The movie and TV show “Lost in Space” included a robot that worked shoulder to shoulder, and even talked, with the Robinson family. Today, that is more than a fabrication on film. Sophisticated robots are easier to use, safer around employees, and lower in price, making them a viable and competitive option for small and medium manufacturers.
Easier, Safer, as Cost Effective
Often perceived only for large companies, robotics are proving beneficial for small and medium enterprise operations today.
“We hear three common questions about robotics,” says Thomas Rilke, CEO, Deutsche Messe Robotation Academy and director, Metropolitan Solutions trade fair. “Is it too complicated? How safe and easy is it for employees with no robotics experience? How can I integrate it into my operation?”
Uniquely positioned to answer these questions, the Robotation Academy, a robotics and automation teaching facility in Hannover, Germany, offers a learning experience for manufacturers unlike any in the world. Visitors can experience robotics in a simulated manufacturing environment, supported by more than $2.5 million of equipment and sponsored by Deutsche Messe, organizers of HANNOVER MESSE, the industry’s largest manufacturing trade fair, and leading manufacturers such as Volkswagen International.
“Many visitors realize robotics is actually less complicated and expensive,” Rilke explains. “They want to test out the latest generation to understand how to safely integrate robotics into their operations. At the academy, visitors are able to network with experts for answers to their top concerns.”
Easy to Operate, Simplified Integration
One of the most common questions asked at the academy and to robotics manufacturers is about complexity, particularly for employees. Employee interaction has become much easier because robots have all sorts of screens, just like personal computers.
![]() |
“Robots today are much more elegant due to advancements in software,” says Tim DeRosett, director of marketing, Yaksawa America, Motorman Robotics Division. “The desire is to be similar to programs on a PC like Word or Excel. No programming is needed, and you simply get right to work on your manufacturing application.”
“The ease-of-use surprises manufacturers,” explains Thomas Visti, CCO/vice president, Universal Robots. “I compare it to using an iPhone, where everything is controlled by a touch panel. You simply press a button to move the robot arm with no coding required. Our robots can also be programmed by physically moving the arm, showing the robot the desired movement.”
In addition to less complexity for employees, robotics companies have also made it easier to integrate into operations.
“There is a perception that you need a robotics expert on staff, which is not necessarily the case today. We have developed a software interface to enable customers to deploy robots with Rockwell Automation’s RSLogix, that integrates with many products and is already familiar to existing staff,” DeRosett states. “Because of this, robotics integration is much more like an appliance where you follow operational instructions versus complicated programming.”
Improvements in Safety, Flexibility
Technological advances have also improved safety and reduced the need for fencing, containing the robot in a fenced in area.
“Safety remains a strong concern, and we demonstrate intelligent safety systems at the academy. For example, a camera underneath the robot identifies where people are working. The robot knows from both the camera and sequences in software when to warn people of movement and when to halt operations,” Rilke continues. “As a result, small and medium factories gain safety with limited space and less fencing.”
“Our smaller robots can operate without a fence and will not move if a person is nearby,” Visti notes. “They are also lightweight and easy to move around, so a manufacturer can use them for one automation task one day and then quickly move the robots to another area the next day.”
Flexibility translates into opening doors for new business.
“We see many three to four employee companies buying robots,” Visti says. “Often these companies have one large customer who occasionally orders and wants a fast response. It can be difficult for an organization of that size to respond and robots offer the opportunity to flexibly run a third shift as needed.”
Using robots also supports growth by opening up opportunities for employees to focus on important areas like service, which retains customers. Robots can take on repetitive tasks like filling boxes or even responsibilities prone to injury and can even help attract employees.
“In Germany, the unemployment rate is down and many smaller and medium-sized manufacturers have a huge problem attracting employees,” Rilke says. “By using robotics for heavy or difficult tasks, companies are able to recruit elderly people to work in the factories.”
