![]() |
From its modest beginning in 1946 as a general screw machine company, Superior Products LLC has grown its product lines to serve the welding, medical, beverage, cryogenic liquid, and specialty gas industries worldwide with fittings, manifolds, and assemblies. Superior’s product range includes about 3,000 unique parts, which are developed and manufactured at the facility in Cleveland, Ohio. The company machines 10 million to 15 million pieces annually, which are primarily made of brass and stainless steel. After machining, the contamination of the parts comes from chips and swarf, as well as cutting fluids and oils.
A Critical Step
As use of the parts are in connection with compressed gas in industrial, medical, and specialty gas applications, they require cleaning to an oxygen clean standard. The Compressed Gas Association (CGA) allows no more than 47.5mg/ft2 of organic material on the parts.
“If a dirty part is used in an oxygen system there is a chance of fire, because it is compressed gas that can lead to explosion. For quality and safety, it is critical that cleaning is done properly,” Iain Hodgekins, general manager, Superior Products, explains.
![]() |
The previous system used by Superior Products, a nitric acid bright dip cleaning system, reached a level of about 17mg/ft2 or 18mg/ft2. Although it satisfied the cleanliness requirement, the cleaning system was about 30 years old, and many parts had to be re-cleaned. The system also used about 2 million gallons of water annually that required processing for heavy metals in the wastewater.
“It was a necessity to replace the cleaning system. We wanted a new system that would allow us to drastically reduce the impact on the environment. Additionally, we wanted a more reliable cleaning process that would require less re-cleaning and improve our efficiency and quality,” Hodgekins says.
The Decision
For selecting the appropriate cleaning solution, Superior Products’ engineers evaluated available cleaning procedures – from aqueous methods to solvent-based techniques – and talked to several cleaning machine manufacturers. Based on cleaning tests conducted at Dürr Ecoclean’s facility in Wixom, Mich., Superior Products decided on the Universal 81C, a solvent-based, closed-loop cleaning system that uses no-chlorinated hydrocarbons.
“With this closed-loop system we have achieved excellent cleaning results, we do not need water for cleaning, and we have no wastewater management issues. Dürr also came highly recommended,” Hodgekins explains. “We are part of the Precision Machined Parts Association (PMPA) and some association members recommended the Dürr machine over others, due in part to Dürr’s having local U.S. support and good service when service was needed.”
Improved Cleaning
Quality The Universal 81C is a single-chamber cleaning system, which operates completely under vacuum. This eliminates the need for additional explosion protection when using combustible solvents such as isoparaffinic hydrocarbons. Additionally, the machine offers multiple monitoring of safety-relevant temperatures and pressures.
The Superior Products system is equipped with three flooding tanks for coarse and fine cleaning, as well as for application of a conservation fluid specifically for the brass parts, ensuring that parts do not tarnish over time. Configuration of the cleaning machine is for a multi-stage process comprised of cleaning, rinsing, steam degreasing, and drying. Using the standard high-performance injection flood washing (IFW), and an optional ultrasonic system, the unit can perform complex cleaning tasks with high process reliability. A user-friendly design feature is the machine’s ability to store eight freely programmable and selectable cleaning programs in its controller. The parameters include rotating and swiveling movements in the cleaning and drying chamber, temperature settings, ultrasonic characteristics, and IFW settings. In this way, the cleaning treatment can be customized to every part batch.
Hodgekins explains, “We are currently using three programs, and we are very satisfied with the cleaning results. There are no parts which need to be re-cleaned, and the cleaned parts surfaces show a rest-level of organic materials of only 5mg/ft2 to 6mg/ft2. Compared with our old system’s results, contamination has dropped by two-thirds. This gives us very good peace of mind knowing that the machine is cleaning well above the standard.”
The vacuum drying technique ensures that even parts with a complex geometry – e.g., bores, blind holes, and undercuts – emerge from the process fully dried.
The fully automatic vacuum distillation unit, as well as full-flow and bypass filtration – which come as standard – remove oil and grease, chips, and swarf from the solvent on a continuous basis. Therefore, the cleaning fluid lasts a long time without needed to be changed.
Cleaning & Drying in a Closed System As highly effective cleaning media, non-halogenated hydrocarbons allow safe and economical use of solvents for removing oils, greases, emulsions, and swarf between or after manufacturing processes. Because of its many different process variants using hot and/or cold immersion with downline vapor degreasing, the sophisticated technology of the Universal 81 C cleaning system is ideal for meeting the requirements expected of modern manufacturing processes with regard to quality and functionality. Removal of large quantities of oil or swarf, from mass-produced parts or particles of dirt with a defined size in fine cleaning, can be achieved by selecting the appropriate filtering system and other application-dependent optional extras. Equipment & Process
Options
Advantages
|
Fully Automatic; ROI Within Two Years
Depending on part geometry and sensitivity, cleaning of parts is in bulk-baskets or arranged in pin-racks to carry the parts throughout the shop. Four of the baskets or pin-racks can be loaded into a carrier system, specifically designed by Dürr Ecoclean. Transportation of the batches into the machine’s cleaning chamber is by an automatic conveyor feeding system, which identifies the products by a proximity sensor and chooses the appropriate cleaning program automatically.
“After looking at the additional cost for the proximity sensor, I do not know why it is not included with every automatic conveyor system. We can not only put anybody in the company on the cleaning machine and they will do a good job, the proximity sensor also saves a lot of manual labor,” Hodgekins reports.
Depending on the program, the cleaning cycle takes between 8-1/2 and 9 minutes to complete. When the batch comes out of the machine, it travels down a track to go into the inventory.
According Hodgekins, the old system required two operators for eight hours a day to clean parts. Due to the fully automatic cleaning process with the Universal 81C, the manual labor for cleaning has dropped to one hour per day.
“We save the equivalent of 15 hours’ work each day. Additionally, the new cleaning process saves us 2 million gallons of water annually and the associated wastewater treatment. Taking these savings into account, the return on investment on the machine is conservatively about two years,” Hodgekins states.
Although the reduced impact on the environment cannot be rated in dollars, Superior Products reached its environmental goals, and that gives the general manager a good peace of mind too.
Dürr Ecoclean Inc.
Wixom, Mich.
www.durr-ecoclean.com
Superior Products LLC
Cleveland, Ohio
www.superiorprod.com
View Dürr Ecoclean’s range of products for a variety of cleaning needs at http://bit.ly/10lzhzT.
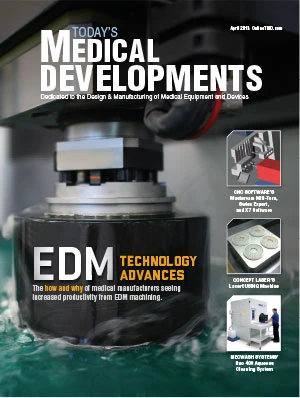
Explore the April 2013 Issue
Check out more from this issue and find your next story to read.
Latest from Today's Medical Developments
- Tariffs threaten small business growth, increase costs across industries
- Feed your brain on your lunch break at our upcoming Lunch + Learn!
- Robotics action plan for Europe
- Maximize your First Article Inspection efficiency and accuracy
- UPM Additive rebrands to UPM Advanced
- Master Bond’s LED415DC90Med dual-curable adhesive
- Minalex celebrates 60 years of excellence in miniature aluminum extrusions
- Tormach’s Chip Conveyor Kit for the 1500MX CNC Mill