A recent report by the National Center for the Manufacturing Sciences showed that machining tolerances have decreased by a factor of five within the last decade, and that even tighter tolerances are on the horizon. This means that things like geometry and surface finish are going to play an increasingly important role in machining operations.There are many times when dimensional gaging just does not seem to work, especially when part tolerances get tight.
When tolerances get smaller than 10µm, a completely new world of influences begins to affect the measurement process. What was once an easy measurement may now become much more difficult, with form, surface finish, and temperature taking active roles. Too often, dimensional gage users making precision orthopedic parts may interpret measurement results as gaging errors or end up blaming the wrong source for an error.
Dimensional gaging is critical to assuring the quality of orthopedic parts. Yet the goal of manufacturing is to develop a process in which the requirement for final gaging is minimal, where checking parts simply serves to verify that the process is under control. Getting to that point requires a detailed understanding of not only the machining process, but also how it affects the form and surface of the parts in question. That analysis starts in the metrology lab with different types of gaging altogether.
Two-Point ID
Recently, a major orthopedic customer complained that his air-plug gage was inaccurate. How did he know this? Because, he said, he had checked the measurements against a coordinate measuring machine and a supermicrometer. The CMM and the supermike agreed with one another closely, while measurements on the air gage differed by as much as 2.5µm: therefore, the air gage had to be in error.
The way to resolve these types of problems is to get the whole measurement system together, along with the parts, and start looking at the process – so that is what we did.
We asked for the gage, the master, and a few sample parts to check in our lab, where results are good to sub-microns, dimensionally, and where additionally we run form and surface finish checks on parts to understand what they really look like. Once through this process, we know what size they really are, and whether there is something wrong with the gage or with the measuring process.
The gaging used in this situation was an air plug with two opposed jets to measure inside diameter. Air gaging has many advantages as an inspection method for this type of application. It is quick and easy to use, requiring little skill on the part of the operator. It is highly adaptable to measuring special features for both dimensional and geometric tolerances, ranging from simple IDs and ODs, to taper, flatness, and runout. With different tooling readily installed on the gage display unit, it can be highly economical. In addition, as a non-contact form of measurement (in the sense that there are no hard contacts), air gaging is useful for measuring delicate or flexible surfaces, and for monitoring the stability of continuous processes such as drawing and extruding. Air tooling is a proven, highly precise, and accurate way of measuring bores and tapers often found in orthopedic implants.
As is typical when checking these issues, we start by looking at the tooling and the master. They were both well within their performance specs, so it was on to measuring the parts. Interestingly, depending on how the part was checked, the part looked either good, or bad. Even more interesting, is that when measuring at the same point on the part – identified by a witness mark – the gage repeated perfectly. However, measuring at other locations resulted in a lot of variation in the readings. Some were within diameter spec, and others were not.
The next step was to take a much closer look at the geometry of the parts, and here revealed the problem. In this particular case, all three gages were giving accurate readings, but each was inadvertently measuring different dimensions. In the lab, we found that the parts exhibited geometry errors of as much as 2.0µm, in addition to a small amount of waveform error. By measuring at different locations on the parts, the operator sometimes noticed that variation, and sometimes did not. By simply measuring from a consistent datum, we brought the air gage readings to within 1.0µm of the other two measuring systems.
Figure 2 – The specs called for an average roughness (Ra) of no more than 0.1µm. However, when measured, the parts showed a Ra of between 4µm and 6.5µm. Since the effect of roughness on overall tolerance is a factor of at least eight, and sometimes as much as 20, the 6.5µm of roughness took up the entire 5.0µm tolerance range on the parts – in addition to the dimensional lobing problem.
Instead of asking, “Is it accurate?” the real question here should have been, “Is it appropriate?”
Most gages are accurate as delivered from the manufacturer, but every gage embraces certain limitations and assumptions. When selecting a gage or a gaging method, it is essential to establish clear objectives. Do you want to account for or ignore variation due to geometry, waveform, and surface finish? Do want to know the maximum OD of a part, or the minimum OD, or the average OD?
In today’s world of tight tolerance manufacturing, these errors cannot be ignored. In fact, they should be known before the first part comes off the machine. When qualifying new machines, it should also be common practice to qualify, or characterize, the machining process. Typically, this is done dimensionally, but it is not always taken a step further to understand what form and surface variations the machine is transferring to the parts. Only by understanding these variations will the choice for appropriate gaging fit the required check.
In this case, the form error was eventually traced back to the machine’s spindles, a condition which would have readily come to light during characterization.
Mismatched Pairs
In another case, a doubting customer was making two mating parts, a cylinder and a bore, for a high precision application. The customer complained that while they were machining well within the specified 5.0µm tolerance range on the shaft, the parts were either exhibiting an unexpectedly tight fit, or worse, not fitting in the bores at all. How could they be wrong, he wanted to know, when everything measured right? As in the first case, the user did not realize there are more things that can go wrong with a part than dimension. He had little understanding of how geometry and surface finish were affecting his parts.
