Delivering precision and qualified surface finish in a single operation are the TNL18 sliding headstock automatic lathe and its variant, the TNL18P production machine (P = production machine), with the TNL18 variant being equipped with a few more features than the P variant.
The lathe can quickly be changed over for use with and without a guide bushing for long or short parts. The extremely long Z-travel distance of the headstock ensures the proper positioning of the main spindle, either for turning with a guide bush or without. In the standard design, the powerful main spindle is equipped with a C-axis and provided with either a direct drive with high dynamic response or a belt drive (TNL18P) and high torque in order to achieve large cutting volumes.
Simultaneous machining with multiple tools ensures high productivity levels by both machines; up to three tools may be used simultaneously on two spindles. The TNL18P production machine differs from the TNL18 variant in that the Y-axis motion of the upper turret is mapped by interpolation of the X, C, and H axes, permitting contour milling and reliable off-center, axially-parallel drilling.
A swiveling sub-spindle is fitted to an X, Y, and Z cross-slide, which simultaneously also carries the bottom tool turret. This slide, characterized by large axis travel distances, provides plenty of space for three-axis reverse side machining, even for geometrically complex workpieces.
The newly designed tool carriers, in which the rotating motion is implemented as a NC rotary axis without mechanical interlock, allows the angular positioning of the turret to be freely configured. All turret stations can be equipped with fixed or driven toolholders. The tool stock in the machine can be increased to as many as 54 tool places through dual- and multi-holders. Reducing setup time and extending productiion time. The high-precision, fast turret indexing enables a very fast chip-to-chip time of 0.3 seconds, fully comparable to any linear tool carrier.
Both the TNL18 and the TNL18P feature the solid back-working attachment that accommodates seven toolholders, of which three can be driven. In total, four stations are provided with an internal coolant supply. Each station can be controlled individually so that cutting oil is selectively supplied. The large travel distances of the sub-spindles enable stations to be occupied by more than one tool (e.g., dual drill holder).
Both machines utilize a new TRAUB for high-precision mounting of toolholders in the turret. The toolholders are seated deeper in the turret which results in less leverage effect and higher stiffness. For driven toolholders, the large shaft diameter enables insertion of roller bearings with large diameters. A quick-change system enables high-precision, smooth exchange of tools without removing the toolholder. The TRAUB compact shaft system increases the tool life and also contributes to improved surface quality.
The control, tailored to a TRAUB TNL18P, combines high performance and a high degree of reliability. The operator interface of the TX8ip (p = production) shows data on a 10.4" LCD display which are entered directly via an integrated keyboard instead of a fold-out industrial keyboard.
The WINFlexIPSPlus programming system is made available directly to the machine by means of an Ethernet interface to an external PC/laptop. With respect to basic configuration and programming, given identical kinematics the production control is fully compatible with the TX8i series – there is no need to develop new expertise about the control which maintains the TRAUB principle of user-friendly upward compatibility and continuous performance improvements.
Index Corp.
Noblesville, IN
index-usa.com
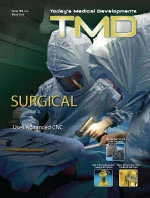
Explore the March 2010 Issue
Check out more from this issue and find your next story to read.
Latest from Today's Medical Developments
- Kistler offers service for piezoelectric force sensors and measuring chains
- Creaform’s Pro version of Scan-to-CAD Application Module
- Humanoid robots to become the next US-China battleground
- Air Turbine Technology’s Air Turbine Spindles 601 Series
- Copper nanoparticles could reduce infection risk of implanted medical device
- Renishaw's TEMPUS technology, RenAM 500 metal AM system
- #52 - Manufacturing Matters - Fall 2024 Aerospace Industry Outlook with Richard Aboulafia
- Tariffs threaten small business growth, increase costs across industries