Photo © Istockphoto.com/Anthia Cumming
Metals have provided the strength, durability, and other characteristics that bone implants require since the inception of orthopedics. The ability of metals to exist in the human body without significant side effects or risk of rejection are via cobalt-chromium super alloys, stainless steels, and titanium alloys – the most commonly used materials in today’s orthopedic devices.
A more recent innovation in metals technology heralds a new era for metals in medical implants: nano-structuring. Scientists from Los Alamos National Laboratory and several institutes in Russia worked together to develop a simple method to modify the internal structure of any metal at the nano-size scale. This is the scale of a cluster of a few hundred, or a few thousand atoms, which is the scale on which many biological processes occur. Modifying metals at this scale allows them to better match and integrate with human bone tissue. Recognizing the potential importance of this discovery, Manhattan Scientifics Inc. has exclusively licensed the patented nano-structuring technology from Los Alamos National Laboratory to make it available for orthopedic implant and other applications.
Understanding this breakthrough is best by comparing the size of the fundamental building blocks of metals with cells, one of the building blocks of the human body. Metals are built with crystals, also known as grains, whose size is typically between 20µm and 80µm, slightly smaller than the diameter of a human hair. Bone cells are smaller than metal grains, generally having dimensions between 4µm and 10µm. Therefore, when bone-forming osteoblast cells attach to the smooth surface of metals, multiple cells bind to a single grain. This is not ideal. Therefore, orthopedic device makers typically modify the metal surface to enhance bone-metal integration. They use chemical etching, bead blasting, or coatings to roughen the metal surface to create smaller scale features that enhance the ability of cells to mechanically-interlock and more firmly attach to the metal. In contrast, nano-structuring changes metals so completely that the fine scale interlocking ability is built in at any surface, as well as throughout the interior volume. The need for additional surface treatment is reduced or eliminated in nano-structured metals. In addition, having the fine scale features throughout the bulk of the metal remarkably improves other metal properties, including strength, cyclic load resistance, corrosion resistance, machinability, and forgability.
Nano-structuring metals also reduce the size of their constituent grains to a range between 0.02µm and 0.40µm. When bone forming osteoblast cells contact a nano-structured metal surface, they cover many grains simultaneously. This offers multiple advantages.
BASIC Dental’s range of
Biotanium implants produced
through a joint venture with
Manhattan Scientifics Inc.First, an intrinsic roughness corresponds to the grain size. The center of each grain can be likened to a hill, while the boundaries between each grain are like valleys. These topographical features enable sub-micron scale mechanical interlocking between the metal and bone cells. In addition, since the planes of atoms within each grain are oriented differently, each cell experiences not one, but many arrangements of atoms. The energy of each arrangement of surface atoms determines the metal surface energy. Nano-structured metals present a range of surface characteristics and energies to each cell. Furthermore, with smaller grains,
there also exists a much larger volume of metal associated with the boundary
regions between the grains. Atoms in or near grain boundaries possess
significantly higher energy than the bulk of atoms within the grains, because nano-structuring creates special grain boundary structures that have particularly high energies. Research is underway at multiple scientific institutions to understand how the energies of nano-structured metal surfaces and grain boundaries enhance cell attachment.
Researchers have published the results of studies in which they evaluated the growth of fibroblast [1,2] pre-osteoblast [3,4,5] and stem cells [6] on nano-structured titanium [7]. They consistently find that enhanced adhesion and proliferation of cells is, in some cases, by as much as a factor of 20.
Another advantage of nano-structuring is that it greatly increases the strength of metals, without altering their chemical composition. Therefore, increase in the strength of pure metals can go to levels comparable to, and even greater than, today’s high strength alloys. For example, the strength of commercially pure titanium (grade 4) can increase from its typical range of 400MPa to 700MPa, to a range between 1,200MPa to 1,400MPa. This increase allows orthopedic devices such as spinal devices or hip stems to be stronger and more compact. The superior properties and processing of nano-structured metals has been reported by researchers worldwide in the more than 6,000 scientific publications, addressing virtually every class of metal.
METAL NANO-STRUCTURING
The nano-structuring technology by Manhattan Scientifics originated with researchers in the former Soviet Union. At the end of the Soviet era, U.S. scientists from Los Alamos National Laboratory joined with scientists from several Russian institutes to transform the original invention into an economical method for metal production. The National Nuclear Security Administration’s Global Initiatives for Proliferation Prevention program provided funding to the Russian institutes while Manhattan Scientifics provided matching contributions to the project. This partnership led to the successful commercialization of the nano-structuring technology. Pilot scale equipment for nano-structuring in Ufa, Russia, is set in a new commercial facility – NanoMeT Ltd. – to produce long rods of titanium and other metals suitable for use in various implants. Meanwhile, Manhattan Scientifics has exclusively sub-licensed the nano-structuring technology patents to a leading U.S. metal manufacturer to implement full-scale production.
