Of the linear motion technologies available today, one relative newcomer is the integrated stepper motor linear actuator.When referring to linear bearings, we generally think of devices that incorporate ball bearings – meaning friction is reduced between moving parts by recirculating (usually metal) balls. Bushings, ball splines, linear guides, and slides typically incorporate recirculating ball bearings.
Increasingly, as technology becomes more demanding, requiring greater and greater precision, another type of bearing has established its place in the pantheon of friction reducing devices – the crossed roller bearing. What high-tech microscopes, as well as advances in wafer manufacturing, robotics, and vision inspection have in common is their growing reliance on crossed roller bearings.
Crossed roller bearings work like ball bearing slides, except that the bearings housed within the carriage are cylinder-shaped instead of ball shaped. The rollers crisscross each other at a 90° angle and move between the two parallel guides that surround the rollers. The rollers are between V grooved bearing ways or raceways ground out of the guides. The travel of the moving guide/table ends when it meets an end cap, a limiting component.
Loads and Cages
Roller-to-rail contact is key in determining load capacity. Of course, rollers provide a larger contact area than ball bearings and, since the rollers usually do not recirculate, they are all carrying the load which produces greater rigidity as well as higher load capacity than ball bearings. Balls, typically contacting at a single point though a raceway’s surfaces, can be designed as curves to increase the points of contact.
There is a direct correlation between the contact area of the crossed rollers and load capacity. The amount of space between the rollers is a major factor. Load capacity can actually be increased as much as 250% by designs with greater roller-to-rail contact.
Metal and resin cages hold the rollers in completely different ways. Metal cages hold the rollers via a notch on the top and on the bottom of the rollers. However, the resin retainer fits around the roller. The resin retainer is able to harvest the whole shape to be held. The whole shape can be in contact with the load because the resin retainer exposes the necessary contact areas.
Rollers in a resin cage can be closer together. This increases the number of allowable rollers within the cage length. So either the cage can be shortened or the load capacity can be increased. A resin cage can afford at least a 30% to 58% increase of the contact area as compared to a metal cage.
Metal cages are less expensive and can be either all stainless or steel. Therefore they can be used in high temperature or medical applications where there is a lot of water and rust potential. Metal is also better suited in a vacuum since resin can have out-gas; such gas emission can cause problems, especially in high vacuum environments.
Travel Length
The longer the travel, the longer the rail has to be. However, as opposed to recirculating ball bushings – which have to have a shaft only as long as the travel required, since the only moving component is the bushing – with crossed roller bearings, the whole rail assembly has to be twice as long as the stroke. That is because both rails containing crossed roller bearings move in opposite directions. So the whole assembly has to move within a space that is twice as long as the travel length. Exceptions are in the minority of cases in which crossed roller linear guide products have recirculating crossed rollers or roller guide products that are not crisscrossed – having four circulations with opposite roller orientations. These exception products do not need rails moving in opposite directions.
Travel Limits
The length of travel is limited by the space available for the rails within an application. Since the rails move in opposition to each other, the space required is twice the distance that the load will be carried. Additionally, an endstop limits travel length. They can only extend (in opposite directions) until they hit the endstop. This makes crossed roller bearings unsuitable for applications that require long strokes.
Wear
For motion control applications with extremely fast acceleration and deceleration – at dimensions ranging from 30mm to 600mm lengths, 2mm to 12mm rollers – endurance can be 150 million cycles.
In crossed roller bearings without anti-cage creep mechanisms, cage creep may necessitate the replacement of guides and readjustment of the machine or installation. This affect often occurs as a result of high acceleration and uneven preloading or load distribution, as well as orientation – inclined or vertical orientation can easily cause creep.
Fit/Interchangeability
The cage in any bearing prevents ball to ball or roller to roller contact, which can cause more friction and wear. Whether the cage holding crossed roller bearings are metal, resin, or some other material, it alters, somewhat, a crossed roller bearing’s dimensions. This affects how they fit into a product design. Stoppers can also affect their size, and therefore their fit.
In addition to stoppers, cage material and design, another factor that affects interchangeability is the design of the anti-creep mechanism.
Cage Creep
In non-recirculating linear components, the retainer floats between the rails and can drift (or creep) from center position. Cage creep is damaging because every time it creeps, rolling elements are not rolling, instead they are slipping and causing metal to metal wear. As the roller cage creeps away from center, it will begin to restrict the slide’s travel. It will creep over time if a full stroke is not being used; especially when mounted vertically. If, after the retainer drifts, the full stroke is once again used, the retainer will hit the endstop of the rail and be forced to skid in order to center again. This action requires a strong motor and can damage the retainer, the rollers, and the slideway. With higher preload, it is even more difficult and damaging to skid the cage back in place.
Anti-Cage Creep
The term anti-creep is used to describe the method of eliminating any slippage of the retainer holding the crossed rollers between the two V-grooved rails of the slideway.
An anti-creep device eliminates this creeping of the retainer, so the slideway can be used in any mounting direction and with lower momentum motors such as linear motors. To prevent cage creep/slippage, manufacturers have used a few different approaches, such as a rack and pinion mechanism; an external attachment made of plastic gears outside of the rail; and a metal gear inside of the rail.
There is one anti-cage creep mechanism that uses a roller with round balls studded around its surface. It has the smoothest tracking motion and therefore is quieter than an externally attached toothed gear-type anti-creep device. In this (Studroller – patent pending) mechanism, creepage is prevented because the raceway has depressions that track the studs or nodules, preventing slippage in any position. By placing studs in the center roller, and machining a path along the rail, the retainer will never slip. It is suitable for high acceleration, vertical mounting, and uneven load distribution. Since the Studroller, being the simplest non-slip design, uses a ball bearing as opposed to a gear or exterior control, its cost is almost the same as a standard slideway – almost half the cost of other anti-creep devices plus, there are no redesign costs to replace a standard slideway.
NB Corporation of America
Hanover Park, IL
nbcorporation.com
Read the full-length whitepaper by clicking here.
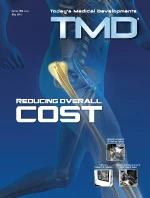
Explore the May 2010 Issue
Check out more from this issue and find your next story to read.
Latest from Today's Medical Developments
- German robotics and automation in a downturn
- Blueshift’s AeroZero
- November USMTO grow from October
- Platinum Tooling’s custom and special tooling
- Top 5 global robotics trends 2025
- Accumold’s micro molding innovations
- Methods Machine Tools, Multiaxis, announce AI solution investment
- MGS to showcase global expansion and healthcare CDMO expertise