In the case of low-pressure plasma, parts are processed in a closed chamber under partial vacuum. Various process gases can be used. Regardless of the fact that to date no legal requirements exist with regard to particulate and film-like residual contamination on technical medical products – such as implants, instruments, cannulae, and catheters – component cleanliness is becoming a more and more important quality and competitive criterion in the field of medical engineering. Various cleaning technologies are available in order to achieve high levels of cleanliness. Essential factors involved in selecting a suitable process include the material or material combination, type of contamination, component geometry, and production throughput. The technically and economically most effective cleaning solution frequently consists of a combination of various processes.
Ultrasonic Cleaning
The ultrasonic cleaning system with automated workpiece transport is laid out for multi-stage aqueous cleaning processes and subsequent passivation.
Wet chemical ultrasonic cleaning allows for economic, gentle, and ecological removal of particulate and film-like contamination. Even parts with difficult to access hollow spaces, for example blind holes, are quickly and effectively cleaned with this process. The cleaning effect is based on cavitation: When a liquid is subjected to ultrasonic sound, the high intensity of alternating sound pressure during the pulling phase of the oscillation cycle breaks up the liquid – the cohesive forces are overcome. This causes the formation of millions of microscopically small bubbles. During the subsequent pushing phase, these cavitation bubbles are rendered unstable and collapse (implode), and they generate hydraulic impacts with very high energy densities, thus causing micro-currents in the liquid. When these strike a surface, they blast off contamination, which has been partially dissolved by a suitable cleaning agent, and rinse the dirt away.
In addition to the cleaning agent, the frequency of the electrical signals generated by the ultrasonic generator, which is transferred to the liquid bath by the vibration system in the form of sound waves, is also decisive with regard to the cleaning effect. In general, we can say that the lower the frequency of the electrical signals, the more energy is released by the sound waves.
Machined parts are frequently subjected to pre- and intermediate-cleaning with solvents. The state-of-the-art in this area is represented by closed systems with integrated distillation units for continuous reconditioning of the solvent.Ultrasonic cleaning is used in the field of medical engineering for pre, intermediate and final cleaning of, for example, implants and instrument components, cannulae, and other metallic parts. In particular, machined parts are frequently subjected to pre and intermediate cleaning with solvents such as chlorinated hydrocarbons, non-halogenated hydrocarbons, and modified alcohols. The reason for this is the fact that machining media which have been carried over into the solvent, for example cutting oils, can be continuously distilled out, so that the cleaning agent delivers uniformly high cleaning performance over a long period of time. The current state-of-the-art for solvent cleaning involves closed systems. These minimize the emission of volatile organic compounds (VOCs), and comply with current environmental protection and work safety standards.
In order to assure the required levels of biocompatibility for technical medical components, ultrasonic systems with aqueous cleaning agents are used for final cleaning. Rinsing, which is usually a multi-stage process, involves the use of fully deionised water – at least in the final stage. This prevents the adhesion of residues left by the cleaning agent, or surface spots on the parts, which impair quality and biocompatibility.
Various cleaning technologies are available to achieve high levels of cleanliness for medical products such as implants. Integrated Protection
In order to destroy germs more aggressively, in some cases high alkaline cleaning agents are utilized in hospitals to clean surgical instruments after use. Since these media attack the surfaces of the instruments, passivation is becoming increasingly important during the instrument manufacturing process, because the additionally applied passive layer provides improved protection against these chemicals. The passivation process can be easily integrated into the final cleaning system.
Using CO2
Cleaning with carbon dioxide (CO2) is an environmentally sound process. Odorless, colorless, non-flammable, and non-toxic, CO2 occurs as a by-product of chemical and industrial processes, and is reconditioned for use in cleaning applications.
Compressed CO2
Cleaning with compressed carbon dioxide represents a supplement to wet chemical processes, and at the same time meets demands for environmentally sound, dry, residue-free technologies. Compressed carbon dioxide is CO2 that has been liquefied by means of pressure, i.e. carbon dioxide in its supercritical phase, in which it demonstrates very good solvent characteristics for numerous non-polar contaminants such as greases and oils. Supercritical CO2 is distinguished by low viscosity and minimal interfacial surface tension, which results in improved gap penetration. This makes it possible to clean parts with highly complex shapes such as extremely small drill holes and gaps. In the field of medical engineering, this technology offers strong potential for the cleaning of cavities with large aspect ratios such as cannulae, endoscope cavities, and small diameter tubing used as supply lines for oxygen and other gases. This technology is also opening up new possibilities for components with highly porous surfaces, which previously could not be cleaned, or only with disproportionately high costs. A further advantage, which makes CO2 extremely interesting for medical engineering, is the bacteriostatic effect of this cleaning agent.