Less Expensive, Integrated Initiative
The cost of experiencing these benefits is much more reasonable since robotics manufacturers have become much better at reducing the cost of solutions.
“Prices have come down during the past 10 years,” DeRosett explains. “For example, a fairly basic machine camera that used to cost $5,000 to $10,000 might now be a few hundred dollars. We also use technology like Microsoft Xbox Kinect Sensor to manage costs. All of this puts robotics in reach of small and medium manufacturers.”
“The total cost is much cheaper than companies realize,” Visti states. “New solutions exist that are a great fit for small and medium enterprises, not just for big industries like automotive.”
Whatever the size of the enterprise, robotics play an important role in capturing operational data to contribute to the best practice of uniting information across all systems.
![]() |
“The integrated industry initiative offers tremendous potential for companies to improve quality and operations,” Rilke notes. “By using the same data for creating products through to service and maintenance, manufacturers of all sizes can greatly enhance results. We stress the importance of integrated industry throughout the Deutsche Messe organization, from our work in the Robotics Academy as well as our annual HANNOVER MESSE trade fair and bi-annual Industrial Automation North America, a new U.S. trade show held as part of the International Manufacturing Technology Show. Integrated industry is the theme of this year’s HANNOVER MESSE fair, offering manufacturers the opportunity to stay on the leading edge of this important initiative.”
Resources Available
Through trade fairs like HANNOVER MESSE and Industrial Automation North America as well as the Robotation Academy, small and medium manufacturing enterprises can learn more about integrating robotics.
“We focus on robotics and automation, including security, safety, electronic automation, and other technologies,” Rilke says. “No similar concept exists anywhere in the world. Our conferences and workshops include actual robotics and parts of the production line. We encourage people to test it, program it, and even make mistakes as part of the full learning process.”
The academy serves as host for visitors from around the world and manufacturers attending the industry’s largest manufacturing trade fair, HANNOVER MESSE, often include a visit to the nearby academy.
HANNOVER MESSE and Industrial Automation North America also serve as useful resources.
“At HANNOVER MESSE, you can see the scope of different models and technology that are available as well as network with experts who can help you find the best solution,” Rilke says.
DeRosett notes, “As a smaller show, Industrial Automation North America is easy to digest and great for a basic education. It is particularly useful for a manufacturer who is just getting started with robotics.”
By embracing robotics like the Robinsons in “Lost in Space,” small and medium manufacturers gain business benefits critical to competing in today’s world economy.
“What was impractical a few years ago is now a reality,” DeRosett states. “It is a great time to be in manufacturing.”
To learn more about robotics, the Robotation Academy, and HANNOVER MESSE 2013, watch a video at bit.ly/UZdc55.
For more information about the Robotation Academy, Industrial Automation North America (IANA), and HANNOVER MESSE trade fairs, please contact Larry Turner at Hannover Fairs USA, Princeton, NJ, 609.987.1202; lturner@hfusa.com; or visit http://bit.ly/TTeVJD.
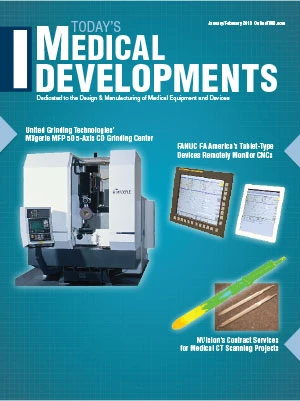
Explore the January February 2013 Issue
Check out more from this issue and find your next story to read.
Latest from Today's Medical Developments
- Tariffs threaten small business growth, increase costs across industries
- Feed your brain on your lunch break at our upcoming Lunch + Learn!
- Robotics action plan for Europe
- Maximize your First Article Inspection efficiency and accuracy
- UPM Additive rebrands to UPM Advanced
- Master Bond’s LED415DC90Med dual-curable adhesive
- Minalex celebrates 60 years of excellence in miniature aluminum extrusions
- Tormach’s Chip Conveyor Kit for the 1500MX CNC Mill