Despite a global recession, medical device manufacturers are facing unprecedented opportunities for growth. High consumer expectations for better healthcare and technology advances that improve quality of life are creating favorable market conditions. Yet, rising costs and compliance concerns are forcing medical device companies to proceed with caution – balancing the competitive drive for product innovation and quality while reassuring consumers that what they buy is safe and fairly priced.
To help manage this opportunity, some of the most successful medical device companies are supporting the FDA’s Total Product Lifecycle (TPLC) methodology – outlined in more detail below – with technologies such as Product Lifecycle Management (PLM). TPLC, implemented with a comprehensive PLM suite, enables medical device manufacturers to deliver innovative, compliant-ready products that meet revenue targets and are consumer price-friendly.
Regulatory compliance is at the forefront of every product development process, especially as companies rely on international suppliers and manufacturing facilities. In successful companies, compliance is the outcome of an effective, proactive business strategy that uses an open, collaborative, end-to-end PLM system for providing complete product lifecycle traceability while facilitating efficiency and productivity. With PLM enabling better compliance, these companies can achieve strategic, competitive growth initiatives such as increased quality, more innovative products, and faster time-to-market.
In 1997 the FDA mentioned the waterfall design process, a product development process that uses logical and sequential steps to produce design controls as an example. Although the FDA did not mean to be prescriptive, life sciences companies have been using it ever since.Iterative vs. Sequential
Historically, methodologies promoted by the FDA have a tremendous influence on how the medical device industry develops products. As seen below, the FDA mentioned the waterfall design process in 1997– a product development process that uses logical and sequential steps to produce design controls. While they intended it as an easy example, and not as a recommended approach, most of the industry took it as a signal and adopted a similar sequential approach.
The waterfall model is beneficial when introducing design controls but has limitations when developing more complex devices – concurrent engineering models have been more successful in that area.
Research analyst firm Cambashi, in conjunction with Life sciences advisory firm Axendia, evaluated the state of the medical device market in terms of the TPLC transformation process. The study, Total Product Lifecycle Management: Lowering Costs while Increasing Quality, identifies some of the key results experienced by early adopters of TPLC approaches. The researchers used a combination of online questionnaires and telephone interviews, garnering responses from 212 individuals (80% managers, directors, and executives), representing more than 185 companies worldwide.
According to this study, 60% of respondents primarily use either a stage gate or waterfall design process while 35% use a concurrent, agile, or other approach that is more consistent with the intent of TPLC. Our research also revealed that nearly half of the survey respondents indicated TPLC was a priority. This is no surprise since one of the benefits of TPLC is the ability to stimulate new product introduction, which was rated the number one opportunity by study respondents.
However, many companies have yet to deploy TPLC despite the tremendous business benefits in doing so. Some of the roadblocks to TPLC implementation include many of the same challenges faced by the industry as a whole – design changes that delay production while also impacting quality and compliance; communication and process challenges along an extended supply chain; and reactions to audit findings.
As seen in the TPLC model, an iterative methodology such as TPLC has the potential of dissolving these roadblocks because it promotes a collaborative environment along the entire product lifecycle. TPLC users validate each component and process design prior to production and design release.
The crux of a successful TPLC implementation is access to shared data across the product lifecycle and, by doing so with PLM, TPLC can also reduce process complexity, save time, and effectively utilize resources across the enterprise and throughout the supply chain.
The TPLC model interconnects and maintains pathways to every component necessary to design, build, and maintain a product. Source FDA CDRHSuccessful TPLC
Medical device manufacturers that want TPLC benefits will need to make a cultural shift, from a sequential and manual process mindset to one that incorporates concurrent and automated processes. PLM applications fulfill the promise of TPLC by helping users design market favorable products; reduce recalls; and effectively manage audt request in real-time. Benefits of integrating PLM into a company’s overall TPLC strategy are immense and include the following areas.
