Valveless, Ceramic Pumps
Solutions for metering high viscosity grease at low pressure for precision lubrication of industrial robot gearboxes are valveless, ceramic pumps, which maximize productivity and eliminate downtime. The PDS-100 Programmable Dispensing System utilizes a valveless pumping design to deliver gearbox lubricating grease accurately, while at pressures low enough to prevent any seal damage to the gearbox. The PDS-100 is available in both single and dual channel configurations. Dispense and metering rates range from a few microliters per dispense up to 768ml/minute continuous metering.
View how the valveless, ceramic pumps work at http://bit.ly/XhD66Q.
Fluid Metering Inc.
Syosset, N.Y.
www.fmipump.com
Multitasking Machine, Increased Efficiency
The Nakamura-Tome NTJ-100 multitasking turn/mill center offers fast tool changes compared to a full tool spindle ATC machine. A large tool capacity, up to 54 tool stations for turning and 24 tool stations for milling tools, reduces set-up time. For faster cycle times, the new NTJ-100 has two high rigidity turrets, each with a Y-axis – 3.5" (80mm) on the upper and 2.6"(65mm) on the lower, facilitating pinch turn and pinch mill operations. An upper turret swiveling B-axis with a range of 182° is ideal for easily producing angular features, eliminating the requirement for expensive angle milling heads.
The new NTJ-100 provides X-axis and Z-axis speeds of 787ipm and 1,574ipm, respectively. Designed with a minimum 7.9" (200mm) and maximum 35.8" (910mm) distance between spindles to eliminate any interference of tooling during multitasking, the NTJ-100 allows for multiple tools in the cut, simultaneously.
Methods Machine Tools, Inc.
Sudbury, Mass.
www.methodsmachine.com
Advanced Nozzle Technology Optimizes the Use of Coolant
Accurate targeting of coolant during machining provides maximum effectiveness in chip evacuation. However, precision and pressure are two equally important aspects of coolant. A high-precision coolant requires lower pressure. The higher the pressure, the more demanding applications can be machined with excellent results.
The coolant flows from the pump to the tool through nozzles directed exactly at the cutting zone. This produces a wedge of coolant that efficiently removes the heat from the cutting zone and forms the chip.
Low Pressure 7–10 Bar (100psi to 150psi)
When using low pressure, the Sandvik Coromant CoroTurn HP holders, with high precision nozzles, outperform regular tool holders that can have a tendency to flood coolant, making for improved chip control and better process security.
70–80 Bar (1,000psi to 1,200psi)
For demanding materials higher coolant pressures are needed, and the CoroTurn HP nozzle technology, in combination with the new SMC, MMC, PMC insert geometries, provides greater productivity.
150–200 Bar (2,200psi to 2,900psi)
Few machines provide solutions for these pressures; however, offered are standard holders and inserts that allow for up to 275 bar (3,900psi) of coolant pressure. Coromant Capto clamping units for high-pressure coolant, with 200 bar (2,900psi) coolant pressure capability, ensure that machine utilization is optimized through reduced setup and production time.
Toolholders
The Sandvik Coromant advanced cooling technology has been a solution primarily for customers using quick change with Coromant Capto, SL- and QS-holding system. Now, the same premium technology can apply with general shank tools, making it possible for everyone working with wet machining to utilize this highly productive coolant solution.
Watch a video on the solutions at http://bit.ly/10pCZsy.
Sandvik Coromant
Fair Lawn, N.J.
www.sandvik.coromant.com/productnews
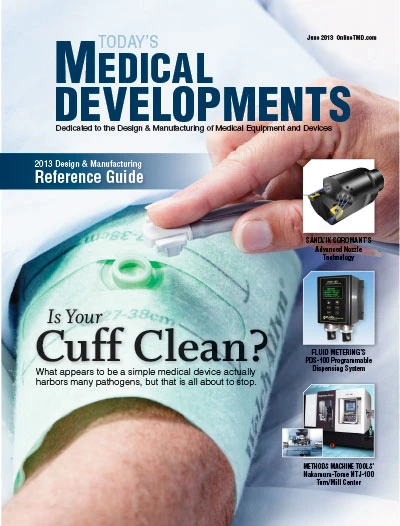
Explore the June 2013 Issue
Check out more from this issue and find your next story to read.
Latest from Today's Medical Developments
- Tariffs threaten small business growth, increase costs across industries
- Feed your brain on your lunch break at our upcoming Lunch + Learn!
- Robotics action plan for Europe
- Maximize your First Article Inspection efficiency and accuracy
- UPM Additive rebrands to UPM Advanced
- Master Bond’s LED415DC90Med dual-curable adhesive
- Minalex celebrates 60 years of excellence in miniature aluminum extrusions
- Tormach’s Chip Conveyor Kit for the 1500MX CNC Mill