Powerful Machining Software Programs
Designed to program Swiss-style NC machines, Mastercam Swiss Expert is popular with the medical device and dental industries, where extremely small but very precise parts are required. Mastercam Swiss Expert supports an unlimited number of axes and channels, and can be used for realistic simulation of the entire machine and its tools. Ideal for optimizing cycle times, Mastercam Swiss Expert also supports all types of tooling.
Mastercam’s Mill-Turn product makes machining on today’s high-powered turning centers and full-function machining centers simpler than ever before, streamlining the programming process with intelligent job setups that are keyed to the exact machine in the shop. Intelligent work plane selection makes it easy to choose the proper spindle and turret, and program the part with Mastercam’s proven milling and lathe tool paths.
Mastercam X7 Preview – Q2 2013:
- Tool Manager provides a new way to create and organize tooling.
- Improved Backplot and Verify utilities offer a more efficient workflow and more comprehensive tool path support.
- Dynamic and OptiRough tool paths deliver more efficient tool motion, including faster calculation times.
- Multi-threading support extends to most 2D high speed tool paths, delivering faster toolpath processing.
CNC Software Inc. (Mastercam)
Tolland, Conn.
www.mastercam.com
Adding Complex Geometries to Simple Shapes
The LaserCUSING process produces intricate geometries and profiles in a variety of materials on components, and in many instances, manufacturing of these are from scratch within the LaserCUSING machine. However, there are a growing number of cases where the technology is used to produce hybrid parts, often with dissimilar metals.
A recent example of use of the LaserCUSING machine is an intricate bronze lattice built upon stainless steel washers, and super glued to a base plate. In this case, the stainless steel washers glued to the baseplate are roughly measured to establish their center positions.
Using MAGICS software, the CAD STL model for the bronze lattice tops is imported and the rough positions used. The build platform is located on the machine and the CAD slicing program is then imported. The next step is to load the bronze powder, which is leveled to the top of the stainless steel washers, establishing the Z start position. The laser in a low power mode is used to produce what is known as a ghost layer. This allows verification of positional accuracy prior to the commencement of the build process. Once the build process is complete, the unused bronze powder is sieved, ready for use in the next cycle, and the finished parts are removed from the build platform.
Concept Laser (now owned by GE)
Lichtenfels, Germany
https://www.ge.com/news/reports/tag/concept%20laser
Achieving Optimum Cleanliness Standards
The Duo 400, a compact, fully automatic, self-contained aqueous cleaning system, meets the highest visually clean and dry cleanliness/inspection standards and is ideal for cell manufacturing or within a centralized layout. The Duo 400 measures just 60" x 64" x 89", delivering a small footprint, and the highly versatile single chamber rotational cleaning system features immersion/spray wash, spray rinse, and hot air dry. MecWash aqueous technology cleans without solvents or emissions, and is effective at cleaning large and small components in purpose-built fixtures or standard size stainless steel baskets and plastic totes.
The Duo wash chamber includes more than 100 high-volume jets that thoroughly penetrate and saturate the workload at more than 130gpm. The temperature of the wash and rinse waters can be set at the operator’s discretion between 140°F and 190°F. Full rotation of the workload at 3rpm exposes all surfaces to the wash and rinse solutions to ensure effective cleaning, draining, and drying. Alternately, when cleaning parts with delicate geometries, programming of the system can deliver gentle oscillation from side to side.
The unit’s flood and spray wash cycles are followed by the spray rinse cycle. Afterward, a high velocity blow dryer raises the temperature up to 285°F to dry all faces of the given components’ surfaces.
MecWash Systems
Aurora, Ohio
www.mecwash.com
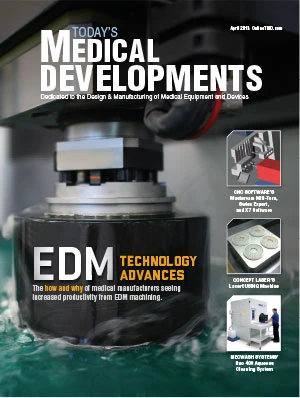
Explore the April 2013 Issue
Check out more from this issue and find your next story to read.
Latest from Today's Medical Developments
- Tariffs threaten small business growth, increase costs across industries
- Feed your brain on your lunch break at our upcoming Lunch + Learn!
- Robotics action plan for Europe
- Maximize your First Article Inspection efficiency and accuracy
- UPM Additive rebrands to UPM Advanced
- Master Bond’s LED415DC90Med dual-curable adhesive
- Minalex celebrates 60 years of excellence in miniature aluminum extrusions
- Tormach’s Chip Conveyor Kit for the 1500MX CNC Mill