Anderson Leveille sitting in front of his company,
Moscow Mills Manufacturing Services, in Stowe, VT.Stowe, VT – home to postcard peaks, darling dairies, rural roads, and…Mach 1 machining. The speed-of-sound analogy stems from a comment Moscow Mills Manufacturing Services founder, Anderson Leveille, said recently.
“Going from holding tolerances of thousandths to ten-thousandths of an inch is like going from normal flight to breaking and exceeding the sound barrier. There is a different set of rules that apply,” Leveille says.
Leveille and his crackerjack team of 15, live by the ultra precision rulebook every day they are in the 10,000ft2 (and expanding) shop.
Leveille’s name originates from the French word l’éveillé, which means the awake, the alert. Even so, he says he did not just rise up one day and decide to machine parts for mechanisms like space elevators. Like most progress, it was an evolutionary process. However, he was astute, paying attention to his mechanical talents, which brought several years of what might be construed as unrelated experience to the task – that of sailboat racing.
His boating career culminated with The America’s Cup. He was part of the eight-person shore crew for what is now legendary in the sailing world – the America3 Women’s Cup Challenge in 1995. Leveille kept the Mighty Mary’s engines humming, designed kelp cutters, worked closely with MIT engineers, and learned a great deal about working with and motivating a team of people.
After almost a decade of living around the world, and soon after the groundbreaking Women’s A3 made its mark in sailing history, Leveille came home to Vermont. He travelled from California in a pickup truck, with a Bridgeport and a lathe in its bed, and went to work on his vintage 1820s gristmill and small hydroelectric plant.
He set up a 17ft x 20ft room with his machines and a welder to upgrade the hydro plant. Soon one of his friends from Tubbs Snowshoes asked Leveille to make a few fixtures. One project led to another, and he wound up pioneering a way to bend the snowshoe tubes without scarring the nicely anodized finishes. As word circulated about Moscow Mills, Leveille attracted more prototype parts to the point where he moved into a larger space and bought a knee mill with a 3-axis control on it and his first seat of CAD/CAM software. As the shop’s reputation grew over the next five years, extremely high tolerance, R&D-type parts started coming in from aerospace, robotics, and medical companies. Leveille kept up by hiring bright people and purchasing used CNC bed mills and lathes, which leads to his first rule of precision machining.
The First Rule:
Precision starts from the ground up. “I mean this literally,” Leveille says. “The very foundation of a shop can play a role in hyper precision machining of hyperspace parts. Of course, it has to be perfectly level and vibration dampened. In our new addition, I plan to have a 3ft to 4ft thick floor with vibration isolation sections that the machines will sit on. A thermally stable building is important as well. Maintaining 68°F as closely as possible is very important when you get down in the ten-thousandths tolerance range.”
An Okuma Multus B300
multi-function machineThen there are the machines themselves. Leveille and his staff rebuild older machine tools from scratch, including hand-scraping the saddles and cross slides adding the latest controls, writing new software for the tool changer interfaces, and proprietary custom cycles using UDF and vibration mitigation strategies to not only save money, but make their motion and performance even more accurate than their original specs. The knowledge gleaned in this rebuilding has led the Moscow Mills team to deeply understand machine tools – their limitations and their capabilities. When they buy new, they are persnickety.
“For instance, when we bought our first Okuma 5-axis VMC, I think we put the distributor, The Robert E. Morris Co., through their paces, requesting customization and extra engineering for greater flexibility,” Leveille says.
“They are as customer-focused as we are, and our standards are very high.”
As such, Moscow Mills has continued to purchase Okumas from The Robert E. Morris Co., now owning two MU400VA machining centers and one Multus B300W multi-function machine.
“Thermal control is so important when working with ultra precise tolerances,” Leveille explains, “and the Okumas have a very effective compensation system. They have pioneered a system others are trying to copy with little success.”
Another aspect of precision starting at the ground level is that Leveille and his team believe they are most successful when they are brought in early on a project, at the design phase, to foster a collaborative relationship with the engineer. To that end, Leveille sees his team as interpreters who translate the engineer’s language of computer solid models, blueprints, and materials lists into manufacturing terms.
An interior look at the Multus B300W multi-function machine
“Our customers are some of the brightest people on the planet,” Leveille says. “They are engineers at leading companies and world-renowned universities. We step in when the manufacturability of a part is in question.”
As a case in point, Boston Engineering Corp.’s principal engineer and leader of its Advanced Systems Group, Mike Rufo, had a project to develop a machine used in neurological research. The autonomous unit was designed to cut extremely thin slices of embedded brain tissue that would then be imaged via electron microscopy and used to map neural pathways. The tissue-slicing equipment had to operate within extremely tight tolerances. It was designed to slice a 1mm cube of brain tissue into 50,000, 20nm wide slices (within ±2nm), using a diamond blade only 12 atoms thick at the tip. Orienting the blade in yaw and pitch required construction of a precision positioning device called a goniometer.
