Oncology is a field where high-end motorization is essential. Equipment is getting continuously more sophisticated and precise, creating the need for advanced motion and automation. Superior motorization solutions are required to meet medical industry standards as well as to provide a cutting edge differentiation and advantage to OEMs launching new devices. Miniature electric motors are helping to improve the detection and treatment of cancer by advancing biopsy, imaging, and radiation treatment. As oncology techniques continue to become less invasive, more accurate, and effective, use of miniature electric motors will remain a driving force in cancer management evolution.
Recently, advances in attaining breast tissue samples using miniature motors have helped make breast biopsy procedures less invasive and intrusive. Thousands of women undergo breast biopsy procedures every day. In the past, a biopsy was an anesthesia based invasive procedure that often resulted in long recovery times, visible incisions, and scarring. The use of a scalpel and sutures in a surgical or operating room setting helped increase the stress of the procedure for a patient. However, recent improvements in the ways breast biopsies are performed have helped advance the efficiency of the procedure and minimize the discomfort and stress to the patient.
By using new devices powered by miniature motors, breast biopsies are faster, less invasive, and with a significant reduction in recovery time. By using a powered device, a physician is able to collect and analyze multiple tissue samples from a single biopsy site. New powered biopsy tools are able to withdraw multiple tissue samples from one small, typically sutureless incision. New powered biopsy procedures have shown to minimize biopsy incision size by up to 85% and shorten overall procedure time up to 75% compared to the more traditional scalpel method. By minimizing the incision site, physicians are also able to minimize scarring, eliminate sutures, and effectively reduce physical recovery time. Using a fully powered device also allows physicians to sort and organize multiple samples from one procedure more efficiently by using remote positioned pre-labeled sample compartments to collect and organize multiple samples from a single biopsy site. By capturing and organizing samples more effectively, physicians can improve the accuracy and reliability of sample analysis.
![]() |
Performance Answers
Customizable slotted brushless DC gear motors are an excellent match to achieve the performance requirements needed by powered biopsy devices. The slotted BLDC motor technology provides extremely high torque in a small package, which enables design engineers to minimize the motor package and make the handheld device as small and light as possible. Additionally, slotted brushless products also offer exceptional efficiency, which further shrinks the end device size by allowing design engineers to use smaller batteries.
Miniature electric motors have also helped to make imaging during biopsy and radiation more precise and accurate. During radiology procedures, injectors add contrast agents into a patient’s vascular system to improve the readability of scanner images, helping radiologists minimize the total amount of radiation delivered to the patient.
Surgeons frequently use control-agent-assisted imagery to prepare for a procedure, during a procedure, or to evaluate the effectiveness of a prior procedure. As an example specifically related to cancer detection, radiologists use control agents to help provide computer-aided images to guide biopsy procedures. Depending on a patient’s target body area, age, weight, and chemical absorption rate, radiologists fine-tune contrast agent injection patterns and scanner parameters to achieve the best image possible while simultaneously minimizing the amount of radiation a patient receives. For example, a young patient with good absorption capacity will receive a strong injection concentration in order to allow a minimum radiation dose during scanner exposure. In contrast, a senior patient who is less capable of absorbing the contrast agent will receive a weaker agent injection but a higher scanner exposure and associated radiation dose to obtain an appropriate imaging result. In order to customize each patient’s agent injection, the injector module must be able to accommodate different injection flow rates and processes. The fact that contrast agents are typically viscous, even when preheated to the body temperature, narrows the choice of an injector drive. Frequently, ironless brush DC motors are a good choice for an injector drive because they achieve higher power density than ironcore motors, helping inject the thick contrast agent into the body properly. Higher power density for ironless brush DC motors compared to ironcore motors also helps reduce motor size to allow for a more compact design envelope. Ironless brush DC motors are also typically more efficient and responsive compared to ironcore motors. Improved efficiency helps ironless motors optimize battery operation and life to help improve the performance of mobile injection devices. Ironless motors also usually have lower rotor inertia and no detent torque which helps improve the control of agent delivery.
![]() |
There are numerous brush-DC products that can meet the necessary control agent delivery needs and help facilitate improved imaging results. For example, Portescap’s standard 35GLT motor is 35mm in diameter and capable of delivering more than 155mNm of continuous torque. Additionally, some applications feature enough available room to use stepping motors. The technical advantage of a stepping motor compared to a brush DC motor is that a stepping motor provides precise positioning and can be driven in open loop to achieve torque at low speeds (1,000rpm and below). In comparison, a brush DC solution will need an encoder attachment and a gearbox to provide precision positioning and low speed torque for the same application. An additional advantage is that a stepping motor solution is typically less expensive than a brush-DC solution. Motion providers that can offer both brush DC and stepping motor technologies, as well as relevant gearbox and encoder options, can present a number of possible solutions and help OEMs select the best technology and product combination to precisely meet the requirements of a given application.