Collaborative Innovation Engine: With PLM, IT-enabled global teams use a common software environment to easily access relevant data, tools, and processes and automate regulatory and quality business processes (workflows) over a unifying foundation built on a single platform. This common platform gives all stakeholders visibility into the massive amounts of information necessary to manage the product lifecycle – eliminating communication bottlenecks. Users no longer need to rely on paper-based processes and/or home-grown point solutions that fail to rapidly and accurately communicate cross-functionally.
Provide an End-to-End Product Development Process: PLM supports the end-to-end product development process – from design creation to product analysis; simulation to manufacturing assembly; maintenance planning to operating training; and patient interaction modeling. PLM fills in the product related gaps that other major enterprise applications such as Enterprise Resource Planning (ERP) are not designed to address. The most comprehensive PLM solutions should also be able to easily integrate with the enterprise applications like ERP or CRM.
Leverage Quality Information and Improve Overall Product Performance: By managing quality issues throughout the product development process, medical device manufacturers can track, investigate, and dispose of field complaints, product inquires, and service requests. They can also be proactive about potential issues. By offering a single, global, on-line system with direct access to the product design and R&D process, PLM provides medical device manufacturers with greater transparency into their quality issues such as CAPAs, nonconformance reports (NCRs), product complaints, and quality audits, and facilitate appropriate engineering changes. As a result, companies can more effectively manage compliance risk, reduce waste, and leverage quality-related information for improving overall product performance.
Real-Time Visibility: PLM supports root cause investigation by linking the information directly to the CAPA. Organizations can respond quicker to market opportunities by streamlining product design, submissions, and the production ramp-up – all because PLM enables real-time visibility into initial request, root cause analysis, risk assessment, and closure.
Closed Loop System for CAPAs: Complying with Good Manufacturing Practice (GMP) regulations becomes easier when companies implement a PLM approach that enables a global, integrated closed loop system for CAPAs. With the tracking of production and non-production issues, audit management and quality monitoring improves. This helps the manufacturer shift from reactive to preventive one.
Eliminates Organizational Silos: By centralizing product development and quality system processes in a common environment, PLM eliminates organizational silos that foster erroneous information. Organizational silos prevent collaborative communication, leading to poor quality, more recalls, and slower time to market. Instead PLM enables global collaboration for better decision-making.
Reduces Auditing Complexity: PLM automates processes to maintain accurate record keeping, track auditor requests, and ensure responses are provided. The responses, such as a manufacturing procedure, are linked automatically to the relevant data in the PLM system. Users can develop an audit schedule to track and plan internal, supplier, and external audits.
In a comparison between medical device manufacturers that use PLM to implement TPLC and those who do not, the Axendia & Cambashi study reported that the PLM users group was much more able to improve along cost and quality lines.
Conclusion
The benefits of TPLC go far beyond time and cost savings, or visibility and collaboration. Fully implemented, TPLC also shortens innovation cycles and results in higher quality products for consumers. TPLC combined with PLM further increases success. Through the use of a common, collaborative innovation engine, all company stakeholders leverage quality information to improve overall product performance. By providing direct access to the product data, regulatory and quality professionals within the organization have real-time visibility into the product development process, and engineers have insight into the regulatory and quality process. This fully transparent, closed-loop system allows innovation and collaboration to flourish, putting more life-saving products in the hands of patients.
Dassault Systèmes Enovia Corp
Lowell, MA
3ds.com
Cambashi Inc.
Cummaquid, MA
cambashi.com
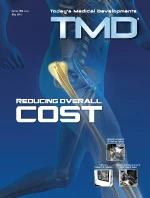
Explore the May 2010 Issue
Check out more from this issue and find your next story to read.
Latest from Today's Medical Developments
- German robotics and automation in a downturn
- Blueshift’s AeroZero
- November USMTO grow from October
- Platinum Tooling’s custom and special tooling
- Top 5 global robotics trends 2025
- Accumold’s micro molding innovations
- Methods Machine Tools, Multiaxis, announce AI solution investment
- MGS to showcase global expansion and healthcare CDMO expertise