CO2 reaches its supercritical state at a temperature of 31°C. For liquid parts cleaning, it is used within a temperature range of 15°C to 25°C. Therefore, the cleaning process is well suited for temperature sensitive materials as well. Due to the fact that CO2 is immediately sublimated at atmospheric pressure, the goods to be cleaned are fully dry as soon as cleaning has been completed. This is particularly advantageous for cleaning materials that are highly sensitive to moisture. Thanks to a direct transition to the gaseous phase, no solvent residues or secondary waste are left on the components.
Snow For Clean Surfaces
Liquid carbon dioxide is also used for CO2 snow-jet cleaning – in the form of extremely fine snow crystals. Thanks to a combination of mechanical, thermal, and chemical effects, the non-toxic, non-flammable CO2 snow gently removes film-like and particulate contamination in a residue-free fashion from nearly all materials such as metals, plastics, glass, and ceramic substrates, even if they have finely structured surfaces. Thanks to the readily focusable jet stream, defined functional areas can be treated in a targeted fashion, for example bonding surfaces. Since it is a dry cleaning process, there is no need for energy-intensive drying with CO2 snow-jet cleaning.
In the field of medical engineering, the process is used for, amongst other things, simultaneous cleaning and deburring of cannulae, dental implant sockets, and surgical saws. Burrs with sizes down into the micron range can be reliably removed in this way. On the one hand, deburring action is based on a mechanical effect, which is caused when the snow crystals strike the surface of the respective material. On the other hand, turbulent flow occurs at the surface to be deburred, and the burrs are thus subjected to alternating bending stress causing them to break off.
A Single Step
Plasmas, i.e. gaseous mixtures of atoms, molecules, ions, and free electrons, allow for efficient surface treatment of technical medical products made of various materials such as steel, non-ferrous metals, plastics, glass, and ceramics. Two technologies are available in this respect: In the case of low-pressure plasma, treatment takes place in closed chambers in a partial vacuum. This makes it possible to treat workpieces with complicated shapes as bulk goods or single parts. Various process gases can be used as well. The second alternative involves inline compatible plasma sources, which are operated at atmospheric pressure. These include traditional barrier dischargers, as well as plasma nozzle systems. In these systems, discharge takes place in the plasma nozzle and is directed towards the surface to be treated by means of compressed air.
The surface is simultaneously cleaned and activated during plasma treatment. This double function is based on a physical and chemical reaction within the process: Ions in the plasma are capable of absorbing large amounts of energy, and are therefore able to remove contamination from surfaces like a blasting process in the nanometre range. Reactive species such as oxygen radicals are capable of removing organic contamination like oils and greases by means of cold burning, and entering into a chemical bond with the surface. This results in increased surface tension, which improves results for subsequent bonding, coating, and printing processes.
Biocompatible plasma is used in the field of medical engineering, for example for final cleaning of stents, surgical and dental implants, as well as guide wires prior to coating with hydrogel or PTFE, and for increasing the surface energy of microtiter plates and other diagnostic instruments, silicone breast implants, catheters, and syringes. The surface stickiness and permeation characteristics of contact lenses made of silicon rubber can also be improved by means of plasma treatment.
Amsonic
amsonic.ch
Hoeckh
en.hoeckh.com
Plasma Technology
plasma-technik.de/en.html
Reinhausen Plasma
reinhausen.com
Fraunhofer IPA
ipa.fraunhofer.de
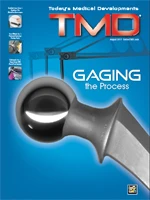
Explore the August 2011 Issue
Check out more from this issue and find your next story to read.
Latest from Today's Medical Developments
- The toolbelt generation
- Covestro's role in transforming cardiac care
- Practical and Affordable Factory Digital Twins for SMEs
- UCIMU: fourth quarter 2024 machine tool orders on the rise
- Thomson Industries’ enhanced configuration capabilities
- Frequently Asked Questions about AM Post Processing
- How new executive orders may affect US FDA medical device operations
- Midwest DISCOVER MORE WITH MAZAK