![]() |
Top quality dentures, made in Germany without an expensive price tag. This, at first glance, seems to be a contradiction in itself. However, as you read on, you will see that it is not.
Laufer Zahntechnik GmbH, Mannheim, Germany, has managed to achieve this balancing act with the aid of an entirely new orientation of the process chain. Andreas Laufer, master dental technician and managing director of the company, gave us an insight into the tasks and direction of focus of a service company catering to the needs of the modern dental practice.
When it comes to manufacturing dental restorations, there are conventional techniques such as mold-based casting or milling from the complete workpiece, with milling currently being the most widely used technique. These manufacturing methods have weaknesses in terms of quality, take time, but above all tend to be expensive in relation to the unit costs. A milled unit costs approximately 19.90 EUR.
According to Laufer, his dental laboratory is able to offer the same unit manufactured via metal laser melting at a cost of 9.90 EUR.
![]() |
So, how is this possible?
Magic Word: Laser Fusing
Andreas Laufer focused, as a pioneer back at the end of the 1990s, on CAD/CAM technology – initially in the area of milling. Then, in 2003, generative metal laser melting technology sparked his interest. At this time, this represented an entirely new approach to manufacturing, whose charm Laufer recognized early on.
“The possibility to move from skilled production by a traditional method to an industrial scale was now achievable,” Laufer says.
This technology, which at the time was still in its infancy, promised a high degree of efficiency and economic viability taking account of the costs of employees, material consumption, and machine costs – thanks to the tool-free manufacturing method. In addition, the time taken to process an order from when receiving it through to delivery of the product to the dentist would see a drastic reduction as well. Another benefit was that a generative structure also means less reworking is required, the finest quality coupled with high precision, density and a great fit, as well as greater freedom of design.
Today Laufer works with LaserCUSING machines of the Mlab cusing type made by Concept Laser, Lichtenfels, Germany. Thinking outside of the box and having the courage to focus on manufacturing on an industrial scale is paying off for Laufer.
Who is Concept Laser? Concept Laser GmbH is an independent company that forms part of Hofmann Innovation Group GmbH, Lichtenfels, Germany. Since the company’s founding in 2000, it has worked across different sectors as a driving innovator in the field of metal laser melting technology using the patented LaserCUSING process. The term LaserCUSING, made up of the letter C from Concept Laser and the word FUSING (complete melting), describes the technology used: the fusion process generates components layer-by-layer using 3D CAD data. The generative process allows the production of complex component geometries without the use of any tools right through to complex structural geometries, which are very difficult to produce, if they can be produced at all, using conventional techniques. The LaserCUSING process allows the fabrication of both mold inserts with close-contour cooling and direct components for the medical, dental, automotive, jewelry, and aerospace sectors. Manufacturing is possible of both prototypes and mass-produced parts. Standard machines and customer-specific machine concepts for the LaserCUSING of metals are on offer. Full service as an option at Concept Laser means that customers can purchase machines for their own independent LaserCUSING application, or access services and development expertise (prototypes and small batches) directly. LaserCUSING opens up new perspectives in terms of quality, reproducibility, economic viability, and speed for more efficient product development many sectors. The machines make it possible to shorten development times and reduce development costs considerably. The key benefits of LaserCUSING include greater freedom of geometry, coupled with much greater flexibility in terms of product development. Another central advantage of the process is the opportunity to produce components without the use of tools and the obviation of the machine programming associated with this. The high quality standards, many years of experience and references of Concept Laser are synonymous with process-reliable and cost-effective solutions, which demonstrate their efficiency in everyday production. Thanks to ongoing further development, the unit costs of the generative process continually see a reduction in cost. |
Learning Curve
As a pioneer of this technology for dental laboratories, Laufer continuously optimized the internal processes in order to be able to manufacture quality products as inexpensively as possible. For example, today, Laufer manufactures its own build plates for the LaserCUSING process.
“This allows multiple usage with a long life cycle of up to 40 use cycles,” Laufer states. “Further technical progress was also made thanks to the further development of the CAMbridge software.”
This program allows, for example, automatic support generation and automatic positioning of the crowns and bridges on the build plate. The program CAMbridge places the dentures requiring manufacturing into position, automatically, in order to achieve a maximum packing density on the build plate.
“The data preparation can be carried out easily and conveniently. This saves time and money. The technology has now come of age. Today a dental laboratory can successfully complete the necessary initial training on how to use this CAD/CAM technology within just a few weeks,” Laufer explains.
![]() A clear user interface of the software, DentalDesigner, highlights the ease of use of the system. |
Paradigm Shift
The switchover to LaserCUSING paid off for Laufer, whose aim right from the outset was to transform the traditional artisan fabrication into industrial production. With fully automatic generative fabrication, on average, fabrication of 80 can occur, simultaneously, on one build plate per day. The enormous cost advantages of this method lies in the batch size. The labor costs can also reduce, significantly – instead of employing six or seven dental technicians for completely conventional cast fabrication, only four employees are now required to produce the same quantity of product using the generative metal laser melting process.
