Close up of arotary fixture with a medical device in position on the SmartScope Flash 302. Photo credit to wedlake.comMountainside Medical specializes in the contract manufacturing of complex, tight-tolerance surgical components that go into their customers’ electrosurgical instruments, laparoscopic instruments and jaws, orthopedic implants and instruments, and endoscopy devices. Mountainside Medical also offers manufacturing services with a primary core competency in high-precision machining. The company is ISO 13485 certified.
Shawn McGilvrey, director of quality, is a 6 Sigma Black Belt and helped set the quality culture in motion at Mountainside Medical. His 6 Sigma attack team – McGilvrey, two quality engineers, and two senior machinists – always look for process improvements within the company and while looking they discovered a bottleneck in their quality process for a particularly complex part. In the workcell for a pair of 11-1/2" long parts made from aluminum extrusions there are 25 important feature relationships on both sides of each part that need to be measured. These dimensions have typical tolerances of ±0.005" and ±0.001", with some tolerances as tight as ±0.0008" and ±0.0008"/-0.0000. The parts are made on Brother 5-axis (3+2) machining centers, and the workcell includes three machines.
The original measurement process used a 2D vision system to measure each side of each part, requiring the operator to manually flip the part. Verifying all 25 dimensions this way took 13 minutes per part, resulting in measuring approximately four parts per hour. Even with sample testing, the measurement process could not keep up with the production rate.
McGilvrey’s research into possible solutions to this bottleneck led to the SmartScope Flash 302 multisensor measurement system from Optical Gaging Products Inc. (OGP). Mountainside Medical already uses two OGP SmartScope Flash 500 systems in their facility. From his experience with those systems, McGilvrey says, “We went with OGP because we were sold on the quality of the machines.”
To introduce the SmartScope Flash 302 into Mountainside Medical’s quality process, Shane Shelbourne and team designed a rotary fixture to hold both parts along the machine’s Y-axis. The SmartScope Flash 302 uses MeasureMind 3D metrology software with a part program created by McGilvrey and Quality Engineering Manager Josh McAfee – McAfee had been in training to do future part programming for the six months prior to the implementation of this particular program.
The new inspection method allows users to follow simple illustrated work instructions developed by the quality team. It is necessary to know only two things about each part – the color of the bin the part came from and its lot number. To use the SmartScope Flash 302, the operator loads the part into the rotary and hits the play button. Unlike the previous manual method, the rotary automatically flips the part under program control so all 25 features are measured without the need to touch the part.
All workcell operators on five shifts have been taught how to use the new process on the SmartScope Flash 302. The improvements are dramatic; even when originally put into place, the inspection process was so fast they were able to speed up the machining to achieve above a 90% machine utilization rate. Now with experience, the machining and inspection processes are synchronized and the original quality process bottleneck has been removed.
A single workcell operator runs all three milling machines and the SmartScope Flash 302. With its rotary fixturing in place, Mountainside Medical verifies those same 25 measurements in less than 5 minutes. Since operator time per part is only 40 seconds, this means that the required six parts per hour are measured with time to spare. All the data goes to QC-Calc, which displays all 25 results on a 40" LCD monitor above the Flash 302 in the workcell to keep all employees aware of the status. Data from this screen is also used for machine tool offset adjustments to account for tooling wear and variations in process stability. The QC-Calc data also allows Mountainside Medical to monitor and track trending data with documented corrective actions and root cause analyses. Real time Cpk values for all dimensions are used to justify the potential ship-to-stock option from the customer. Mountainside Medical is now running five shifts around the clock – three shifts each weekday and two shifts on weekends – and is now able to send statistical reports to customers upon request. In fact, they can give the customer a statistical report within 30 seconds of such a request.
The original goal of McGilvrey’s 6 Sigma team was to exceed 98% customer lot acceptance. In fact, the company quickly reached 100% lot acceptance for its 25 to 30 shipments per month. This particular Mountainside Medical customer is so confident of part quality that it allows ship-to-stock with no incoming inspection at their facility. In addition, their customer is seeing improved yields of their own products since the incorporation of the OGP SmartScope Flash 302 into Mountainside’s quality process.
Mountainside Medical continues to find ways to improve their quality processes. For example, McGilvrey plans to set up communications with the system so he can visit the customer site and remotely access the QC-Calc output in real time during Quarterly Business Reviews. With the SmartScope Flash 302, Mountainside Medical has lowered costs to customers while assuring that products are completed on time and to the highest quality expectations. This investment comes with the additional benefit of increased employee satisfaction as they appreciate how the new quality process increases the value of their company to their customers.
Optical Gaging Production Inc.
Rochester, NY
ogpnet.com/smartscope
Moutainside Medical
Boulder, CO
mountainsidemed.com
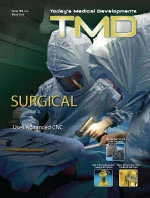
Explore the March 2010 Issue
Check out more from this issue and find your next story to read.
Latest from Today's Medical Developments
- Kistler offers service for piezoelectric force sensors and measuring chains
- Creaform’s Pro version of Scan-to-CAD Application Module
- Humanoid robots to become the next US-China battleground
- Air Turbine Technology’s Air Turbine Spindles 601 Series
- Copper nanoparticles could reduce infection risk of implanted medical device
- Renishaw's TEMPUS technology, RenAM 500 metal AM system
- #52 - Manufacturing Matters - Fall 2024 Aerospace Industry Outlook with Richard Aboulafia
- Tariffs threaten small business growth, increase costs across industries