Implant Direct LLC, designs and manufactures application-specific dental implants and prosthetics sold directly to qualified dentists. The company is the brainchild of implant pioneer Dr. Gerald Niznick, who invested two years with his team of engineers and manufacturing specialists to develop a technologically advanced line of implant products and a unique facility in which to produce them.
According to Joe Morales, director of manufacturing for Implant Direct’s Calabasas, CA., manufacturing facility, “Dr. Niznick gave us free reign to develop the most efficient manufacturing plant possible. I know the term state-of-the-art is over used, but it really applies to the way we put together this facility. We are so proud of it we even have live webcams on our website where you can see what we’re doing.”
Implant Direct uses 40 high-precision Swiss machines, coupled with 40 LNS Express 320 automatic bar feeders that load 12ft lengths of titanium bar stock. The plant runs three shifts to produce over 600,000 dental implants each year and several million related parts. On weekends, a skeleton crew works until noon Saturday and the factory continues operating unattended until 7am Monday morning.
“Thanks to our high-efficiency Swiss machines and the ability of the Express barfeeds to run continuously, we have reduced labor costs dramatically.” Morales explains. “We have 20 employees working the first shift. They set up the jobs and get production going. The second shift drops to nine workers who are extended from the first shift. The third shift has zero workers. We run unattended overnight and on the weekends, using remote monitoring of machine functions and other factors, including vibration sensing, to make sure the process runs smoothly. We can do this because we have designed the entire operation for maximum efficiency. We use the most reliable equipment we could find, including the LNS bar feeders, our Swiss machines and Kennametal Quick-Change cutting tools. When our employees start the day we have all of the production programming and kits of tools ready.”
The Express automatic bar feeders saved Implant Direct 30% in labor costs versus the manual loaders used in their previous factory, which had fewer machines with 75 people running them. Today there are more machines and the entire machining operation runs over three shifts with 40 people. Another advantage of the automatic bar feeders is less handling of bar stock. For example, when machine titanium bar stock as small as 1/8", with the manual bar feeders the stock sat on hooks where it sometimes became bowed and could cause machining problems. Now that it is loaded directly into the LNS automatic barfeeder, that is never an issue.
“When we designed the new factory we evaluated a number of barfeed suppliers. We chose LNS not only for the quality and reliability of their barfeeders, but because of their attention to service. We want our key suppliers to work with us as partners, we have had that relationship with LNS,” Morales concludes.
LNS America, Cincinnati, OH www.lns-america.com
Implant Direct LLC, Calabasas, CA www.implantdirect.com
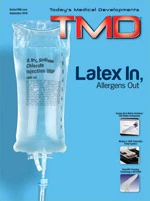
Explore the September 2010 Issue
Check out more from this issue and find your next story to read.
Latest from Today's Medical Developments
- Arterex acquires Phoenix S.r.l., a leading Italian medical device solution provider
- FAULHABER’s expanded portfolio of high-performance DC motors
- NAMSA will acquire WuXi AppTec facilities in Minnesota and Georgia
- Tolomatic’s Drive Integration Tool
- Cutting Edge Innovations: Maximizing Productivity and Best Practices with Superabrasives
- The toolbelt generation
- Covestro's role in transforming cardiac care
- Practical and Affordable Factory Digital Twins for SMEs