![]() EcoCuff is durable enough to last for a complete patient stay, yet more cost-effective than most traditional disposable cuffs when used in a single-patient use setting. |
Most every adult knows the routine for a visit to the doctor; you are weighed, get your height checked, and then get your blood pressure taken. Now, many dentist offices are also starting routine blood pressure checks during a patient’s dental visits as well. Also, of course, when you check into the hospital for any procedure, monitoring your blood pressure is a regular part of the stay. This all seems harmless, just standard procedures for physicians and hospitals, but what about the germs?
“It is pretty well documented that there are bad pathogens found on blood pressure cuffs,” says Skaneateles, N.Y.-based Welch Allyn’s Senior Category Manager, Blood Pressure Products, Sean Karla. “For years researchers have cultured cuffs and found MRSA, C-Diff, and many other pathogens, so this is not a new problem. There is also a study showing a correlation between reusing blood pressure cuffs on multiple patients and increased C-Diff rates. So, some hospitals have acknowledged the connection between cuff use and hospital acquired infections, others have not even considered it – perhaps because cuffs may not be high enough on their radar screen – but there is certainly a patient safety issue related to reusing blood pressure cuffs on multiple patients.”
Welch Allyn engineers set out to design a cuff to optimize single patient use to address this problem, but its development answered more issues than just germs.
Other Challenges
It was determined that the product they needed to develop was the EcoCuff, which is a single-use patient blood pressure cuff to reduce the chance of cross-contaminating patients with the typical pathogens found on multi-use cuffs. However, designing a single-patient-use cuff posed other challenges for designers. For example, the cuff needed to be durable enough for a complete patient stay at a hospital, yet be affordable and minimize environmental impact. Designers at Welch-Allyn faced these problems head on, turning their attention to delivering a product that would help improve financial outcomes for hospitals while minimizing the overall environmental impact from hospital waste.
The most salient financial issue facing the EcoCuff is also the most beneficial to the patient’s safety: It is disposable, only meant for a single use. As such, hospitals will have to buy more of them, thus the increased cost for this commodity. However, Karla says the safety benefits far outweigh the product cost.
“Hospitals are well aware of that hospital acquired infections can cost $10,000 to $40,000 per incident. Therefore, the use of dedicated single-patient use products like blood pressure cuffs is an upfront cost many hospitals incur preventatively.”
![]() Offered in four sizes, compared to the traditional 10+ sizes, engineers tweaked length and depth to accommodate the changes in patient sizes these days. |
Most hospital-acquired infections are not covered by insurance. Therefore, hospitals often pay the costs of extended stays to treat the infected patients. Addressing the environmental impact presented similar obstacles.
“Anytime you use a product as one per patient, and you are using a high-volume product, obviously there is going to be an increase in raw materials and more materials thrown into the waste stream,” Karla notes.
Welch Allyn’s plan with EcoCuff was to minimize the amount of material utilized per cuff. However, the further the team progressed with development, the more it realized that the scope of the problem was bigger than just the material chosen. It was at this point that team members began to take a true product lifecycle analysis view – looking at raw materials, transportation of the raw materials, manufacturing efficiencies and energy use, actual shipment to the end user, and finally, end of life for the product.
To help with this, Welch Allyn employed the assistance of the Rochester Institute of Technology (RIT), Rochester, N.Y., and the Golisano Institute for Sustainability to conduct a product life cycle assessment. The study compared traditional disposable cuffs to the EcoCuff along the entire lifecycle. Results of the study determined an EcoCuff delivered 60% less environmental impact that traditional disposable blood pressure cuffs (see sidebar).
Life Cycle Assessment Welch Allyn’s EcoCuff, a single-patient-use blood pressure cuff, was designed to be environmentally preferable to previous models by using less material and consisting of one, homogeneous material. Welch Allyn needed a method to quantify the environmental impacts of three versions of its disposable blood pressure cuffs in order to determine environmental preference when used in a single patient use manner, identify areas for future improvement, and establish the optimal end of life strategy. New York State Pollution Prevention Institute (NYSP2I), part of Rochester Institute of Technology, Rochester, N.Y., performed life cycle assessments (LCA) of three Welch Allyn blood pressure cuffs in compliance with ISO 14040 and 14044 LCA standards. Each cuff was modeled with two end-of-life scenarios – landfill and incineration – to determine the optimal end of life management strategy for each cuff. LCA results show that the EcoCuff uses approximately 50% to 60% less energy and results in 50% to 60% less environmental impact than the other two disposable cuff models. LCA results were used internally and externally, and Welch Allyn experienced additional benefits. Internal Use of Results:
External Use of Results:
|
“The result is a product that is durable enough to last an entire patient’s stay, affordable enough that hospitals can actually use it in a one cuff per patient model, and from the environmental side, it has less impact on the environment and can even be recycled in some areas,” Karla explains. “We feel we have really designed the first single-use cuff that addresses the overall combined problem areas for most hospitals – controlling safety, cost, and environmental impact.”
Manufacturing Efficiencies
Standard blood pressure cuffs, those meant to last for years, are made primarily out of nylon, while some will have bladders from neoprene. Others on the market are made heavily out of poly vinyl chloride (PVC), but are also comprised of multiple other materials.