DEBUT IN DENTAL
The first application of this new metal in human implants has been in dental implants, using nano-structured, commercial purity titanium rods produced in the pilot scale NanoMeT facility. Medical trials in Europe and North America have shown the advantages of nano-structured commercial purity titanium. Surgical success rates in these studies have been particularly high, between 98% and 100%. Because of the enhanced strength of nano-structured titanium, it has also been possible to design and manufacture smaller diameter implants, which are particularly well suited for replacing lower front teeth. In the medical trials in North America, the time for bone integration and healing shows a reduction by a factor of three, with full tooth restoration and loading within one month.
In the United States, Manhattan Scientifics has established a joint venture with BASIC Dental, Albuquerque, NM, which has obtained FDA approval to manufacture and market a nano-structured titanium variant of the BASIC Dental implant product line. Initial production and distribution of the new Biotanium implants began in December 2010. Registration of the Biotanium implants in other countries is underway so that the benefits of nano-structured titanium and of the BASIC Dental implant system design will become more widely available.
NEXT-GENERATION
The launch of nano-structured metals in dental implants is the starting point for their broader use in a much wider range of prosthetics. The benefits of higher strength and more rapid bio-integration can enhance the performance of virtually any orthopedic device. As full-scale production of nano-structured metals comes online, metal product forms for fabricating hip, spine, and most trauma appliances will be available.
For orthopedic device manufacturers, the benefits of nano-structured metals are not limited to just the superior metal properties. Nano-structuring improves machinability, and provides better surface finish, less tool wear, and higher production rates. Nano-structured metals can also be forged at lower temperatures, which provide a superior die filling ability. The ultrafine grain structure gives nano-structured metals the ability to be formed super-plastically, making it is easy to form them into complex shapes. Finally, in several instances in which medical device manufacturers have wanted to use their special or proprietary coatings, the nano-structured metal surfaces show to be particularly suitable for anodization and application of ceramic films.
The robust availability of nano-structured metals in all the product shapes and forms that prosthetic manufacturers use today will enable a new generation of medical devices to be introduced that are lighter, more compact, stronger, longer lasting, and intrinsically biocompatible.
References
[1] Valiev RZ, Semenova IP, Latysh VV, Rack H, Lowe TC, Petruzelka J, et al. Nanostructured titanium for biomedical applications. Adv Eng Mater 2008;10:B15.
[2] Valiev RZ, Estrin Y, Horita Z, Langdon TG, Zehetbauer MJ, Zhu YT. Producing bulk ultrafine-grained materials by severe plastic deformation. JOM 2006;58:33.
[3] Kim TN, Balakrishnan A, Lee BC, Kim WS, Dvorankova B, Smetana K, et al. In vitro fibroblast response to ultra fine grained titanium produced by a severe plastic deformation process. J Mater Sci Mater Med 2008;19:553.
[4] Estrin Y, Kasper C, Diederichs S, Lapovok R. Accelerated growth of preosteoblastic cells on ultrafine grained titanium. J Biomed Mater Res A 2009;90:1239.
[5] Kim TN, Balakrishnan A, Lee BC, Kim WS, Smetana K, Park JK, et al. In vitro biocompatibility of equal channel angular processed (ECAP) titanium. Biomed Mater 2007;2:S117.
[6] Estrin Y, Ivanova EP Michalska A, Khanh Truong V, Lapovok R, Boyd R, Accelerated stem cell attachment to ultrafine grained titanium, Acta Biomaterialia 7 (2011) 900–906
[7] Semenova IP, Valiev RZ, Yakushina EB, Salimgareeva GH, Lowe TC. Strength and fatigue properties enhancement in ultrafine-grained Ti produced by severe plastic deformation. J Mater Sci 2008;43:7354.
Dr. Terry C. Lowe is Chief Scientist for Manhattan Scientifics, Inc., a publicly held company that advances technologies with potential world-changing impact to the threshold of commercialization via highly skilled scientific and engineering expertise; resourceful, experienced management; and strategic alliances. Manhattan Scientifics is working to bring technology solutions that shape the future into the commercial marketplace today.
Manhattan Scientifics Inc.
Santa Fe, NM
mhtx.com
BASIC Dental
Albuquerque, NM
basicdentalimplants.com
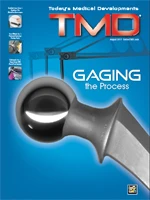
Explore the August 2011 Issue
Check out more from this issue and find your next story to read.
Latest from Today's Medical Developments
- The toolbelt generation
- Covestro's role in transforming cardiac care
- Practical and Affordable Factory Digital Twins for SMEs
- UCIMU: fourth quarter 2024 machine tool orders on the rise
- Thomson Industries’ enhanced configuration capabilities
- Frequently Asked Questions about AM Post Processing
- How new executive orders may affect US FDA medical device operations
- Midwest DISCOVER MORE WITH MAZAK