Those who have worked in medical device manufacturing for any length of time are aware that precision in production is paramount. In an effort to increase efficiency and product precision, some OEMs might have considered switching to expensive servo or brushless motors over stepping motors. However, designers and manufacturers of stepping motors have made a multitude of enhancements to ensure that their product lines are as efficient and cutting edge as the applications they are used in.
By re-evaluating what manufactures need and expect from their motors, medical manufacturers can reacquaint themselves with the darling of motion control technology – the stepping motor – and learn about the expanded range of features packed into this small, but powerful, motor.
Stepping Motor
Stepping motors have been used in medical applications for decades because of their robust features, performance, and overall value. Innovations to stepping motors are continuously being made. Stronger, rare earth magnets are now being used and are resulting in much greater torque. In fact, the stepping motors of today have approximately 150% greater torque than their similar frame size counterparts did 20 years ago. Additionally, machining processes have greatly improved, allowing much smaller motors to be manufactured.
Coupled with stronger magnets, small stepping motors today can do what much larger motors did years ago. In addition to resulting in greater space saving, the innovations in materials and manufacturing processes also result in motors with a much higher efficiency. Instead of the majority of input power being wasted as heat, high efficiency stepping motors have very little wasted energy, which saves additional money due to decreased energy use and the ability to run at a continuous duty cycle.
The Most from Your Angle
Manufacturers of precision stepping motors offer several different full step angles such as 0.36o, 0.72o, 0.90o, and 1.80o and in sizes ranging from 20mm2 up to 90mm2 with many frame sizes in-between. This full range of stepping angles means that the precision in production OEMs can be achieved with the right stepping motor. Stepping motors have a step accuracy in the +0.033o to 0.050o range. Because of the stepping motor’s quality construction and drive methods, error does not accumulate, meaning that regardless of the move length, error will not be greater than 0.033o to 0.050o.
This works because a smaller step angle results in higher resolution, giving the motor the ability to stop at more points in a given revolution. Rather than using gearing, a motor with a small step angle may be able to accomplish the application. Two methods exist to reduce the step angle. The first is microstepping, which is done electrically by the driver. The second method is accomplished mechanically by increasing the number of phases in the motor and/or the number of teeth. Decreasing the step angle in this manner increases the resolution, decreases the vibration, decreases the error, and costs less since a simple full or half step driver can be used rather than a micro-stepping drive.
The smaller step angles now offered on stepping motors also dispels the old stereotype stepping motors have of being noisy. Because the noise the motor makes is dependent upon the angle used in the motor, a smaller step angle will make the motor vibrate less and cause applications to make less noise.
Stepping Motors In Action
Consider a few medical applications in which a manufacturer’s wide selection of stepping motors made the difference.
An analyzer can have upwards of 50 axes of motion, depending upon the processes. Stepping motors are the obvious choice because of the fact that they can be run open loop. To close the loop on 50 axes would be cost prohibitive. The machine is used in a laboratory environment; therefore low audible noise is required. A stepping motor with a 0.36o step is a perfect solution since lower vibration results in less transferred noise. In addition, the machine must fit within a certain form factor. Since a wide variety of frame sizes are available, small motors can be used on some of the axes, reducing the overall size of the machine. Finally, for reduction of energy consumption, operation cost, a high efficiency motor in some or all of the axes would be a good solution.
High resolution motors with small step angles have become the motor of choice in this application. Furthermore, many pump manufacturers have changed their designs to use fewer consumables, requiring a high torque motor to push less fluid through a smaller diameter tube. Small stepping motors with powerful rare earth magnets are a wise option.
Finally, XY samplers require a high accuracy to ensure the pipette is over the intended well. Stepping motors with high resolution mechanically accomplished by increasing the number of teeth, have the best accuracy of all types of stepping motors.
The Bottom Line
For years, the functions of stepping motor’s have made them the best solution for medical OEMs. Not only are they easy to use, they are cost effective and very accurate. Since designers and manufactures of stepping motors are continuously making improvements, they will ensure that their motors continue to provide the best solutions for medical manufacturers by expanding their range of functions and devising new means to make them stronger, more precise and more energy efficient.
Oriental Motor U.S.A. Torrance, CA www.orientalmotor.com
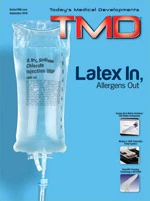
Explore the September 2010 Issue
Check out more from this issue and find your next story to read.
Latest from Today's Medical Developments
- Arterex acquires Phoenix S.r.l., a leading Italian medical device solution provider
- FAULHABER’s expanded portfolio of high-performance DC motors
- NAMSA will acquire WuXi AppTec facilities in Minnesota and Georgia
- Tolomatic’s Drive Integration Tool
- Cutting Edge Innovations: Maximizing Productivity and Best Practices with Superabrasives
- The toolbelt generation
- Covestro's role in transforming cardiac care
- Practical and Affordable Factory Digital Twins for SMEs