“We could design the goniometer to a certain point, but when it got to determining how to hold the part’s tightest tolerances we needed help,” Rufo says.
To machine the components of the goniometer, Boston Engineering contacted Moscow Mills. Describing the stainless-steel assembly the shop produced, Rufo says, “To produce the extreme reliability required in operation, the tolerances for the components ranged from 0.0002" to features that were lapped and hand-fit.”
While the specific analysis and resulting process Moscow Mills employed on the Okuma 5-axis VMC is proprietary. Leveille explains, “We have the best tools in here, however, they are merely tools. There is a multi-faceted approach at work here which involves our culture, our work ethic, the human equation, our ability to repeat a process, that are paramount to success in the precision machining realm. Bottom line, if you do not know what you are doing, you are not going to hit your tolerances. Pre-planning on the ground level is vital. And people are behind it all.” That leads to the second rule.
The Second Rule:
Precision accepts no compromise. “You cannot skimp on anything,” Leveille says, “and I mean anything – equipment, people, training, dedication, ambition, and focus. The work demands it.” One of the parts made on the Multus B300W multi-function machine owned by Moscow Mills.
In addition to advanced metalcutting and grinding machine tools and the relevant software for all disciplines, Moscow Mills also has equipment for fabrication and heat- and cryogenic treatment. A 5-axis coordinate measuring machine and other inspection devices provide the ability to measure the precision parts. Other specialized equipment includes a laser interferometer and Renishaw ballbar for assessing the repeatability of their machine tools.
Moscow Mills has recently found a way to focus its talents and experience through its acquisition of Vibration Solutions. With this acquisition, now Vibration Solutions North – a wholly-owned subsidiary of Moscow Mills Inc., the company is engineering and manufacturing unique tooling solutions for aerospace and other balancing applications. Moscow Mills has applied for multiple patents, which could be helpful for jet engine manufacturers requiring tighter balancing tolerances. These enhanced tolerances have implications for quieter and more fuel efficient power plants. They also result in the need for tooling that has extreme repeatability. Since vibration can result in numerous mechanical issues, the new tooling could be a boon to the industry. As such, Leveille says that top tier companies in the industry are showing interest in the new technology to improve the balancing of critical rotating components and assemblies.
The Third Rule:
Precision requires a willingness to make mistakes, a.k.a. learn. According to Leveille, to get repeatable results below the two-tenths realm, a shop must provide the freedom and encouragement for its employees to remove uncertainty in every place. In other words, a shop needs to build in that breathing room to tinker, to troubleshoot, and to make mistakes or learn as Leveille would prefer it be called.
Moscow Mills continues to purchase Okumas from The Robert E. Morris Co., now owning two MU400VA machining centers.“There are millions of variables when you are working within these types of tolerances and why they may be off,” Leveille says. “Is it the fixture? Burrs? The amount of tension on the bolts? Holding the component or the gauge in your hands too long? Stress in the material? Wrong insert? Improper toolpaths? Every time you remove uncertainty, you end up with fewer variables to examine that may be causing the issue. And, the guys cannot be afraid to try something because this or that might happen, which would make them do something else. It is very easy to get stuck in analysis paralysis. The productive trick with troubleshooting is being able to make a decision, move forward, and if it is wrong, learn from it, and then figure out what to do next.”
Of course, with any business there are time constraints to make profits and on-time deliveries. That is where experience and training comes in, Leveille says. It helps to make 75% or better of the decisions right the first time, otherwise it can be very expensive.
“Sometimes we do not do as well on a job as we would like, but I believe it is absolutely crucial to accept these scenarios and learn from them. The worst thing you can do to someone is chastise them for trying something. The fundamental truth of learning is being willing and able to try something and learn from the results. If it does not go as expected anyone worth his salt is going to analyze the results objectively and be better for it.
Yes, at the end of the race, one can readily see how Leveille’s previous role as a salty sailor was an excellent precursor to running a successful engineering and manufacturing firm. He keeps his tools trim and his team motivated by instilling skills, drive, and determination, and thereby breaks down the barriers to achieve ultra precision.
The Robert E. Morris Co.
Windsor, CT
robertemorris.com
Okuma America
Charlotte, NC
okuma.com/home.html
Moscow Mills Mfg. Services
Stowe, VT
moscow-mills.com
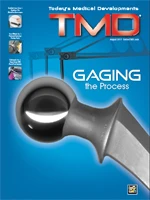
Explore the August 2011 Issue
Check out more from this issue and find your next story to read.
Latest from Today's Medical Developments
- The toolbelt generation
- Covestro's role in transforming cardiac care
- Practical and Affordable Factory Digital Twins for SMEs
- UCIMU: fourth quarter 2024 machine tool orders on the rise
- Thomson Industries’ enhanced configuration capabilities
- Frequently Asked Questions about AM Post Processing
- How new executive orders may affect US FDA medical device operations
- Midwest DISCOVER MORE WITH MAZAK