![]() for receiving an electric motor in medical technology made from Inconel 718 (laser fused part finished using milling and turning technology). |
As a partner to developers and designers, MBFZ toolcraft GmbH, Georgensgmünd, Germany, develops precision parts and high-quality assemblies. Customers come from the medical, automotive, motor sport, and aviation sectors. Their names read like a fine menu – Carl Zeiss AG, Phonak GmbH, MTU Aero Engines, BMW, and Mercedes. With two machines from Concept Laser, Lichtenfels, Germany, for metal laser melting (LaserCUSING), toolcraft is expanding its product range in the areas of turning, milling, die-sinking EDM, and wire EDM to include a generative, powder-metallurgic process.
The novel thing here, according to Christoph Hauck, one of the three managing directors of the company, is the ability to finish components fabricated without the use of a mold with machining and turning where necessary. Fabrication of tool-less components occurs in the space of just a few working days. In addition, production of components from original materials in powder form is with almost identical material properties. This produces completely new solutions, for immediate employment. The finishing touch is by the license to operate as a supplier of precision components in the aviation industry in accordance with EN 9100:2001.
The precision parts produced by the workers in the Middle Franconia region of Germany have ensured that toolcraft has enjoyed an excellent reputation as an ideas generator and driver of new technology for many years. Ultimately, customers get everything they require from one single source: Complete solutions for an assembly as a one-stop shop across the entire process chain – from development right through to delivery of the finished product.
What is important here, according to Hauck, is, “to receive advice and a development service that is independent of any particular material or process. This is the only way that we can find the solution that is the best in functional terms and at the same time is most cost-effective.”
Embracing a wide range of different technologies, this produces parts and complex assemblies in steel, plastic, magnesium, aluminium, titanium, nickel-base alloys, and more recently in monocrystalline superalloys, which up until now were considered incapable of machining.
![]() |
New Horizons
Encouraged by the successful introduction of the new LaserCUSING manufacturing technology from Concept Laser in 2011, and the increasing popularity of the laser fused parts among customers, toolcraft invested in another machine from Concept Laser at the beginning of 2012. Laser melted parts are produced and they are then generally given a machined-cut finish at toolcraft.
“We are currently concentrating here on the core materials that are requested by our customers from the aviation, motor sport, and medical sectors,” Hauck explains.
These core materials currently include aluminium and nickel-base alloys. After each build process, the powder is sieved in an external sieving station from Concept Laser in order to remove any impurities, therefore being able to ensure a consistently high level of component quality.
The major quality feature with the machines from Concept Laser is a closed nitrogen or argon atmosphere. When building up components, entirely using laser melting followed by a cut finish, it is of course also possible to produce functionally integrated components: For instance, Hauck shows off a cooling jacket for an electric motor (see image to right). This extremely compact part made from Inconel 718 has an integrated cooling system with feed and discharge of the cooling medium, which protect the electric motor from overheating. Construction of the cooling system, itself, was in one fabrication step while building up the cooling jacket layer by layer. After the laser melting on the machine from Concept Laser, finishing of the contours are by employing milling and turning processes. This measure ensures meeting of all the tolerances. As a positive side effect of this, at the points, which are milled, the component gets the usual glossy surface, which customers come to expect.
“The generative technology also opens up new development options for us,” Hauck says. “We can now consider entirely new categories. We can change the way we think, departing from a mold-based solution or milling from a complete entity, and instead consider an almost limitless geometry. This offers levels of freedom which a designer must first get to grips with.”
Customers are increasingly excited by the new possibilities that are opening up here on the design side in terms of speed of development, function, or lightweight construction.
Construction 2.0
The possibilities of LaserCUSING allow less warping or cavity formation compared with a die-casting method. This therefore results in a reduction in the scrap rate and, in turn, more quality. In addition, there are cost advantages from not having to use molds, greater freedom of geometry, and markedly shorter production and development times. Hauck from toolcraft estimates the potential for reducing the unit costs to be 20% to 30%. There are also other advantages compared with milled parts: As a fundamental rule, there are material savings, which in some cases can deliver considerable cost benefits. When it comes to producing a geometry in a very confined space, which reflects the current trend, milling or turning is stretched to its limits. For example, the areas where laser melting comes into its own include very complex, thin-walled structures, such as those found in gas turbines or sensors.
“LaserCUSING only uses the material that is actually required to produce the component. This means an enormous material saving,” Hauck explains. “Furthermore, laser melting can be used to manufacture almost all component geometries in just one fabrication step.”
Hauck’s experience with different parts tells him that there is the potential to make a saving of 50% to 85% compared with a milled solution: “Depending on the part geometry, this will have an enormous impact on the unit costs.”
LaserCUSING The Process |
Partnership with Concept
The rapid introduction and successful application in practice resulted from the numerous offers and options that Concept Laser provides to its users. For instance, toolcraft benefits from the knowledge, e.g. hybrid technology and parallel or surface cooling, developed in the Hofmann Group. Another factor is the training courses, offered at customers’ premises, if required, and numerous offers of assistance with the method, application, or materials.
“This,” Hauck says, “is a continuous process of providing support with tricky components.”
After thoroughly researching the offers available in the market, Hauck decided to choose Concept Laser.
“We found that the assurances that were given really were capable of being met and we were not just promised something that could not be delivered. The mutual process of learning between the provider and user operates at a very fair level and in a spirit of partnership at Concept Laser to allow the laser melting technology to develop as dynamically as possible,” Hauck states.
Potential for the Future
The previous possibilities offered by laser melting have already revolutionized the way that toolcraft approaches new projects.
“Just the integration of functions and freedom of design are already providing us today with solutions which previously seemed inconceivable,” Hauck says.
For example, compared with conventional technologies, use of the laser melting method can be to construct a greater surface area, which makes it possible to dissipate heat in a better way. He sees plenty of scope for new ideas in the future: New superalloys are being developed and certified for applications in the high-performance sector. This does of course also apply to high-strength aluminium and other materials, which broaden the scope of possible uses on an original material basis. In the case of the 400W fiber lasers, currently employed, Hauck also sees further opportunities in terms of layer thicknesses and widths to increase the speed of generative build-up.
“What will be particularly relevant in design terms will be to increase the overhangs without any supporting geometries. They are currently around 45°. The objective in the medium term is to advance this freedom to 30°,” Hauck says.
LaserCUSING machines with larger build chambers are also a current development topic for which there are numerous applications.
“All in all, there are very good prospects for remaining competitive in the future,” Hauck says. “There is a further path to travel beyond the horizon.”
MBFZ Toolcraft GmbH
Georgensgmünd, Germany
www.toolcraft.de
Concept Laser GmbH (now owned by GE)
Lichtenfels, Germany
https://www.ge.com/news/reports/tag/concept%20laser
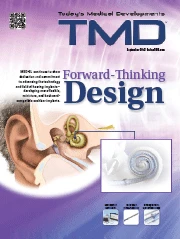
Explore the September 2012 Issue
Check out more from this issue and find your next story to read.
Latest from Today's Medical Developments
- Copper nanoparticles could reduce infection risk of implanted medical device
- Renishaw's TEMPUS technology, RenAM 500 metal AM system
- #52 - Manufacturing Matters - Fall 2024 Aerospace Industry Outlook with Richard Aboulafia
- Tariffs threaten small business growth, increase costs across industries
- Feed your brain on your lunch break at our upcoming Lunch + Learn!
- Robotics action plan for Europe
- Maximize your First Article Inspection efficiency and accuracy
- UPM Additive rebrands to UPM Advanced