The intricate, delicate parts of many medical devices present numerous challenges to assembly automation. Complex geometry and tacky surfaces are common among syringes, I.V. components, check valves, sight chambers, and various disposable medical products.
For the precise, yet gentle part handling required to assemble these components, one type of automated assembly system is ideal: high-speed continuous motion machinery. In addition to being able to handle complex components, continuous motion systems deliver the high output and accuracy required.
The results – faster time to market and better quality products. However, what exactly is continuous motion assembly? Perhaps a more in-depth look at this technology will help.
What Is It?
A continuous motion machine is a high-speed automation machine that never loses control with the individual components and is able to perform various tasks, simultaneously. Automation of time sensitive processes can be on one machine, with one part moving continuously through the system from one task to the next.
In terms of high speed assembly, output does not get any faster than with a continuous motion system. But speed is not the only benefit of continuous motion technology.Key attributes include:
- Outputs as high as, or sometimes higher than 1,000ppm (parts per minute), depending on the complexity of the part;
- Positional accuracy as good as or better than other automation systems; and
- Machine footprints up to 10 times smaller than other technologies of similar overall output.
Continuous motion allows for a smooth process that is far less likely to damage any parts, while at the same time maintaining part alignment. Perfect part alignment and no part damage equals mitigated risk for the entire project. Not only is risk minimal in regards to the medical devices being produced, but machine maintenance needs are also reduced, which translates to money saved all around.
Continuous motion systems also allow optimization of the assembly process for maximum speed, efficiency, and accuracy. Multiple, longer processes are automated on one machine, allowing for higher speed. Little or no adjustments are required and the machine’s processes are accurately and consistently repeatable based on the original design.
Applications
As mentioned before, these machines are able to handle challenging parts and materials that are typical of the medical devices industry, such as complex shaped parts or tacky surfaces. Process control functions performed include, heat forming, pressure/flow, torque, ultrasonic welding, laser welding, spin welding, registration, labeling, and marking.
The more complex the assembly, the more likely users may need to use rotary indexing.Here are some of the applications that continuous motion can do better and faster than other machines:
- Irregular shaped parts: Complex curves are best resolved through an orientation process that feeds them into the machine, and looks into a feature on machine tooling. The machines can then mechanically reposition the part.
- Tacky surfaces: Silicone is a typical material in medical devices and can often be difficult to handle. The best way to deal with this is by maintaining tooling centerlines as close as possible. Keeping a consistent speed is of the utmost importance when dealing with tacky surfaces because it will minimize the impact on the part. Constant tooling speeds available on continuous motion minimize the impact of high friction surfaces.
- Fluids applied to a part: It is not uncommon to apply adhesives or solvents that serve as a bonding agent. The best way to achieve this is by dispensing the fluid through individual nozzles on each station, or by transfer from the reservoir to the tooling tip.
- Processes involving heat to modify a part or transfer material: This is an ideal application for a continuous motion machine, since the machine is able to dedicate more time to the operation.
Benefits
The benefits of continuous motion machines are very apparent in the medical devices sector.
For example, the machines can accommodate lengthier tests and inspections. This capability is very important when meeting regulatory, liability, and patient safety concerns. Customization of machines is possible in order to check for height accuracy, missing components, and disfigured parts. Continuous motion can also accommodate manufacturers who perform inspections between changeovers. Inspection controls includes discrete sensors, vision, pressure/flow, weighing/counting, torque and functional testing, among others. As long as identification of parameters is in the early stage, built-in inspection controls can allow for variations in process timeframes. For example, a customer can identify a process that they would like to occur between 2 seconds and 4 seconds. That process can then happen for as short as 2 seconds or as long as 4 seconds.
As discussed earlier, continuous motion machines often come with smaller footprints. To understand why this is, one needs to look at a typical alternative to continuous motion. Many have heard of or used indexing machines before; they are familiar machines that can still make sense in certain applications, e.g. for speeds under 100ppm. Indexing machines differ from continuous motion in that they use a dial to stop and start at each station.
As already shown, continuous motion machines never stop moving and can often offer the same accuracy as slower indexing machines, but at much higher speeds. For example, one continuous motion machine performing multiple processes can have an output of 300ppm, which is the equivalent of five indexing machines each with an output of 60ppm.
Keeping that example in mind, continuous motion requires less labor. Instead of having five different operators on five different machines, you have just one operator on one machine. In addition, as the quest to cut labor costs continues, the advanced controls of continuous motion machines enable a smaller labor force. These control systems include PLC, PAC, and HMI, with a mix of local and remote I/O. The operators need minimum skills to guide the machines in a precise and consistent manner.
This last point shows a glimpse of the future of automated assembly technology. Customers are already requiring advanced data collection and networking, which allows for more accurate trouble shooting and process optimization. In addition, vision systems are becoming more common – especially in the medical devices industry – to identify not only defects and bad parts, but also mold wear and tear that occurs over time.
At Haumiller Engineering, one of the first steps when beginning a project is to decide what parts require the most development. Haummiller engineers are then able to identify risks and manage and prototype those accordingly. This allows for efficiency, simplicity, and lower risk as well. This early collaboration enables quick and efficient assembly of mission critical products, without compromising on quality.
Haumiller Engineering
Elgin, IL
haumiller.com
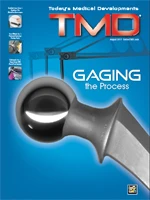
Explore the August 2011 Issue
Check out more from this issue and find your next story to read.
Latest from Today's Medical Developments
- The toolbelt generation
- Covestro's role in transforming cardiac care
- Practical and Affordable Factory Digital Twins for SMEs
- UCIMU: fourth quarter 2024 machine tool orders on the rise
- Thomson Industries’ enhanced configuration capabilities
- Frequently Asked Questions about AM Post Processing
- How new executive orders may affect US FDA medical device operations
- Midwest DISCOVER MORE WITH MAZAK