However, the fully automatic fabrication overnight not only speeds up the technical production time itself, but also offers an enormous saving in terms of time for dentists as service partners. As an example, they can take an impression of the patient in the morning and send it to the laboratory. At Laufer, the associated plaster-cast model first required creation and then scanning in, followed by design of the denture. Towards the end of the working day, the build job, which is prepared with CAMbridge, starts on the Mlab cusing machine. Fabrication then takes place, automatically, overnight. The next morning the denture parts receive a heat treatment at Laufer prior to detaching from the build plate. There is reworking of the individual pieces of work. This involves breaking off the support structures by hand and reworking the denture with a handpiece. After approximately two to three minutes, the denture is ready for shipping, or can have a veneer applied when further in-house work is required.
Dentists and patients really appreciate this timesaving procedure. Within the space of just two days, dentists can insert the dentures into the mouths of their patients, delivering a greater quality of life thanks to the quality and time saving available.
Metal Laser Melting The LaserCUSING process, a metal laser melting process, produces metallic components, which handle subjection to mechanical and thermal loading with high precision. Depending on the application, the materials used are high-grade and tool steels, aluminum or titanium alloys, nickel-based superalloys, cobalt-chromium alloys, and in future precious metals such as gold and silver. LaserCUSING involves fine metallic powder locally fused by a highly energetic fiber laser. Following cooling, the material solidifies. Production of the contour of the component is through direction of the laser beam using a mirror-deflecting unit (scanner). The component builds up, layer by layer (with a layer thickness of 20μm to 50μm), by lowering the bottom of the installation space, applying more powder, and fusing again. The special feature about the machines from Concept Laser is stochastic navigation of the slice segments (also referred to as islands) which processes successively. The patented process ensures a significant reduction in stresses within the component. For single-part fabrication, a maximum installation space of 300mm x 350mm x 300mm is available. |
![]() |
Looking to the future
The business at Laufer demonstrates that it is possible to deliver high quality coupled with high speed when doing business in Germany. Nevertheless, Laufer also sees many other opportunities for improving the process chain. The central point here is to generate the data via a mouth scan done at the dentist’s premises followed by printing of a plastic model. Using this method would allow carrying out two pieces of work in parallel: the printing of the model to check the fit and the construction of the denture.
Laufer sees important changes on the horizon with the materials too. Instead of finishing a metallic base with ceramic, as has previously been the case, it will be possible in the future to employ high-strength full-plastic solutions whose processing will then also take place using generative means, with laser fusing. Laufer seems to have a number of other ideas for the future.
The route that he has his company following, from process optimization, improvement of the process chain, and the industrial approach based on generative fabrication, demonstrate a clear path of growth.
Concept Laser GmbH (now owned by GE)
Lichtenfels, Germany
https://www.ge.com/news/reports/tag/concept%20laser
Laufer Zahntechnik GmbH
Mannheim/Friedrichsfeld, Germany
laufer-zahntechnik.de
In Brief Founded by Andreas Laufer in Schwetzingen, Germany, in 1989 is Laufer Zahntechnik GmbH. Since 1995, the company – finding its home in Mannheim, Germany, has been growing at a constant rate, becoming one of the biggest and leading dental laboratories in Germany. Specializing in sophisticated technologies in the areas of aesthetics, implantology, and above all combined dentures, the company is today an expert point of contact for more than 500 dental practices from all over Germany. Another persuasive factor is the great value for money that Laufer Zahntechnik offers its customers. The aim of manufacturing high quality, yet inexpensive dentures in Germany is now possible, and with great success. Jobs retention has remained, with new positions created each year. Documentation of good quality management is by the TÜV certification in accordance with DIN ISO 9001:2008, underscoring the company’s slogan of “Hightech – Made in Germany, Inexpensive – Reputable – Reliable.” The service provided by the company today includes more than just high-quality dentures. Additional services, in cooperation with other dental companies, are also available to dentists. |
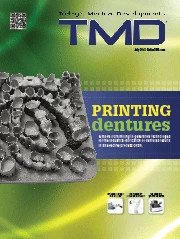
Explore the July 2012 Issue
Check out more from this issue and find your next story to read.
Latest from Today's Medical Developments
- Copper nanoparticles could reduce infection risk of implanted medical device
- Renishaw's TEMPUS technology, RenAM 500 metal AM system
- #52 - Manufacturing Matters - Fall 2024 Aerospace Industry Outlook with Richard Aboulafia
- Tariffs threaten small business growth, increase costs across industries
- Feed your brain on your lunch break at our upcoming Lunch + Learn!
- Robotics action plan for Europe
- Maximize your First Article Inspection efficiency and accuracy
- UPM Additive rebrands to UPM Advanced