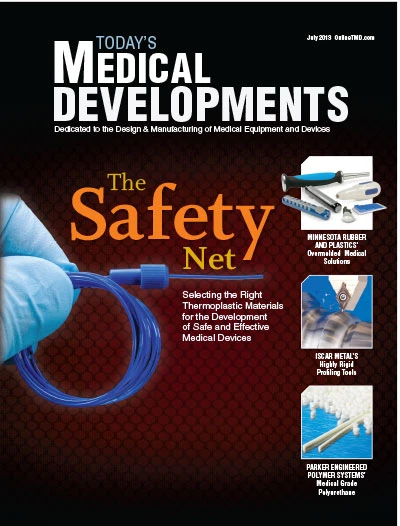
Explore the July 2013 Issue
Check out more from this issue and find your next story to read.
Latest from Today's Medical Developments
- Tariffs threaten small business growth, increase costs across industries
- Feed your brain on your lunch break at our upcoming Lunch + Learn!
- Robotics action plan for Europe
- Maximize your First Article Inspection efficiency and accuracy
- UPM Additive rebrands to UPM Advanced
- Master Bond’s LED415DC90Med dual-curable adhesive
- Minalex celebrates 60 years of excellence in miniature aluminum extrusions
- Tormach’s Chip Conveyor Kit for the 1500MX CNC Mill