“Even though PVC is recyclable in some areas, most other cuffs are made out of so many additional materials that you cannot really take it in its entirety and recycle it,” Karla states. “You would actually have to deconstruct the cuff in order to recycle the materials.”
EcoCuff is 100% polypropylene, which, according to Karla, is typically considered a better material from an environmental perspective, and is gaining in popularity as a recyclable material. Many hospitals currently utilize polypropylene recycling for other hospital goods they purchase, and the EcoCuff recycling would fit right into that plan.
Beyond the material choice was the need to look at the manufacturing process to see how that fit with the project goal of developing a cuff that was eco-friendly from start to finish. Again, the RIT study came into play.
“Traditionally, most blood pressure cuffs are manufactured using RF welding, which requires significant amounts of energy. So it was that area that caught the most attention,” Karla explains. “We challenged the traditional methods to see if there were other ways to get lower energy welds with the same results, and ended up selecting a heat sealing process. That is just one example of the many steps we took to reduce the environmental impacts required during the manufacturing process, and obviously this required the company to invest in new machinery and equipment just for this product line.”
Design Details
Welch Allyn’s answer to the environmental concerns associated with single patient use is only one aspect of the overall EcoCuff solution. The company has also addressed the very complicated device and cuff compatibility problem within hospitals. Karla explains, because of the use of the Welch Allyn’s FlexiPort system, hospitals can standardize virtually all of their blood pressure devices to work in harmony with EcoCuff and all other cuffs in the FlexiPort line. This helps make single patient use possible since patients are commonly transferred from department to department throughout hospitals during their stay.
Before FlexiPort, clinicians had to make sure the cuff they were using could connect to the blood pressure machine they had. Often, a hospital would have many different brands of blood pressure machines – some with one tube connections, others with two tubes; some with connectors that screw together, others with bayonet-style fittings. The confusion as to what cuff fit with what machine is not what clinicians need to spend their time determining.
“If you look at the side of FlexiPort cuffs you will notice the clear, plastic looking ring. Now, on the blood pressure device side, there is a matching fitting, which just clicks into that port on the cuff. It may not look like that much of a revolution, but many hospitals have now moved to this connection method and it has eliminated the confusion of finding the compatible cuff for the device at hand,” Karla explains.
To further reduce the difficulties clinicians face while searching for the right blood pressure cuff, Welch Allyn made changes to the EcoCuff cuff sizes.
“One of the big challenges of any blood pressure cuff manufacturer, and from a clinician’s perspective as well, is that patients, in general, are getting larger, their arms are getting larger in circumference, but not in length. Therefore, the space between the armpit and elbow is defined and designing a cuff to fit correctly in the space with the growth in circumference is a challenge,” Karla says. “So, when the design engineers worked on the EcoCuff, they reduced the number of sizes from the normal 10+ down to just four – trying to optimize these sizes based on a vast amount of data on patient limb circumference and arm lengths.
“The end result is a cuff that is slightly longer and wider, and one that is tweaked to fit this growing patient population while still adhering to the latest clinical sizing standards. In addition there was attention to the placement of the slot on the one side of the material, so that as a clinician wraps the EcoCuff around a patients arm, the FlexiPort on it will only fit through the slot if the cuff is appropriately sized, further ensuring that proper fit and reading is achieved.”
Welch Allyn took the time to look closely at blood pressure cuffs, products many would consider simple, to determine how it could be made better. The result of this effort is a cuff that offers improved safety features, addresses growing medical costs, and is environmentally preferable. In addition, since many hospitals have standardized to the FlexiPort system, these connections are readily available in facilities to connect to the EcoCuff, making a switch seem rather seamless.
“All of the improvements Welch Allyn made to EcoCuff will help facilities implement a single patient use model to improve patient safety, make it more affordable, and reduce the environmental impact compared to traditional disposable cuffs, a real win-win for people inside and outside the hospital as well,” Karla concludes.
Welch Allyn
Skaneateles Falls, N.Y.
www.welchallyn.com/cuffs
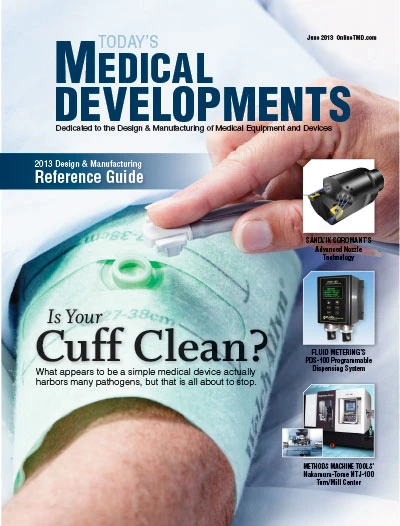
Explore the June 2013 Issue
Check out more from this issue and find your next story to read.
Latest from Today's Medical Developments
- Tariffs threaten small business growth, increase costs across industries
- Feed your brain on your lunch break at our upcoming Lunch + Learn!
- Robotics action plan for Europe
- Maximize your First Article Inspection efficiency and accuracy
- UPM Additive rebrands to UPM Advanced
- Master Bond’s LED415DC90Med dual-curable adhesive
- Minalex celebrates 60 years of excellence in miniature aluminum extrusions
- Tormach’s Chip Conveyor Kit for the 1500MX CNC Mill