![]() |
Medical imaging systems contain so many high-tech electronic elements that it is all too easy to overlook the mechanical components that contribute to the success or failure of these systems. Consider linear bearings, for example.
Linear bearing are integral parts on a variety of imaging systems – from traditional X-ray machines to advanced systems such as magnetic resonance imaging (MRI), computed tomography (CT) and positron emission tomography (PET).
Typically, use of the bearings are to guide and support the motorized beds that position patients under the system’s scanning elements, though they are sometimes used for auxiliary motion axes, too.
Guiding a motorized bed is a seemingly simple task, but it is also a crucial one. If these linear bearings fail, they can take even the most advanced imaging system out of commission.
Failure in these medical imaging applications usually results when bearings are not truly robust enough to handle the heavy loads associated with the moving patient beds. With these loads routinely topping 3,000 lb, the bearings can all too easily become misaligned and wear prematurely.
There is another under-appreciated dimension to a successful bearing in medical imaging applications; the bearings have to operate quietly and smoothly, not just for the sake of image quality, but for the sake of patient comfort. Research has shown that mechanical noise negatively affects patients, increasing their anxiety levels and potentially triggering panic attacks in extreme cases.
![]() |
Misalignment can play a role here too by making bearings both sticky and noisy.
Throughout the years, development by Rollon Corp. has been in the area of a variety of different bearing platforms that can help cure the linear motion problems that can plague medical imaging machines. Here is a look at two rail systems that can handle the heavy-duty loads day in and day out.
Compact Rails
n this unique bearing design, the slider moves on large roller bearings that travel within profiled rails (see Figure 1). This arrangement offers three key advantages in medical imaging applications.
For one, the large roller bearings make for a system that is both space efficient and heavy-duty. The largest compact rails measure less than 2.5" high and can handle a maximum load of 3,400 lb, more than enough to accommodate a motorized bed rated of 500 lb with a safety factor of six.
![]() |
For another, the bearings are inherently tolerant of misalignment (see Figure 2). Design of the rail profiles have be specifically designed to allow the rollers axial freedom within the raceways. Depending on the styles of rail selected, this freedom can offset parallelism errors in either one or two axes. As the building of imaging machines occurs, this capability greatly simplifies the preparation of bearing mounting surfaces and installation of the bearings. Over the machine’s life, the misalignment tolerance helps reduce bearing wear.
Lastly, compact rail bearings are quiet compared to systems that rely on recirculating balls. In tests conducted by Rollon, compact rail sliders with ground raceways generated less than 70db of noise while traveling 2m/s with a 4,000N load. A comparable recirculating ball slider operating under the same conditions generated 86db.
![]() |
Telescopic Rails
Rollon’s semi- and full-telescopic rails feature a sturdy ball-cage design that allows them to extend well beyond their mounting structure with negligible deflection. The largest telescopic rails have strokes of more than 6.5ft in one direction – or 13ft in designs that telescope from two ends of a fixed intermediate member. Built from hardened or standard cold-rolled steel, these slides can take heavy loads that would shock any engineer who thinks that telescoping slides are just for drawers and cabinets.
To take an example of a semi-telescopic rail that is often used in medical imaging applications, Rollon’s ASN63-1970 rail can support a 10,000 lb load with negligible deflection even when extended by 50% of its overall length, to its full 40" stroke (See Figure 3). Using two of these semi-telescopic rails together doubles the load capacity to 20,000 lb.
Full-telescopic rails are also an option for even greater extensions. Rollon’s DMS63-2210 rail, for instance, has a fixed length of 87" and a total stroke of 89". When fully extended, a pair of these full-telescopic rails can support a 2,000 lb load with a maximum deflection of 0.5".
The most often found use for telescopic rails are in applications that require a low profile, simple, and cost-effective support for a cantilevered beds or imaging tables.
Rollon Corp.
Sparta, NJ
https://www.rollon.com/usa/en/
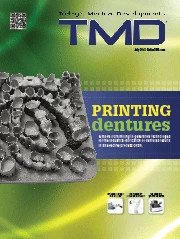
Explore the July 2012 Issue
Check out more from this issue and find your next story to read.
Latest from Today's Medical Developments
- Copper nanoparticles could reduce infection risk of implanted medical device
- Renishaw's TEMPUS technology, RenAM 500 metal AM system
- #52 - Manufacturing Matters - Fall 2024 Aerospace Industry Outlook with Richard Aboulafia
- Tariffs threaten small business growth, increase costs across industries
- Feed your brain on your lunch break at our upcoming Lunch + Learn!
- Robotics action plan for Europe
- Maximize your First Article Inspection efficiency and accuracy
- UPM Additive rebrands to UPM Advanced