In the medical device manufacturing industry, accurate measuring of products is critical. That is especially true in the development of orthopedic implant devices, which not only have to meet exacting specifications for a successful surgery, but also must satisfy internal design standards before they ever reach the end customer. A coordinate measuring machine (CMM) is an essential tool that quality inspection at Ortho Development Corporation relies on every day to satisfy their key internal customer first – the product development department.
Ortho Development Corporation, located in Draper, UT, has been focusing on the design, manufacture, and sales of orthopedic implant devices and related surgical instrumentation since 1994. They specialize in products for total hip and total knee joint replacement, and spinal fusion. Their 40,000ft2 facility includes its corporate offices, research and development, manufacturing, inspection, and warehouse space.
Ortho Development’s Escalade Acetabular SystemIn 2004, Ortho launched the first of several new products, all with critical dimensions and performance features. Looking to the future, company management knew they needed more dynamic and efficient inspection measurement equipment to ensure the highest precision while reducing inspection lead times. The quality inspection group needed to start their CMM research quickly.
Tasked with the job of collecting information on different CMM systems, including a Carl Zeiss CMM, was Joe Lucero, QA manager at Ortho. After preparing all of the data reports for management’s review on three comparable machines, from three different manufacturers, it was concluded that a Zeiss Contura CMM was the best system for their needs. Its accuracy and repeatability capabilities were exactly what they needed for their demanding measurement applications. They also liked the technical support options available from Carl Zeiss and the user-friendly Calypso metrology software.
“I have worked with other metrology software programs and I just knew from the initial Calypso software demo that it would be easy to program and that has proven to be true,” Lucero states.
Ortho purchased the Contura 1000 in 2005 along with the Vast XT active scanning sensor. They value the durability of the machine, including the granite table providing a secure surface for their parts, and the ceramic guideway technology that offers stability against temperature changes and moisture. In addition, the complex probe configurations easily changes out for different measurement programs with the MSR probe rack. Ortho was surprised with how accurately the Vast XT sensor continually monitored probe deflection.
“The Zeiss specifications called out deflection to be at 100 millinewtons and it was actually better, at 80 millinewtons, when we measured the probe deflection,” Lucero says.
Prior to the purchase of the Zeiss CMM, Ortho was using handheld and other manual gauges. Depending on the part, their target tolerances range from 0.005" to 0.0002". Previous inspection methods could get close to these targets but they took significantly longer. Efficient measurement on the previous machine was not possible for some of the parts with critical intricate features – such as acetabular shells and liners used in hip replacements, and tibial base trays and inserts used in knee surgeries.
“With the Contura we always had confidence that the target tolerances would be met,” Lucero states.
Inspection of incoming parts from vendors accounts for about 90% of Ortho Development’s CMM inspection work. The other 10% of inspection is on parts they manufacture in-house. Depending on the part type, they measure anywhere from 10 to 100 parts a day on the Contura. This CMM is also used in the design stages of product development and to provide routine gage R&R reports for product management.
Since purchasing the Zeiss CMM, Ortho has experienced a significant reduction in inspection time and had excellent operational success. They are now saving approximately 15 to 30 minutes per lot on inspection time. Ortho also relies on Zeiss Care, which includes an annual software maintenance agreement plus an A2LA accredited calibration service for annual calibrations and maintenance. This package allows them to verify the status of the CMM prior to service and makes sure that it is always running in peak condition. With the excellent care from Ortho and annual calibrations, the Contura has been problem free since 2005.
One Calypso metrology software feature that Ortho particularly likes is Parameter-Coded Measurement (PCM). PCM offers menu-guided control of parameter-supported measuring runs. Programming of measurement plans is in such a way that various workpiece variants can be measured, and parameters can be set to influence the automatic run of a measurement plan. PCM is a powerful tool for using variables in a program. Some variable examples include using feature attributes (size and location), controlling scanning speed, making one program work for an entire part family, and creating user inputs or prompts before or during a program.
“When you are creating a program, you do not have to worry about disrupting the sequence when switching back and forth between different measurements or alignments,” Lucero says.
Contura 1000 with VAST XT active scanning sensor
Due to continual growth and confidence in Zeiss systems, Ortho is planning to purchase a Contura G2 in the near future for their inspection needs. They also plan to add Vast XXT sensor technology with the RDS articulating probe holder for measuring new parts with complex angles. This sensor accepts extensions up to 100mm in length and is well suited for measurements of parts requiring many angular probe positions.
One thing Ortho has learned from the quality inspection process is that the Contura is a critical component in both ensuring their high standards for accuracy and in giving them confidence that they are delivering premium orthopedic implants to their customers. Two principal benefits of owning a Carl Zeiss system are decreased inspection time and user-friendly software.
“Not only has this Contura helped me satisfy my internal customer, our product development department, but I have also enjoyed being associated with Carl Zeiss, their training and support, and I plan to be a return customer,” Lucero concludes.
Carl Zeiss Industrial Metrology LLC
Minneapolis, MN
zeiss.com/metrology
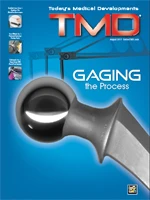
Explore the August 2011 Issue
Check out more from this issue and find your next story to read.
Latest from Today's Medical Developments
- Best of 2024: #5 Article – Accelerating medical device development with freeform injection molding
- Best of 2024: #5 News – Complexity, the enduring enemy of medical cybersecurity
- Best of 2024: #6 Article – Closing the global product information gap
- Best of 2024: #6 News – NUBURU enters medical device market with order Blueacre Technology
- Season's greetings
- Best of 2024: #7 Article – Synchronized machining processes for medtech
- Best of 2024: #7 News – 3D printing could revolutionize treatment for cataracts, other eye conditions
- Best of 2024: #8 Article – Perfecting the CMP process for surgical blades