![]() |
St. Henry, Ohio-based Tru-Edge Grinding Inc., started in 1996, has prospered designing and grinding cutting tools for metalworking applications. Recently, however, it has been applying its grinding expertise to surgical cutting tools. What it knows about tool grinding translates well into the medical field, delivering excellent results for its customers in shorter than typical delivery times.
With 14 ANCA CNC tool and cutter grinders on its manufacturing floor, Tru-Edge provides precision regrinding and reconditioning services, turnkey engineering, tool designing solutions, and custom and modified tool manufacturing options for medical, aerospace, automotive, and many other industries.
The growing company is ISO:9001 and ISO:13485 certified to perform medical grinding work, grinding the cutting tools for surgical instruments, supporting Tier 2 and Tier 3 medical suppliers with its tool grinding expertise.
The certification is about process control. Capability studies on the equipment, inspection processes specific to the medical industry, including documentation, are all complete – requiring greater detail than the standard ISO:9001 certification process.
Having ground more than 100 different surgical tools, approximately 10% of the company’s work is in medical. Earning the ISO certification will serve to strengthen its reputation in the industry while earning additional work.
“We do many different drills and reamers and have developed a lot of special fixturing for our ANCAs that allow us to do a variety of medical work. Our grinding experience helped us to come up with efficient, time-saving ways of shaping the surgical tools,” states Tim Knapke, owner/general manger.
“Cutting tools, in general, have geometry characteristics that, if you are not engaged in making cutting tools, would not be easily understood. That is typical of the medical device suppliers. Grinding cutting tools is not their core competency.
![]() |
“Some of the medical tool designs have not been around for more than a couple of years,” Knapke continues. “So a lot of learning is going on with new designs and prototypes; the tool designers are specifying increasing quality into the tools.”
Until a couple of years ago, production of the tools was by milling and turning with plenty of handwork due to much complex geometries. However, increasingly, medical device manufacturers are looking toward grinding to impart the geometry and finish required to the cutting tools, qualities that turning, milling, and handwork cannot match consistently.
“At Tru-Edge, we can put the material in the grinder and machine the tool complete in one setup, no deburring required. Cycle times may be an hour per part due to the complexity of a part such as a bone rasp and the number of teeth in the part. Previously, such a part would have required hours of cycle time across six processes from milling to turning, deburring, and polishing. We have taken hours out of the time required to produce a finished bone rasp,” Knapke says.
In order to do some of the more complex medical grind work, the ANCA software has been key. One of the parts Tru-Edge has been successful with is a bone rasp – the kind of medical part that, if you can do it successfully, you can do just about anything else, Knapke says.
“I have to say, the ANCA iGrind Medical software within the ANCA Toolroom suite is wonderful. We were a little skeptical at first; it seems like it would be a stretch for the machine to make the demo bone rasp, but it came out perfect on the first attempt,” Knapke continues. “It is a very complex part to produce on a grinding machine, as are other medical tools and implants.
“At times, the solid models of new medical parts we get from the customers are not always perfect and complete,” says Frank Seger, engineering product and development manager. “Nevertheless, ANCA went off those models to create a test grinding program for the rasp that worked very well. With that demonstration, we decided to invest in an ANCA to do other similar types of parts,” he says.
Of its 14 ANCA machines, Tru-Edge concentrates its medical production on the MX7 and TX7. There are four machines dedicated to medical production with room on the floor for more as production increases.
Optimization of the MX7 is to grind tools up to 25mm (1") diameter.
“With a wheel pack changer storing six HSK wheel packs, we have the flexibility to handle the different batches of stainless steel material, producing a number of different complex tools in a single setup, saving a good deal of cycle time,” Seger says.
![]() |
The TX7s are production-oriented machines with a 49hp spindle for precision grinding tough material. All machines in the Tru-Edge shop operate with the same software and any can run the medical part programs. It can also hold a Big Plus milling toolholder, so we could add that capability if we need to.
The medical tools are usually of 17-4 stainless. “We have learned a lot about stainless steel in the last few years,” Seger says. “It was a steep learning curve. Depending on the stainless material we are working with, vitrified CBN or standard CBN may be the best wheel.
