![]() |
Rick Cochran is the founder and CEO of Mobile Medical International Co rp. (MMIC), St. Johnsbury, VT. Having won the National Small Business Administration Person of the Year in 2011 has enabled Cochran to be a voice for the success small businesses bring to the United States. As the winner of the SBA award, Cochran even had the chance to meet with President Obama – spending his visit reinforcing the importance of manufacturing and small businesses and their positive impact on the United States.
It is because of this drive and interest in building from that small business vision that enabled Cochran to turn MMIC into a reality.
MMIC offers U.S. healthcare code compliant Mobile Surgery Units (MSUs) and other healthcare delivery facilities. These MSUs are also the basis for MMIC’s ISO-based mobile operating room and patient wards – providing equivalency of care for soldiers serving their countries around the world.
Where it Began
“I once had an employer who used to say, ‘if you hear of a problem more than twice and you find the solution, you have a business,’” Cochran says. “It was in an earlier career, working in medical equipment distribution that I would meet doctors who were eager to have a surgery unit available but knew they didn’t have surgical volume to justify building a facility. Therefore, after a while of hearing this comment repeatedly, I started to put some design drawings and preliminary efforts into the idea of a mobile medical unit.
“As I changed jobs and moved more into the consulting side with physicians for the preliminary design of their facilities for functional layout of all the equipment and various components, the mobile medical concept continued to haunt me. Therefore, after nearly 10 years of knocking this idea around, MMIC became official because I knew if this concept had stayed with me this long, there was a reason why.”
Initially the product range was a tractor-trailer type design where you push a button and it expands from the sides, converting into a medical surgical facility that meets all U.S. standards of care. With that flagship design, Lieutenant General (Dr.) Paul K. Carlton Jr. was the first surgeon to try out the unit. Cochran is quick to note that because Carlton was utilizing this for a surgery, it instantly gave MMIC’s technology some visibility in the military space. That launch pad resulted in the interest of developing a fully integrated, rapidly deployable, self-contained mobile hospital for the military environment.
“Then my approach was to take this concept into a whole new product set, designing and manufacturing for ISO approved military use – where the ISO containers are an 8ft x 8ft x 20ft container where you push a button and it expands – housing everything including a generator,” Cochran states. “From this concept we have also moved into a Mobile Single Pallet Unit (MSPU) that tows behind a Humvee or F-150, which sees utilization in disaster response or as field hospital use as well. The Sultanate of Oman was actually our launch customer for the single pallet units – so a U.S.-based and manufactured product, the MSPUs, has been seeing international use for more than five years.”
Chassis on Up
All manufacturing of the MSUs happens in St. Johnsbury, VT.
“From the chassis on up, we do all of our own manufacturing here in Vermont. A visit to the facility will show work occurring on all the aluminum components that make the box, the manner in which our engineers put together the channels is actually a patented solution, and it is that concept which delivers greater rigidity to our designs,” Cochran notes. “It is a cantilevered-type structure, with telescoping beams on either side. Being a box-in-box design so, from a technical perspective, the unit opens rapidly, featuring a bi-fold floor that is fully connected so it drops into place, enabling users to be up and operational in short time from when you pull up to a location.”
Employees at MMIC also do all the work for the electrical, plumbing, medical gases, ducting, and all mechanical systems the unit requires. Once ready, that all integrates with the componentry – the various medical systems that are installed into the MSUs. Obviously, sourcing of the medical systems is from the industry OEMs, and configure according to the need of the customer. Because of the ability to customize the units based on the end user’s need, the system has a somewhat plug-n-play feature to it, making the options endless and delivering the ability to have the unit, for example, used for ophthalmology one week and then switched over for use in urology or another field of need at that location.
One source of plentiful utilization for MMIC’s MSUs is when hospital officials are looking for a way to maintain services while undergoing renovations. Because the units are state-licensed, Medicare-certified, and joint-commission accredited, as a hospital works on expanding services they can lease an MSU for deployment on the hospital property, maintaining a full range of services until completion of the construction of new, permanent facilities.
Manufacturing, Materials
The staff at MMIC specializes in the design and fabrication of the units, produced heavily from aluminum stock, with forming and fabrication of the components, which will then conjoin through riveting and interlocking channels.
“Internally we partner and share machinery with another company in our facility that builds scales for the weight industry, so we co-share some of the CNC and laser machines with them, enabling the manufacturing of our components to occur right here in our facility,” Cochran says.
There was a time, as the company was just getting started, that component outsourcing was occurring. Then, a few years ago, they started to bring all that work back in-house. However, Cochran was finding that some original engineering designs his staff was using were off specification. Nevertheless, the software they were now utilizing helped solve that.
A staff of eight engineers designs exclusively with Pro-Engineering software from Parametric Technology Corp. (PTC), and have for many years. It was through this use of Pro-Engineering that the design issue was easy to resolve, resulting in an improvement to the componentry manufacturing and more fluid product delivery.
Today
MMIC currently employees approximately 54 full-time employees, and is entering a growth phase, so the addition of more staff is not out of the question. Throughout the years, as orders have ramped up quickly, the use of temporary laborers has occurred, to enable a fast response time, and at points the facility has seen as many as 100 employees on the payroll.
Therefore, when asking Cochran about his ability to find skilled workers, the problem that seems to echo around the industry, he is actually quite positive about it. “As for skilled labor, the regional technical education center is for all of Vermont is located here, so we have been very fortunate at having an easy time filling positions. Because the technical center has preliminary CAD design training, a full electrical shop, and a trade component, we are able to hire employees with a fairly well-rounded set of skills,” Cochran explains. “Beyond that, current employees at our company are very skilled in their craft so they do a good job of taking and training new hires for upward mobility with us.”
Beyond the immediate school in St. Johnsbury, Cochran notes that they also work on engineering recruitment from Thayer Engineering School at Dartmouth College, as well as having recently established a new relationship with Vermont Technical College for entry-level engineering work.
Having a vision for a product, and not giving up on it, as well as having the foresight to work with local educational facilities to gain and retain staff that can help a company grow, Cochran, and the staff at MMIC, appear to be in it for the long haul with their MSUs.
Mobile Medical Int'l Corp.
St. Johnsbury, VT
https://www.mmicmedical.com/
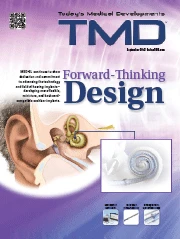
Explore the September 2012 Issue
Check out more from this issue and find your next story to read.
Latest from Today's Medical Developments
- Copper nanoparticles could reduce infection risk of implanted medical device
- Renishaw's TEMPUS technology, RenAM 500 metal AM system
- #52 - Manufacturing Matters - Fall 2024 Aerospace Industry Outlook with Richard Aboulafia
- Tariffs threaten small business growth, increase costs across industries
- Feed your brain on your lunch break at our upcoming Lunch + Learn!
- Robotics action plan for Europe
- Maximize your First Article Inspection efficiency and accuracy
- UPM Additive rebrands to UPM Advanced