![]() |
Miniature motors are also helping to improve cancer treatment. Collimators that control the shape of a radiation beam during radiation therapy use miniature electric motors to move radiation blocking elements (usually lead or tungsten leafs) into discrete positions to form the shape of the beam that a patient is exposed to during treatment. The shaped beam rotates around a patient to expose different angles of the targeted malignant cells. In order to adapt to the changing shape of the exposed malignant cells during rotation, and minimize radiation exposure to nearby healthy cells, the collimator continuously adjusts the blocking elements to modify the shape of the radiation beam precisely. Collimators require extremely reliable, high-torque-density electric motors. While a collimator is in operation, its blocking elements are typically in continuous motion resulting in heavy use of the motors that drive the elements. Additionally, many collimators have months of patient backlog in treatment centers and cannot afford machine downtime. These two facts – combined with the importance of ensuring that all blocking elements are working properly to eliminate any unnecessary patient radiation exposure – result in the need for exceptional motor reliability. Collimator motors also need to have high torque density to achieve performance and size requirements. Collimators usually use one motor per blocking element and may contain up to 160 elements. High torque density and efficiency allows motors to be smaller to allow all 160 motor drives to fit within a relatively small area. Eight millimeter or 10mm brush or brushless DC motors with matching planetary gearboxes and magnetic encoders are often the choice for the motion solution used to drive collimator-blocking elements.
![]() |
Array of Options
The following range of motor options from Portescap matches some of the applications previously mentioned.
Ironless brush DC motors: With both precious metal and graphite commutations, ironless motors typically offer up to three times more torque than similar size conventional ironcore motors. This is possible because there is no iron armature in Portescap’s brush DC options, so the rotor generates no iron-losses while rotating. Also, having no armature opens up room inside the motor for utilization by the permanent magnet in order to reduce the overall motor diameter and increase motor torque density. This brush DC product line also offers longer life than conventional iron-core motors by eliminating commutator arching and achieving low current consumption through removing detent torque and attaining low winding resistance.
Brushless motors: Offering both slotted and slotless brush DC motor designs to the market, brushless motors are typically used for high speed and long life applications. Brushless motors can be optimized for motor operating speeds up to and in excess of 80,000rpms. Slotted designs are frequently used for high torque applications, and often power both autoclavable and non-autoclavable surgical hand tools. Slotless motors are frequently used in high-speed lower torque applications where long life, high performance, and efficiency are vital. Both slotted and slotless designs can be tailored to meet a customer’s exact working point. Working hand-and-hand with highly trained and experienced application and design engineers to choose the motor technology and product features to exactly meet customer’s need and facilitate end product success in the marketplace is a must. Stepping motors: Can stack, hybrids, and disc magnet stepping motors often find use in precise positioning applications. Can stacks are used for their simple construction and wide application. Hybrid motors are often used for higher torque density applications, while disc magnet motors find use in advanced positioning and response. Typical applications for stepping motors vary widely. Some frequent applications are fluid handling, diagnostics, and infusion systems.
![]() |
Portescap
W. Chester, Pa.
www.portescap.com
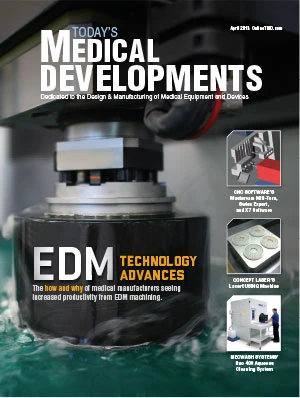
Explore the April 2013 Issue
Check out more from this issue and find your next story to read.
Latest from Today's Medical Developments
- Tariffs threaten small business growth, increase costs across industries
- Feed your brain on your lunch break at our upcoming Lunch + Learn!
- Robotics action plan for Europe
- Maximize your First Article Inspection efficiency and accuracy
- UPM Additive rebrands to UPM Advanced
- Master Bond’s LED415DC90Med dual-curable adhesive
- Minalex celebrates 60 years of excellence in miniature aluminum extrusions
- Tormach’s Chip Conveyor Kit for the 1500MX CNC Mill