“Stainless steel is a funny thing to work on. It does not heat treat well, having harder and softer spots in the same workpiece leads to burning, warping, and twisting during the grind, leading to part distortion,” Knapke says.
“But the parts need to be straight, burn-free, and burr-free. That is what makes the grinding process for medical tools a challenge – a challenge that milling and turning experts do not easily take on,” Knapke says.
“Tolerances within a few thousandths are one of the easier parts of the process for us,” Knapke says. “Inspecting the tools with a CNC comparator with downloadable DX files allows us to update offsets and helps produce parts with the highest level of consistently. All of which is traceable back to medical industry standards.”
Making a Difference
Certain options for the ANCA machines make them ideal for medical applications, assuring highly consistent grinding results. First, is ANCA’s in-process wheel dressing.
“We will never buy another machine without in-process dressing,” Knapke says, “due to the accuracy it affords our process. Part programs are based on a data point in the work area. In-process dressing allows the machine to know where the wheel surfaces are in relation to the data point and to the part at all times. The wheel imparts the form to the tool; automatically dressing cycles maintain its form consistently.
Grinding cycle times are also improved. By automating the stick dressing, there is a reduction in downtime during production, permitting unmanned production runs as wheel condition is maintained during the batch. Dressed wheels also permit high consistent feedrates.
In addition, importantly for stainless steel grinding, regular dressing of grinding wheels reduces tool burn and material damage, as well as ensuring open cutting wheels that reduce grinding forces and minimize spindle load.
ANCA’s software, known for its flexibility and user-friendliness, fully supports the white stick dressing process, ensuring removal of the least amount of wheel material.
Another option for medical tools, which can be very long and narrow, is the ANCA P-axis.
“With ANCA’s P axis working with the grinding wheel and steady rest, we are able to grind these long reamer-type parts successfully,’” Knapke says. “We will not buy a machine without it. It was out of the box perfect. Many of the medical cutting tools are complex and therefore difficult to hold in some cases, but the P axis eliminates that concern.”
The ANCA travelling steady provides the machine with an additional axis (P-axis) which, under CNC control, keeps the tool support directly underneath the point of grinding at all times. Keeping support under the wheel means complex operations on long slender tools is reliable and consistent.
“A conventional stationary support provides support on a short tool, but when you are manufacturing tools such as drills up to lengths of 400mm long, a stationary support will not provide the continual support along the entire length of the tool,” Seger says.
![]() |
Another key to processing the medical tools is Tru-Edge expertise in holding the odd-shaped workpieces.
“Medical drills come in blanked out,” says Seger. “We have created a way to hold onto the unusual quick-change shank of the tool, flute it out, and put a drill point on it with no distortion.”
The predictable, high quality of the medical grinding process at Tru-Edge is its overall key advantage.
“One of the first comments we got from our first medical tool customer when they saw the first part was “This thing dimensionally is flawless.” That is where the ANCA’s have simply shined,” Knapke points out. “We have three medical customers now, and would like to add three more on an ongoing basis,” he says. “We feel that is a good base goal. Six customers would fill this room with ANCA’s.”
With his company’s engineering innovation and attention to process quality, that seems a very reachable goal.
Tru-Edge Grinding Inc.
St. Henry, OH
tru-edge.com
ANCA
Wixom, MI
anca.com
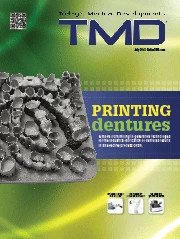
Explore the July 2012 Issue
Check out more from this issue and find your next story to read.
Latest from Today's Medical Developments
- US cutting tools orders decreased 2% from November 2024
- SMW Autoblok's Manual Jack connection kit
- MedTech Innovator welcomes five new industry partners
- First Article Inspection for quality control
- The manufacturing resurgence is here – are you ready?
- Workholding solutions for your business
- ZOLLER events will showcase the company’s cutting-edge innovations
- THINBIT’s MINI GROOVE ‘N TURN Acme threading inserts