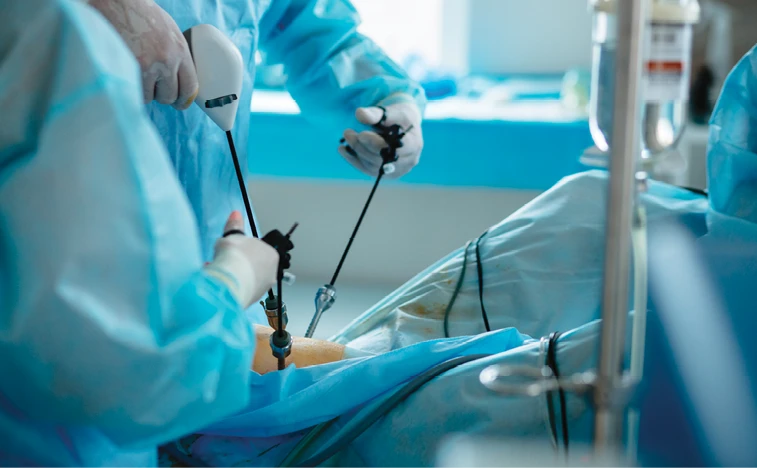
©IRYNA- STOCK.ADOBE.COM

Material failure is a major or possible cause for 30% to 40% of medical device recalls by the U.S. Food & Drug Administration (FDA), according to a recent study by research and development company Battelle. Material failures can result when the selection process does not consider the device’s complete use cycle application requirements (including functionality, performance, and regulatory requirements), the manufacturing process (including secondary operations), and the environment in which the device will be used (which can involve various exposures ranging from ultraviolet (UV) light to harsh cleaners to high-temperature sterilization).
Surgical devices have especially demanding use cycles. Material selection may need to factor in trends such as device miniaturization for laparoscopic and robot-assisted laparoscopic surgery, efforts to reduce hospital-acquired infections (HAI), and ergonomics to optimize surgical precision and comfort.
Application environment
One important consideration is whether the application is single-use or if it will be used multiple times. Single-use devices are sterilized using gamma radiation or ethylene oxide (EtO), while reusable devices undergo steam autoclaving or low-temperature hydrogen peroxide sterilization. As reusable devices must withstand repeated sterilization cycles that could accelerate environmental stress cracking; material considerations should include thermal cycling and hydrolytic stability.
Surgical devices may be exposed to strong disinfectants and chemical wipes used to combat HAIs, bodily fluids, and saline. Under the intense lighting of operating rooms, they must also resist UV degradation that can cause embrittlement, cracking, and discoloration.
Another factor is whether the device will be operated by the surgeon by hand or with a surgical robot. A human user may require comfort, grip, and flexibility that a machine would not. For instance, for consistency and precision, a robotic surgical device would require dimensional stability and the ability to maintain tight tolerances.
Application requirements
To meet surgical device requirements, designers need several thermoplastic materials with specific attributes. Properties may be inherent to the polymer family, or they can be enhanced using additives and reinforcing fillers or fibers.
To maintain part performance and consistent operation under stress, such as force, a material for a surgical device may require creep resistance to prevent part deformation throughout time and fatigue resistance to withstand repetitive motion. A related issue is wear performance: how well a material withstands the friction caused by moving against a counterforce. Slip additives incorporated in resin can help reduce the coefficient of friction in wear parts.
Dimensional stability, also a potential requirement, is influenced by polymer morphology, coefficient of thermal expansion, and water absorption.
Aesthetics may not be as important for surgical devices as for home healthcare devices, but appearance is still a consideration. Some components must be transparent for clinical reasons, while others may be colored to indicate functionality. A material’s aesthetic properties should resist fading, abrasion, and color shift.
Rheology (flow) plays a key role in processing. Thermoplastic characteristics such as melt viscosity rate and shear behavior should be considered, especially when molding a thin-wall or highly complex component that requires higher flow.
Biocompatibility is a basic regulatory requirement for materials used in contact with the human body. Tests for biocompatibility include Biological Reactivity Testing (USP Class VI), and ISO 10993, Biological Evaluation of Medical Devices. Biocompatible plastics intended for medical devices include medical grades of polycarbonate (PC) and PC copolymers, PC/polybutylene terephthalate (PC/PBT), acrylonitrile butadiene styrene (ABS), PC/ABS, polyether ether ketone (PEEK), polyetherimide (PEI), polyvinyl chloride (PVC), polyethylene (PE), and polypropylene (PP).
In cases where devices are powered, materials must provide flame retardance.
Manufacturing process
A thermoplastic material should support production goals for high volume, speed, and cost. However, material selection may be limited by equipment and the molder’s capabilities.
Most thermoplastic grades are tailored for specific molding processes. A polymer’s morphology, molecular weight, and viscosity affect processing speed, mold filling, and shrinkage. Thermoplastic supplies come matched to equipment – pellets for injection molding and extrusion, sheet for thermoforming, and filaments for fused deposition modeling. Suppliers often make different versions of a material for specific processes, giving designers greater processing flexibility.
Some applications require secondary operations for assembly, labeling, or aesthetics, requirements that may influence material selection. If secondary pad printing is involved, the material will need suitable surface energy and compatibility to optimize link application. It may require a surface treatment (example: corona treatment) to alter the surface energy.
Some materials and processes can help improve time-consuming, costly secondary steps. Overmolding a thermoplastic elastomer onto a rigid substrate can eliminate the need for adhesives. Choosing a compound with inherent lubricity or molded-in color avoids post-molding of lubricants or paint.
Materials suppliers
Several variables come into play when selecting thermoplastics for an application. Medical device manufacturers may have some materials expertise, but many lack the knowledge, resources, and application development background of experienced material suppliers. Involving suppliers at the outset of the development cycle can save time, improve chances for success with a new device, and bring fresh perspectives to a project.
Major material suppliers may offer expertise in the medical device sector, many years of translatable experience from working in multiple industries, and a deep knowledge of their candidate materials, part design, and processing. They can also provide support and guidance on regulatory requirements, although the customer must ultimately make its own determination. These resources and suggestions can help device manufacturers address specific application requirements and help mitigate potential risks such as mandatory recalls.
SABIC
https://www.sabic.com/en

Explore the May 2019 Issue
Check out more from this issue and find your next story to read.
Latest from Today's Medical Developments
- HERMES AWARD 2025 – Jury nominates three tech innovations
- Vision Engineering’s EVO Cam HALO
- How to Reduce First Article Inspection Creation Time by 70% to 90% with DISCUS Software
- FANUC America launches new robot tutorial website for all
- Murata Machinery USA’s MT1065EX twin-spindle, CNC turning center
- #40 - Lunch & Learn with Fagor Automation
- Kistler offers service for piezoelectric force sensors and measuring chains
- Creaform’s Pro version of Scan-to-CAD Application Module