Engineers at FloMet start with the simple premise that it is possible to develop a viable solution and, when combined with their knowledge of metal injection molding (MIM), the goal is easy to obtain.
Located in a 40,000ft2, state-of-the-art building, the company is highly automated, with a dedicated technical staff consisting of true industry experts.
The staff’s ability to create turnkey solutions for client applications enables assistance through all stages of the process – from part design, to blending custom feedstocks, to production, and any secondary operations. The result is customers get a component that precisely meets their specifications, enabling quick production and, typically, in a more cost effectively manner than through other manufacturing methods.
MIM offers numerous benefits compared to conventional techniques like investment casting, die-casting, machining, and press and sinter. The process can produce complex parts in high volume and at a lower cost.
FloMet engineers suggest that clients consider MIM during the initial design stage of a part in order to realize the greatest benefit from the process. In addition, utilization of expertise in the MIM process can help in designing a complex part, perhaps one that is small, with detailed shapes, many intricacies, and one requiring tight tolerances.
The range of metals for the MIM process also go beyond stainless steel, with the production of parts available from FloMet’s custom-compounded exotic alloys, all designed to meet the individual property requirements of the specific application.
Gone Green: In addition to lean manufacturing methods that minimize waste, FloMet uses continuous recycling processes, meaning all products and materials, from design development through final inspection, are recycled in various manners.
Proprietary furnaces feature an ecological scrubber system that internally processes all chemistry, removing any potential for the release of gases into the external environment.
In addition, custom-designed debinder ovens with the addition of a scrubber system are used to collect and retain byproducts for other purposes. Materials taken from these scrubbers (waxes, oils, waste, etc.) are recycled into a component used in paving roads.
Finally, the equipment at FloMet, such as batch furnaces, is energy efficient, while binder ingredients are non-hazardous, meaning feedstock and resulting products are also non-hazardous.
Capabilities
- Metal Injection
- Electromagnetic Shielding
- Thin Wall
- Partnering in MIM Design
- Material & Alloys
Quality in Testing, Measuring, and Inspection
- First Article Layout Inspection
- Statistical Process Control (SPC)
- High Precision Vision Measurement Systems
- ASTM Testing Equipment
- Microstructure Analysis
- Coordinate Measuring Machines (CMM)
- Spectrum Analyzers
- Optical Comparators
Custom Compound Exotic Alloys
- Stainless Steels
- Soft Magnetic Alloys
- Controlled Thermal Expansion Alloys
- Low Alloy Steels
- Implantable Alloys
- Non-Ferrous Metals
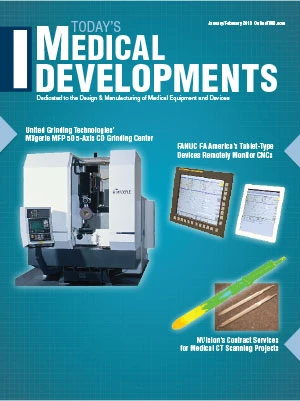
Explore the January February 2013 Issue
Check out more from this issue and find your next story to read.
Latest from Today's Medical Developments
- Tariffs threaten small business growth, increase costs across industries
- Feed your brain on your lunch break at our upcoming Lunch + Learn!
- Robotics action plan for Europe
- Maximize your First Article Inspection efficiency and accuracy
- UPM Additive rebrands to UPM Advanced
- Master Bond’s LED415DC90Med dual-curable adhesive
- Minalex celebrates 60 years of excellence in miniature aluminum extrusions
- Tormach’s Chip Conveyor Kit for the 1500MX CNC Mill