Sine Parallels Make Angled Setups Easy
Now there is a fast and easy way to set up workpieces for machining at three common angles. Using Kurt’s Sine Parallels, clamping of rectangle parts occurs precisely and quickly at 30°, 45°, and 60° angles. The Sine Parallels also provide opportunity for clamping round workpieces.
The precision ground Kurt Sine Parallels increase the versatility of any standard 6" Kurt vise. They install and position quickly and easily with a single bolt for each plate, with no need to remove jaw plates – they remain in the vise while using the Sine Parallels. Following the initial setup, the Sine Parallels can change, quickly, to any of the other angles and used as a parallel.
Kurt’s Sine Parallels are ideal for any lot size from prototype to production. The Sine Parallels are a better and more cost-effective option than building a special fixture. They add versatility to any existing standard Kurt 6" vise at a modest cost.
Kurt and Production Tool and Supply will sell and distribute exclusively the new Sine Parallels for the next six months through their online stores.
Kurt provides a full range of standard workholding products, including custom engineered setups for virtually any need. Kurt’s product portfolio includes multiple station CNC vises, 5-axis vises, rotary table workholding for VMCs, plus a full line of tombstones for achieving maximum high density workholding.
Kurt Manufacturing Co., Industrial Products Division
Minneapolis, MN
kurtworkholding.com
Six-Axis Cleanroom Robots
An ISO 5 (class 100) cleanroom version of Denso’s VS-Series 6-axis articulated robots is now available. The VS-Series robots offer the world’s highest speed and precision in their class, with cycle times from 0.37 seconds to 0.33 seconds and repeatability from ±0.03mm to ±0.02mm. Reaches are from 500mm to 900mm and payload capacities from 4kg to 7kg.
The VS robots are extremely flexible, with an even more compact design than previous models, including ultra-slim arms to facilitate integration and a new optional bottom-side cable connection that saves valuable floor space. The robots can be mounted on the floor, ceiling, or wall, with no special hardware required.
An internal wiring option allows connection of gigabit Ethernet devices and servo grippers directly to the robot flange, preventing cables from becoming tangled or interfering with peripheral equipment. ANSI and CE safety compliance allows global deployment.
Typical cleanroom applications include assembly, dispensing, encapsulating and potting, insertion, inspection, laser welding, machine tending, material handling, nut driving, packaging, pick and place, press fitting, screw driving, soldering, test handling, and ultrasonic welding.
Denso Robotics
Long Beach, CA
densorobotics.com/products-vs- 6axis-new.php
Wire EDM with Cylindrical Drive Technology
The EDM MV Series line features design and engineering improvements, including non-contact cylindrical drive technology, an improved power supply, auto-threading, deeper submerged-wire threading capabilities, and more.
The cylindrical drive technology offers a simple, yet intelligent, design concept using a linear shaft motor. Mitsubishi’s round magnetic shaft creates a non-contact design using the full 360° of magnetic flux, delivering no wear, no cogging (inherent in flat plate systems), and no backlash.
A new servo control system uses a fiber-optic drive system with four times the communication speed for improved reaction time and accuracy. The Digital Matrix Sensor and V350 type-V generator specifically shapes the pulse to minimize electrode wear and decrease wire vibration, decreasing wire consumption while maintaining quality and straightness of the cut. Tests show up to a 60% reduction in wire consumption and 40% lower operating costs.
The head design features a flat-plate power feeder using an exclusive lever lock system, making it easier to index during operation. Without the need to open doors to rotate the carbides or realign wire, shops can realize significant time savings.
The series incorporates several design improvements to reduce overall operation cost. These include less expensive power feed design, larger wire drive rollers with more useable surface, reduced electrode wear for lower wire cost, optical drive plus LSM for reduced electrical consumption, and Sleep Mode function, which turns pumps off at night and restarts them in the morning to save energy and still have the machine thermally ready for operation.
MC Machinery Systems Inc.
Wood Dale, IL
https://www.mcmachinery.com/
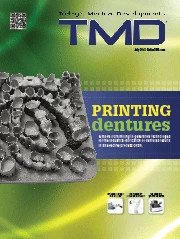
Explore the July 2012 Issue
Check out more from this issue and find your next story to read.
Latest from Today's Medical Developments
- #52 - Manufacturing Matters - Fall 2024 Aerospace Industry Outlook with Richard Aboulafia
- Tariffs threaten small business growth, increase costs across industries
- Feed your brain on your lunch break at our upcoming Lunch + Learn!
- Robotics action plan for Europe
- Maximize your First Article Inspection efficiency and accuracy
- UPM Additive rebrands to UPM Advanced
- Master Bond’s LED415DC90Med dual-curable adhesive
- Minalex celebrates 60 years of excellence in miniature aluminum extrusions