![]() |
Instead of building a better mousetrap, a team of Rice University freshmen took a mousetrap and built a better way to treat dehydration among children in the developing world.
“The goal was to regulate the amount of fluid delivered to children so we could prevent over-hydration and under-hydration,” says Melissa Yuan, a member of the IV DRIP (Dehydrated Relief in Pediatrics) team and a mechanical engineering major. “It is designed to be used in severely underdeveloped parts of the world, where conditions can be pretty primitive, where they may not even have electricity.”
The challenge that sparked the innovative design has been mentioned by physicians working in Africa since Rice’s Rebecca Richards-Kortum and Maria Oden began traveling there six years ago in search of real-world design challenges for students in Rice’s Beyond Traditional Borders program. Richards-Kortum is the Stanley C. Moore Professor of Bioengineering and director of Rice 360°: Institute for Global Health Technologies, which oversees Beyond Traditional Borders. Oden is a professor in the practice of engineering education and director of the Oshman Engineering Design Kitchen.
“Many times physicians have mentioned to us that they would like a tool that can better moderate IV-fluid delivery to children, who are often connected to adult IV-bags,” Oden says. “In understaffed medical settings, monitoring IV-fluid delivery to patients can be a challenge. At the same time, it is of critical importance that the appropriate amount of fluid is delivered.”
The device costs about $20 to manufacture. A mechanical, durable, autonomous, and simple-to-operate volume regulator, it uses a lever arm with a movable counterweight similar to a physician’s scale to incrementally dispense IV fluid.
![]() |
The system uses the change in torque as an IV bag is drained of fluid to set off a mousetrap-like spring that clamps the IV tube and cuts off the flow the prescribed fluids. Tests have shown the device dispenses fluid within 12 milliliters of the desired volume in increments of 50 milliliters.
“We knew we needed something simple and reliable, not high-tech or terribly sophisticated,” Yuan says. “There’s nothing digital about it, nothing electrical or fancy.”
The team includes chemical engineering major Paige Horton, bioengineering majors Kamal Shah and Thor Walker, and mechanical engineering major Taylor Vaughn. Rebecca Hernandez, a senior in bioengineering, serves as the team’s apprentice leader representing the Rice Center for Engineering Leadership.
Walker emphasizes the old-fashioned engineering of the device: “There’s nothing revolutionary about this thing. It was matter of determining the right weight for the steel counterweight, which is 812 grams, and calibrating everything else correctly.”
The most time-consuming part of assembling the device is calibrating the counterweight and determining the spacing of the notches the counterweight falls into,” she says.
“Then the clamp goes off and it folds the tubing in a V-shape, the way you would crimp a garden hose to make the water stop coming out,” Walker says.
![]() |
This summer Shah and Yuan will transport four of their prototypes to Malawi and Lesotho, respectively, to test them under practical field conditions. Malawi, in southeastern Africa, is among the least-developed countries in the world, with a high infant mortality rate and a life expectancy of about 50 years. Some 1.5 million children in developing countries die annually of dehydration.
Conceived in the fall of 2011, the device was a freshman project in the Engineering 120, Introduction to Engineering Design course taught by Ann Saterbak, a professor in the practice of bioengineering education and director of laboratory instruction in Rice’s George R. Brown School of Engineering. Team IV DRIP has already received the 2012 Willy Revolution Award for Innovation in Engineering Design, sharing a $2,000 prize.
The team also won the $500 Best Freshman Design award at the 2012 George R. Brown Engineering Design Showcase.
Rice University
Houston, TX
rice.edu
To see the device in action, watch the video at youtube.com/watch?v=VlED86BWPcE&feature=youtu.be.
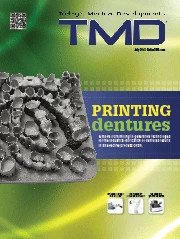
Explore the July 2012 Issue
Check out more from this issue and find your next story to read.
Latest from Today's Medical Developments
- Copper nanoparticles could reduce infection risk of implanted medical device
- Renishaw's TEMPUS technology, RenAM 500 metal AM system
- #52 - Manufacturing Matters - Fall 2024 Aerospace Industry Outlook with Richard Aboulafia
- Tariffs threaten small business growth, increase costs across industries
- Feed your brain on your lunch break at our upcoming Lunch + Learn!
- Robotics action plan for Europe
- Maximize your First Article Inspection efficiency and accuracy
- UPM Additive rebrands to UPM Advanced