A well-implemented multi-axis manufacturing system cuts production time,
increases throughput, and improves quality and profits.You may not realize it, but many of the products you buy actually cost a lot more than the initial price you paid for them. For example, let’s say you paid $25,000 for your vehicle. Over a five-year period, additional necessary expenses, for operating your vehicle, can easily add up to $12,000 – or approximately 50% of the price of the vehicle.
Add to that the time you spent picking out the vehicle – conducting online searches, reading auto reviews, and visiting dealerships or individual sellers. All of these things contribute to the cost of owning the vehicle. Similar logic applies in the purchase of capital equipment: It is easy to add unexpected costs to the ownership experience, both before and after the purchase. The cheap solution in the short term may end up costing you more in the long run, so exploring How Total Cost of Ownership (TCO) applies to linear motion systems is important.
The Systems
Linear motion systems, also referred to as linear modules or electromechanical actuators, typically combine a linear drive mechanism, with a linear guide system – inside a housing – to create a single linear axis. Many sizes and styles are available, which makes it easy to combine them into custom multi-axis robotic systems. Extremely small systems can be combined to create a 3-axis dispensing system for laboratory automation, for example, or very large systems may be used to build a handling system for heavy automotive components. For a more integrated system, motors, drive amplifiers, and controllers are required, and to simplify specification and ordering, some linear motion companies have begun offering complete, pre-configured Cartesian motion systems. Medical manufacturing and packaging companies often choose these pre-configured, pre-assembled systems to eliminate the time and hassle of mounting and aligning multiple axes, selecting the proper motor and drive combination, and designing mounting interfaces, which allows them to focus on their expertise.
Quantifying Costs
The TCO principle was first defined in the 1980s to quantify the cost of implementing personal computers in the workplace. Since then, TCO theory has been applied widely throughout all major industries.
For example, a well-implemented Cartesian robot, or other multi-axis manufacturing system, can not only cut production time and increase throughput, but can also improve quality and profits. If poorly implemented, however, those profits can disappear in rework, redesign, or unexpected maintenance costs.
What factors should you consider when evaluating the costs of a linear motion system? In this case, unplanned or infrequently considered costs are often found in three separate phases of implementing the system.
- Pre-purchase activities such as design and specification;
- Purchasing, which includes ordering, taking delivery, system assembly, and startup; and
- The post-purchase phase, including maintaining and repurposing your system.
Critical Starting Points
The pre-purchase phase is the most important phase of implementing a linear motion system. In this phase, the cost elements influencing TCO depend on the time required to design, specify, and purchase the appropriate linear motion system. Making good choices in the pre-purchase phase can save time in designing the system and in sourcing the components. Getting it right early also ensures smooth startup and trouble-free operation.
The key to success in this phase is sizing and selecting the appropriate linear module or modules for your system. To make the sizing and selection process easier, most reputable linear motion companies offer considerable resources in web-based sizing and selection tools. A typical 3-axis Cartesian system normally requires at least 17 hours of engineering time just to size the system to ensure you are getting the right modules to handle the application requirements.
Good sizing tools can guide the user through the main factors that need to be considered, and can cut this time to three hours or less. Coupled with automated drawing generators, which provide instant access to 2D and 3D models, the user can save $1,120 or more in engineering costs alone.
Cost savings resulting from good planning go well beyond saved engineering time. Consider the consequences of a poorly engineered system. A system that is not robust enough to handle the application, if installed, leads to terrible waste due to poor performance, lost productivity, and lost revenue from missed market launch opportunities. In addition, factor in the extra cost and hassle of removing the ineffective system, re-sizing the application, re-ordering, re-installing, and starting up a new system.
Red Tape is Expensive
Once the linear motion system is selected and designed into the application, purchasing activities begin. Some companies can provide a single part number for a complete, multi-axis electromechanical system, making the ordering process easier by simply reducing 20 or 30 part numbers down to one. The result: Savings in the number of vendors, purchase orders, and line items, further leading to time savings throughout the approval, procurement, and receiving processes.
After the linear motion system is received, a significant amount of time can be spent assembling and starting up the system. To reduce cost at this stage of the product life cycle, it is important to choose a system that is easy to install and does not require complex start-up procedures. Pre-assembled linear modules and Cartesian systems offer the least complexity in this regard. Recognizing these cost savings, many system integration companies are using pre-configured Cartesian systems to cut their costs and lead times.
Post-Purchase Phase
After the system is put into service, maintenance work can add several thousand dollars to the cost of ownership over the life of the system. Some linear products are cleverly marketed as lubed for life. However, it is important to note that the life (number of meters or revolutions traveled) is often defined with no load applied to the system. When a load of just 100 lb is applied, the life of these lubed for life components can be reduced by five times. For a machine with 1m stroke, traveling at 1m/s for 16 hours per day, this equates to approximately one full year of life that is lost. If the scheduled replacement of the linear motion system is every three years, then a lost year of life increases the replacement frequency by 33%.
To reduce maintenance or replacement costs, choose a linear motion system that incorporates full contact seals, which preserve lubrication inside the moving components and prevent contamination from entering. Re-lubrication time and effort can also be reduced by choosing a system with easy-to-access lube ports or the capability of using an automatic lube system.
Low Price in Context
Look beyond just the price provided on the vendor’s quotation and consider the costs associated with specifying, designing, purchasing, and maintaining the system. The short-term savings achieved by simply buying the products with the lowest initial purchase price are quickly eclipsed by unexpected costs that arise in these other areas. Achieving manufacturing excellence, eliminating waste, improving worker satisfaction, enhancing revenue and profits, and increasing quality can all result if TCO considerations are applied when specifying and buying manufacturing technologies.
Bosch Rexroth Corp.
Buchanan, MI
boschrexroth-us.com
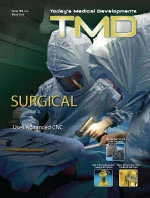
Explore the March 2010 Issue
Check out more from this issue and find your next story to read.
Latest from Today's Medical Developments
- Kistler offers service for piezoelectric force sensors and measuring chains
- Creaform’s Pro version of Scan-to-CAD Application Module
- Humanoid robots to become the next US-China battleground
- Air Turbine Technology’s Air Turbine Spindles 601 Series
- Copper nanoparticles could reduce infection risk of implanted medical device
- Renishaw's TEMPUS technology, RenAM 500 metal AM system
- #52 - Manufacturing Matters - Fall 2024 Aerospace Industry Outlook with Richard Aboulafia
- Tariffs threaten small business growth, increase costs across industries