
Producing high-precision profile inserts requires that tapered diamond grinding wheels are dressed regularly. The preferred grinding tool for machining profile inserts is often the tapered or V-shaped diamond grinding wheel, which must be dressed – brought into the correct geometric form – routinely to ensure proper grinding results.
Extremely precise tapered diamond grinding wheels often feature an edge radius of just a few hundredths of a millimeter and are correspondingly sensitive, so the right dressing technique is essential. Haas Multigrind engineers recommend the XING dressing technique in which the dresser wheel is positioned at a 90° angle, unlike other techniques where it’s positioned parallel to the grinding wheel axis. The silicon carbide or corundum wheel can be used for dressing and with the NC-controlled process, the grinding wheel radius can be generated with the circumference of the dresser wheel, maintaining a consistent contact surface and pressure between dresser and grinding wheels. Benefits include lower pressure loads and higher profile accuracy.
Dressing without unclamping, re-chucking
Haas Multigrind XING dressing is performed inside the grinding machine, eliminating the need to unclamp and re-chuck the grinding wheel. This improves dimensional accuracy, while the grinding wheel offers better radial and axial runout to generate better surfaces. Operators can hear the wheel sounds better during grinding.
Haas engineers are expanding XING applications, using the technique to profile grinding wheels, grinding pencils or quills, and grinding wheels with other grain types, as well as ceramic and hybrid-bonded grinding wheels. As a result, many different wheel contours can be dressed using grinding machines such as the Multigrind CU and Multigrind CA. However, this is only possible if the option for direct or indirect wheel probing is available. A noise-sensing system is always required for setting up, optimizing, and operating the dressing process. For V-shaped wheels with a 30° included angle, the wear depends greatly on previous wheel damage, so existing wear behavior must be measured and compensated.
Cross-dressing to XING-dressing

Mechanical engineers at Haas grin when asked why this dressing techniques is now called XING dressing and no longer cross-dressing. In English, cross-dressing refers to, “the act of wearing items of clothing and other accoutrements commonly associated with the opposite sex,” not a phrase associated with surface finishing.
In American vernacular XING is the abbreviation for crossing – a much better fit.
Haas Multigrind LLC
www.multigrind.com
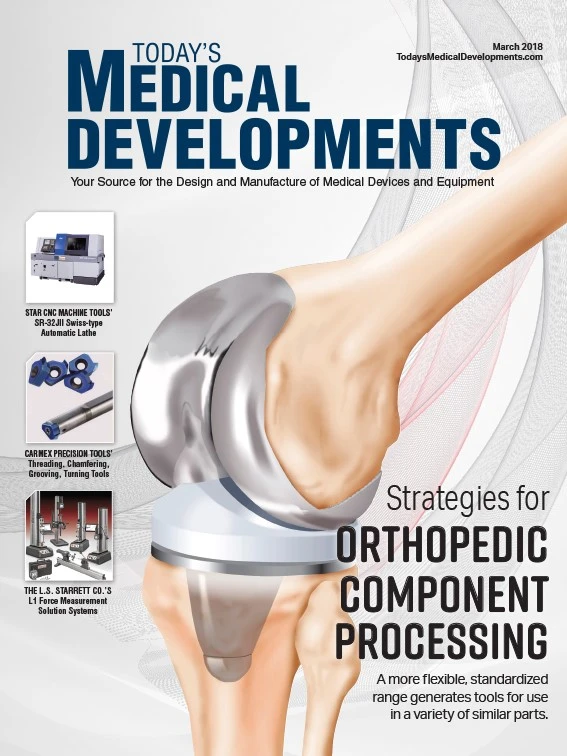
Explore the March 2018 Issue
Check out more from this issue and find your next story to read.
Latest from Today's Medical Developments
- Minalex celebrates 60 years of excellence in miniature aluminum extrusions
- Tormach’s Chip Conveyor Kit for the 1500MX CNC Mill
- #39 - Lunch & Learn Podcast with EMUGE-FRANKEN USA and Okuma America
- Significant expansion for Intricon
- REGO-FIX’s powRgrip toolholding system
- Birk Manufacturing achieves ISO 13485 recertification
- AdvaMed’s Medical Innovation Agenda for the 119th Congress
- SW North America's BA 322i twin-spindle CNC