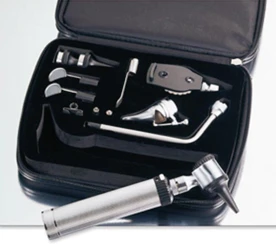
THE THREAD ROLLING PROCESS Thread rolling is a metal working process that produces threads and other forms on round metal parts with no metal removal. It is done entirely by moving the metal under pressure while rotating the workpiece. The resultant part is stronger than its typically cut counterparts because the grain structure of the workpiece "flows" into the form, rather than being cut away. Carbon steels, stainless steels and many hi-tensile alloys such as titanium and inconel can be rolled
LIFTING AND MOVING APPLICATIONS
Rolling can be done by the thru-feed
method where continuous lengths of
thread are rolled on bars or studs. Jack
screws and actuators of many types are
rolled this way, and there are many applications
for these screws in the medical
field. There are a wide variety of thread
forms available, such as standard UNR,
acme and ball form, all available in single
or multiple lead, to fit any design criteria.
Hospital beds are one application where jack screws are already in use and, as the new demands for special lifting devices to assist hospital staff increase, many more applications will develop that require these screws.
KNURLING APPLICATIONS
Knurls can be rolled in a wide variety of
forms and pitches, including: straight,
diagonal, male diamond and female diamond,
typically from 12 TPI to 80 TPI.
Knurls are used for grips on hand tools,
for anti-rotation/anti-pull out on injection
molded plastic assemblies and to create
interference on press-fit assemblies.
Knurls can be rolled on solid parts as well as thin-walled hollow parts in a wide variety of materials.
FAST, ECONOMICAL AND SUPERIOR
QUALITY
The thread rolling process is faster than
conventional machining with typical infeed
rolling times at 1 to 2 seconds per piece
and thru-feed rolling times and typically 12
feet per minute.
Since the material "flows" during the thread rolling process, the beginning part diameter, or blank diameter, is smaller than the finished diameter. This results in a considerable savings in material compared to conventional machining, because there is no scrap.
The surface finish on the flanks of a rolled thread is burnished as a result of the forming process, and therefore is superior to most milling or grinding.
Thread rolling machines are versatile and can adapt to a variety of part shapes. Justifying a machine can be easier than you think, and the cost savings and improved part quality will certainly help your bottom line.
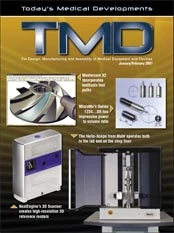
Explore the January February 2007 Issue
Check out more from this issue and find your next story to read.
Latest from Today's Medical Developments
- The role of robotics in precision medical device manufacturing
- Swiss Steel Group’s UGIMA-X machinable stainless-steel sets
- #51 - Manufacturing Matters - The Impact of M&A in MedTech 2024
- Visual Components: 25 years of simulation and programming software innovation
- Zimmer Biomet announces definitive agreement to Acquire Paragon 28
- Discover an innovative technology for EMI/ESD/TVS suppression
- Teleflex to acquire BIOTRONIK’s Vascular Intervention business
- Innovation at Global Industrie 2025