Recigno Laboratories receives close to 400 orders a day for the crowns and bridges they produce.Recigno Laboratories has more than a half century of experience in the production of dental prostheses. Established in 1954 by Peter Recigno – who is still active in the company – son David Recigno now leads the family business and its staff of about 100 employees.
As one of the largest producers of crowns and bridges in the United States, the company supplies approximately 8,000 customers – both dentists and small dental laboratories –from the company’s locations in Willow Grove, PA, and Pleasantville, NJ. Together, the two locations receive close to 400 orders a day. For more than 10 years, the company, considered the technological leader in the field of industrial production of dental prosthetics, has used CAD/CAM processes in order to achieve high production volumes and optimum quality. Being in the business of producing dental prostheses for many years, Recigno Laboratories employees were already familiar with the CAD/CAM technologies of closed systems, but the recent decision to purchase the DMG Ultrasonic 20 linear as a milling machine was definitely a new direction. In addition to choosing to use an open system for the first time, Recigno Laboratories also added biocrown, biobridge, biocoping, bioframe, and the entire biorestoration line – a product it developed in-house – to its range.
So why implement all the change?
Having read about the Ultrasonic 20 in an issue of the DMG Journal, David Recigno was sure that machine would fit perfectly in their laboratory, meshing with the daily production routine.
As Recigno explains, “We were looking for a machine that could also machine glass-ceramics and zirconium efficiently. The Ultrasonic technology struck us as highly advanced and exceptionally well suited [to our process], and it is a critical step to eliminate any chance of micro-fractures happening to the material being milled.”
Recigno’s next step was contacting his local DMG supplier, Sauer, which is where he obtained all the technical information he felt he needed. “That,” he says, “is what completely convinced me. Basically, it was the Ultrasonic machining and the high precision, compared to the turnkey lab CAD/CAM systems currently on the market that was the key justification for purchasing the machine.”
Citing the various technologies of the machine, Recigno, after having researched other machines, felt there were none as well equipped with the technology and that also works as efficiently.
“This is precisely what makes it different from other machines. The fast linear drives are a huge advantage for us, as they make the production highly dynamic. The 5-axis simultaneous machining also produces a better end result,” Recigno explains. “Since it can machine even extreme undercuts, it actually permits us to produce all designs on the machine. Now we have a versatile machine that also ensures rapid and highly precise operation, which increases our production volume and improves the quality of the crowns and bridges.”
David Recigno, CEO of Recigno Laboratories, in front of the Ultrasonic 20 machineProduction Growth
In regards to the increase in production volume, since the machine is equipped with the integrated linear magazine, workers are now in the position to run the machine, unattended, while preparing new copings, frames, and crowns. This, in turn, enables the company to accept significantly more orders than before. Yet another benefit Recigno is seeing is the elimination of any human error in the handling of the zirconia, alumina, and lithium disilicate blocks, enabling a better quality-controlled production environment that further adds to the growth aspect.
The use of the Ultrasonic 20 is a driving force in the growth of the company, but Recigno considers this additional piece of equipment only an extension of the closed system they have always implemented – with no current plans to combine the two processes.
“With biocrown and the biorestoration product line we have developed a product line that we produce exclusively on the Ultrasonic machine. It essentially competes with our previous products, but we want to offer a broader product range,” Recigno states. “You might compare it with the selection of a pain reliever. The doctor can recommend a generic active ingredient that represents a solution for the patient, but some still insist on the brand name because they want the best. With our crowns, the situation is similar: Even though many companies can machine zirconia, alumina, and lithium disilicate, our labs and dentists are getting a brand name product that they can trust because of the advanced technology we employ, including the Ultrasonic 20 milling system. They get their own impression of the quality and characteristics of our products and advise their patients accordingly.”
Moving Forward
Since most customers send in handmade models, these models require scanning into the system in the laboratory prior to milling on the machine, and for this Recigno employees utilize scanners from 3Shape. While some customers currently send in an STL dataset, ready for employees to process, there is always the hope for more customers to convert to scanners. A trend that they are noticing is that toward intra-oral scanners. After the patient’s mouth is scanned and that file is sent to the lab, technicians use CAD software from 3Shape to produce the crowns and bridges. Following that, a milling strategy is defined with CAM software from Open Mind.
When asked about future investments, Recigno notes that the Ultrasonic 10 is another option for them. “We now know what the Ultrasonic technology can do and believe that a more compact and less expensive machine, with these same characteristics, can provide ideal support for our production.”
Until the time of the purchase of the next machine, Recigno says that they “will continue to drive ahead with the growth...and with the expansion of our production capacities. In so doing, we will continue to value innovation and apply advanced technologies so we can also satisfy the quality demands of our customers and their patients in the future. Because one thing is certain: the dental industry will grow and that means not only an increased demand for crowns and bridges, but also better and more advanced products for our customers.”
DMG / Mori Seiki U.S.A.
Hoffman Estates, IL
http://us.dmgmori.com/
Recigno Laboratories
Willow Grove, PA
recigno.com
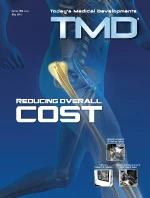
Explore the May 2010 Issue
Check out more from this issue and find your next story to read.
Latest from Today's Medical Developments
- German robotics and automation in a downturn
- Blueshift’s AeroZero
- November USMTO grow from October
- Platinum Tooling’s custom and special tooling
- Top 5 global robotics trends 2025
- Accumold’s micro molding innovations
- Methods Machine Tools, Multiaxis, announce AI solution investment
- MGS to showcase global expansion and healthcare CDMO expertise