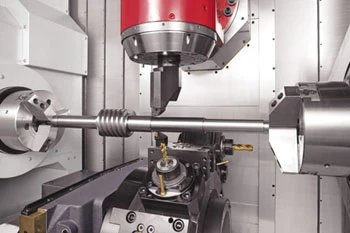
Customers are looking for increased productivity from integrated mill turn centers employing basic cutting processes. Mori Seiki may have the answer.
Kicking-off this special presentation, Dr. Masahiko Mori, president of Mori Seiki, noted that the NT Series has been in the making for 3 yrs. Beginning in 2002 and aiming to produce a "next generation" mill-turn center, hundreds of customers were surveyed to find the weak points in existing multi-axis machining centers. Listening to customer responses, it was unexpectedly discovered that there was not much 5-axis machining being performed.
Using multi-axis machines, parts were simply being machined by a combination of lathe and machining center functions. And, according to those surveyed, O.D. turning was the most utilized function. That being the case, Mori Seiki decided to focus on the lathe and the machining center functions of the multi-axis center, to ensure that these functions were not inferior to machines dedicated to these functions on an individual basis.
To capitalize on the turning ability of a lathe and the cutting ability of a machining center means the NT Series would require a new design from the base up.
Beginning with a new stronger flat bed to hold the column and headstock and support the DCG structure and high-performance spindle, the new design focuses on maximizing rigidity and cutting performance.
The box-in-box construction supports the saddle at both ends, precisely guiding and driving moveable parts at their centers of gravity in a balanced manner to promote high-speed and high-acceleration. An octagonal ram construction provides maximum ram and cross rigidity. In addition, by making the ram in the form of an octagon, the slideway forms a V-shape, creating precise linearity.
Combining the capabilities of a direct drive tool spindle, 2 headstock spindles, and a tool turret with a built-in milling motor, the NT Series provides a wide range of machining variations from raw material to completion in one setup.
Especially well suited for products requiring extremely tight tolerances from aerospace to medical devices, NT machines handle simultaneous milling and turning operations, grinding, and hob cutting. For example, turning possibilities with the tool spindle and turret include O.D. / I.D. cutting, drilling, and I.D. threading. Milling possibilities include O.D. milling, O.D. hole machining, and ball-end milling. Operations like cut-off, face cutting, and end-face hole machining and tapping can be handled with headstock spindle 2. Angular machining is possible only with the tool spindle.
As the tool spindle, turret, and headstock spindles operate simultaneously, an advanced level of control has also been designed with interference check functionality. MAPPS III, a third generation panel computer is equipped with machine interference check functionality for integrated mill / turn centers, and high-speed cycle functionality.
Interference is completely checked in 3 dimensions for spindles, work, soft jaws, tools, holders, and turrets. Machine models and standard tool model data are installed as standard. In addition, jaw and tool models are automatically set from soft jaw forming and tool-length measurement set-up data. Mechanical collisions are prevented via program operation from set-up due to interference detection in automatic and manual operation modes. Because MAPPS III has ample processing capacity, the simulation can be accomplished in real-time. According to Mori Seiki, it is possible to reduce programming time and raise productivity by 50%, due to high-speed canned cycles and extensive menus.
Dr. Mori is confident that once it is formally introduced at the EMO Show in Hannover, Germany this month, the NT Series Integrated Mill Turn Center will become the flagship for integrated machining. In addition Mori Seiki believes the NT Series will lead the manufacturing industry into a new era for integrated mill / turn centers.
No doubt, my Thursday in Japan with Mori convinced me he is about to create a new round of excitement in the world of machining.
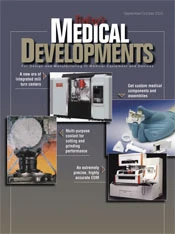
Explore the September 2005 Issue
Check out more from this issue and find your next story to read.
Latest from Today's Medical Developments
- Turnkey robotic systems are already behind the times
- You can still register for March’s Manufacturing Lunch + Learn!
- HERMES AWARD 2025 – Jury nominates three tech innovations
- Vision Engineering’s EVO Cam HALO
- How to Reduce First Article Inspection Creation Time by 70% to 90% with DISCUS Software
- FANUC America launches new robot tutorial website for all
- Murata Machinery USA’s MT1065EX twin-spindle, CNC turning center
- #40 - Lunch & Learn with Fagor Automation