The gaging used to measure this OD was a two-point air ring. Just as with the air plug above, the method and precision chosen were right for the application. The air ring provided fast and easy measurement right at the machine making the parts.
The gaging being used in this situation was an air plug with two opposed jets to measure inside diameter. Air gaging has many advantages as an inspection method for this type of application. It is quick and easy to use, requiring little skill on the part of the operator. It is highly adaptable to measuring special features for both dimensional and geometric tolerances, ranging from simple IDs and ODs, to taper, flatness, and runout.However, form analysis showed a consistent three-lobed out-of-round condition on the outside diameters, which was making the effective diameters too large. Three-lobed out-of-round is a very common issue in some manufacturing processes, but unless you look for it, you may not know it is there. In this case, the specs did not call for any geometric analysis on the parts; and the shop was only using a two-point dimensional gage which was incapable of detecting the problem.
Figure 1 illustrates the relationship between out-of-roundness and effective diameter on a three-lobed part. As you can see, any two-point measurement will yield a consistent diameter, because each lobe is geometrically opposed by a flat area. This measured dimension would fall somewhere between the inner and outer dotted circles. However, the effective diameter – or the amount of space this part would actually require to clear – would be the outer dotted circle, which encompasses all the lobes. In this case, because the tolerance was so tight to begin with, the increase in effective diameter caused by the roundness problem exceeded the total tolerance for the part.
Therefore, while this situation appears to be the opposite of the first one, both cases are quite similar. In both, two-point air gaging was used to provide very high precision measurements. However, because the gaging was not appropriate for the application, it could not provide the information the customer needed.
So did that mean that these users had to invest in a lot of expensive lab equipment, or buy new machines? Fortunately the answer is no, not in either of these cases. However, access to sophisticated lab equipment certainly would have helped them understand the nature of their manufacturing processes. In the first scenario, spindle bearings were causing out-of-roundness, and in the second scenario, the odd number of lobes was common for the process (in fact, the greater the number of lobes, the more closely you approach true round). Once understood, compensation for both conditions was easy. The two-point air plugs/rings were exchanged for three-jet versions, with the jets 120° apart. In this configuration the gages could easily pick up the highs and lows on the respective parts.
Measured in the lab, parts exhibited geometry errors of as much as 2.0µm, in addition to a small amount of waveform error. By measuring at different locations on the parts, the operator sometimes picked up on that variation, and sometimes did not.
Best practice dictates thorough checking of machine tools, either on some regular basis – say every two years, or sooner if the environment is subject to heavy vibration or radical swings in temperature, etc. – or whenever a new or substantially different part is to be machined.
Calibration of machine ways, and positioning with products such as laser interferometry, is necessary, and the process itself characterized by appropriate form and surface analysis in a qualified lab. This will not only help avoid unexpected errors, but will also help you understand your overall machining capability. By scheduling the toughest jobs on the best machines, you will improve your total quality as well as reduce scrap and rework.
Surface, Too
Unfortunately, in the second case, out-of-roundness was not the only problem. There was also a problem with surface finish, which while specified, was not really being measured. The specs called for an average roughness (Ra) of no more than 0.1µm. However, when measured, the parts showed a Ra of between 4µm and 6.5µm. Since the effect of roughness on overall tolerance is a factor of at least eight, and sometimes as much as 20 (see Figure 2), the 6.5µm of roughness took up the entire 5.0µm tolerance range on the parts – in addition to the dimensional lobing problem.
Again, the solution was not costly – surface finish gages are readily and economically available for shopfloor use – but simply required an awareness of the problem and an understanding of the basic causes.
Nevertheless, the lesson is an important one. A recent report by the National Center for the Manufacturing Sciences showed that machining tolerances have decreased by a factor of five within the last decade, and that even tighter tolerances are on the horizon. This means that things like geometry and surface finish are going to play an increasingly important role in machining operations. Moreover, we need to understand that role up front, before the first parts are manufactured, rather than trying to figure out the problems later when there is so much more pressure to keep the process running.
Mahr Federal Inc.
Providence, RI
mahr.com
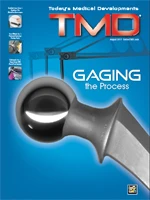
Explore the August 2011 Issue
Check out more from this issue and find your next story to read.
Latest from Today's Medical Developments
- The toolbelt generation
- Covestro's role in transforming cardiac care
- Practical and Affordable Factory Digital Twins for SMEs
- UCIMU: fourth quarter 2024 machine tool orders on the rise
- Thomson Industries’ enhanced configuration capabilities
- Frequently Asked Questions about AM Post Processing
- How new executive orders may affect US FDA medical device operations
- Midwest DISCOVER MORE WITH MAZAK