This Tsugami SS20 Swiss-type CNC Screw Machine at PMMI has been saving
the company nearly 60% of their outsourcing costs after only six weeks of operation.
When considering the various aspects of the often-used phrase return-on-investment, we frequently think in terms of how much more we can accomplish with the dollars spent. Thoughts also go to how much more we can save with the proper allocation of those dollars. Sometimes, we can accomplish both objectives with the same purchase. Such is the case with Precision Metal Machining Inc. (PMMI), a surgical instruments and implants contract manufacturer in Carlstadt, NJ, specializing in servicing customers in the orthopedic industry.
Founded 24 years ago as a general commercial-based machine shop with five employees and a handful of conventional machine tools, they grew steadily to where they now employ 40 people and feed a work-hungry lineup of CNC lathes, machining centers, and EDM machines. Of equal importance, their relationship with Morris Group divisions, Morris TriState and Rem Sales, extends back nearly as far, with the distributor providing valuable applications assistance and training, along with state-of-the-art machine tools that include Okuma and Tsugami lathes and machining centers.
“The move to Okuma was a natural,” says PMMI’s Director of Sales, Steve Barrows. “Since our main customer at the time had Okuma equipment, we could replicate their production techniques with the same machine tools. The CNC programs were already established for the Okuma machines, so we could just install the equipment, load the programs, and start cutting. The staff at Rem Sales was with us all the way and worked hard to get our people up to speed very quickly. Frequently, when you get new equipment on the floor, there’s a lot of downtime for training and familiarization. Often, you also encounter speed bumps in production while you are optimizing tooling and fine tuning the programs. This did not happen, thanks to Rem’s dedication to after-sales support.”
Complementing many of today’s advanced surgical techniques, orthopedics has moved into the realm of minimally invasive technology. Instrumentation for many of these new surgeries calls for parts that are longer and thinner than those of previous designs.
“While the bulk of our precision machining operations are still handled easily on our Okuma lathes and machining centers,” Barrows says, “it was not long before we were spending upwards of a quarter-million dollars a year for outsourced screw machining operations. We turned again to the capabilities experts at Rem Sales. They helped us explore the options to bring the screw machining discipline in-house.”
“After significant machine versus machine comparisons,” says Giovanni Riccardi, PMMI’s director of operations, “we selected the Tsugami SS20 Swiss-type CNC automatic as the optimal solution for our requirements. Some of the machines we looked at had the strength for heavy cuts, but did not have the rigidity needed to hold fine micro finishes. We can not allow chatter and tool marks that require a great deal of hand finishing. Demos on the Tsugami SS20 showed us it could take the time-saving heavy cuts and still provide the smooth finishes our customers need right off the bat. It has all of the bells and whistles we could ever need for our parts.”
The bells and whistles Riccardi alludes to are certainly obvious in a brief rundown of the machine’s specs. With a 0.787" (20mm) bar capacity and 8.67" (220mm) workpiece length, the Tsugami SS20 is based on a much heavier 32mm machine’s construction, giving it a rigidity and vibration damping heft of over 7,400 lb that is so critical to achieving the demanding tolerances of orthopedic instruments. The SS20 provides seven controllable axes, the capacity for 24 tools and features live face and cross tools for the main and sub-spindles. Rapid traverse is a fast 1,260ipm (32mpm), the main spindle speed is 10,000rpm and tool spindle speed is 5,000rpm. The SS Abile CAD/CAM software uses a simple building block concept for part design and is standard with the machine. Also standard is a dual path Fanuc 31i-A CNC system that greatly reduces cycle time by permitting true simultaneous operation of the main and sub-spindles.
As soon as the new machine was delivered, the engineers from Rem Sales helped get a couple of the first jobs started, so the SS20 has been productive since it arrived. “As an example of the machine’s ease of operation,” Barrows explains, “we assigned our EDM lead man, who had no previous experience on a CNC lathe or mill, to start on the new Tsugami under the tutelage of the Rem Sales people. I am happy to report that with a minimal learning curve, he quickly established a comfort zone with the machine and its control.”
Of key importance to PMMI is the ability of the new Tsugami to easily handle extremely tough 455 stainless steel. They encountered problems outsourcing some of their screw machine work to several vendors, who would not even quote the job if it called for 455 stainless. With the SS20, PMMI can machine 455 stainless as easily as 300 series or 17-4 stainless, which they consider to be the vanilla of the industry.
One example of the work coming off the Tsugami is a handle for an orthopedic curette (a bone scraper). Previously, it would have to be outsourced or produced in-house, requiring a CNC lathe and a machining center for two turning and two milling operations. The SS20 allows them to drop this part complete, in one shot, with a cycle time of ten minutes. The finished size of this handle is 1.75" long and 0.669" diameter and is held to 0.0004" tolerance on the back end where an interchangeable component is threaded and then welded. It is later subjected to an over-mold process and the tight tolerances prevent silicon rubber leakage or flashing.
Another application is one of a family of ten fittings used for spinal surgery applications. The largest is 10.50" long. Starting from a 0.75" diameter, it is brought down to 0.275" in one shot. According to PMMI, it requires the combined rigidity and horsepower of the SS20 to remove that depth of stainless material and still maintain a 32rms surface finish.
“We could not get our outside vendor to even bid on the project,” Riccardi says. “They did not have the capability on their equipment to machine the diameter between the fitting’s two wings. The Tsugami has the capability, thanks to its 90° milling attachment, that eliminates a 10 minute secondary operation.” The machine also achieves a 0.001" geometric tolerance between the first groove and the groove behind the wings that is quality checked under 50x magnification.
“Three important factors in the success of our business are part quality, prompt delivery, and cost competitiveness,” Barrows says. “The Tsugami gives us confidence in the quality of the parts it is producing. Every part is subjected to strict verification in our quality department. After all, once it is inside a human body, it has to work absolutely perfectly.
Summing up PMMI’s return-on-their-investment: in just the first six weeks with the new Tsugami SS-20, PMMI has realized a cost saving of 60%. New parts are being programmed for the machine’s CNC system and process validation is ongoing. Eliminating outside vendors for screw machine operations on their precision components has given PMMI total in-house control of both productivity and quality.
REM Sales, Windsor, CT www.remsales.com
Precision Metal Machining Inc., Carlstadt, NJ www.gopmmi.com
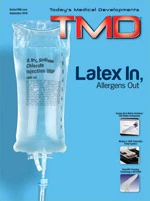
Explore the September 2010 Issue
Check out more from this issue and find your next story to read.
Latest from Today's Medical Developments
- Arterex acquires Phoenix S.r.l., a leading Italian medical device solution provider
- FAULHABER’s expanded portfolio of high-performance DC motors
- NAMSA will acquire WuXi AppTec facilities in Minnesota and Georgia
- Tolomatic’s Drive Integration Tool
- Cutting Edge Innovations: Maximizing Productivity and Best Practices with Superabrasives
- The toolbelt generation
- Covestro's role in transforming cardiac care
- Practical and Affordable Factory Digital Twins for SMEs