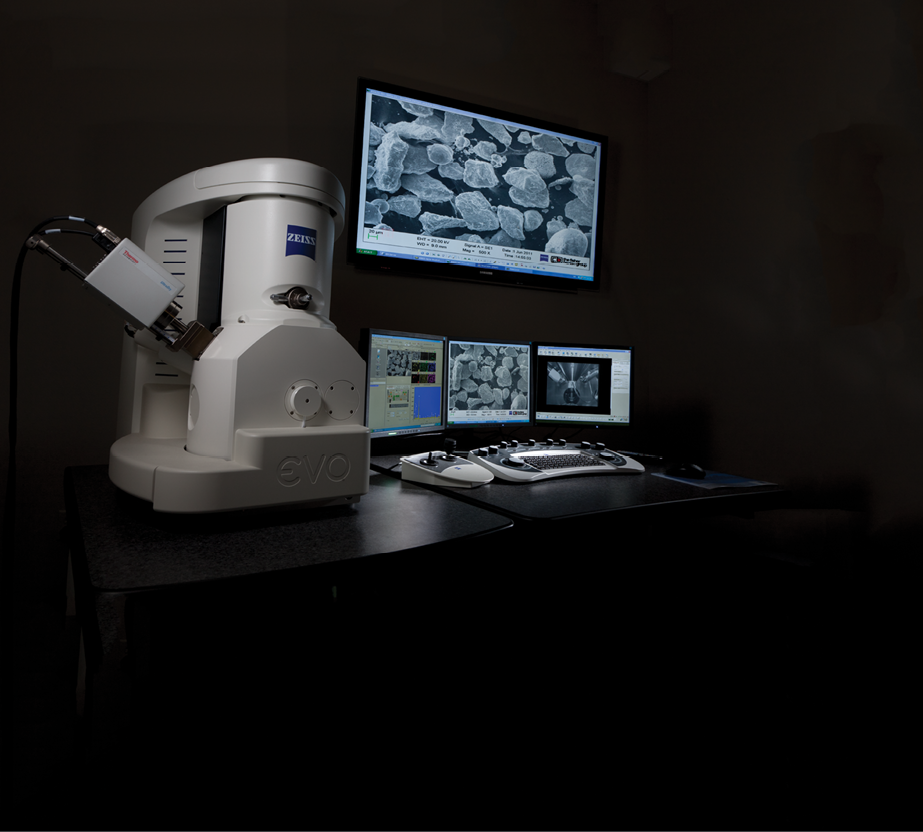
The earliest documented evidence of thermal cautery – the use of localized heat to cauterize an incision and limit blood loss – dates to 3,000 B.C. in surgeries performed by the Egyptians. Surprisingly, very little changed until the first electrosurgeries were performed in the 19th century, when surgeons experimented with electric current to cauterize an incision with a heated wire. True electrosurgery, and the forerunner of today’s monopolar and bipolar electrosurgical systems, began with Dr. William Bovie, and his electrosurgical unit invention in 1926 (a Bovie) capable of delivering an alternating current at high frequency (RF) and various voltages for surgical cutting and/or to control bleeding.
Today, more than 80% of all surgical procedures involve electrosurgery. Surgeons in every specialty, armed with an array of hand-held and robotically held electrosurgical devices, often coupled with minimally invasive surgical techniques, can minimize blood loss, procedure duration, patient time under anesthesia, and recovery time. While much of the credit goes to the skillful surgeons and innovative electrosurgical device manufacturers, there’s another important player: thermal spray coatings providing critically important surface properties for these devices.
Bipolar takes charge

Both monopolar and bipolar devices use electrical current from a generator unit to apply a highly controlled electrical current and generate local heat that, when applied by a surgical instrument, cuts, coagulates, ablates, or dissects tissue. They differ in the path the current takes. The monopolar device (the active electrode) directs current through the tissue, which then exits the patient through a grounding electrode plate/pad placed on the patient. A bipolar device can be as simple as forceps or scissors, with current flowing from the negatively charged electrode, scissor blade or forceps tip, through just the tissue held between the blades or tipjaws, to the positively charged electrode on the other positively charged blade or tipjaw. Unlike the monopolar device, no current flows through the patient. The current flow is much more localized, making bipolar devices ideal for more surgeries performed on small areas requiring greater precision, such as laparoscopy. Additionally, bipolar devices are ideal for use for patients with implanted devices where current from a monopolar device might pass through the device and cause a short circuit or misfire.
Bipolar electrosurgical devices now come in a multitude of sizes and designs, with many featuring increasingly complex, extremely precise geometries for highly specialized, delicate surgical applications. Almost all are made of metal, primarily stainless steels, and all are designed to conduct an electrical current. The precise application of an electrically insulating (dielectric) coating to the metal substrate surface of the device has never been more critical. Without this insulation, electrical arcing can occur, causing the device to short out and fail – or worse, injure the surgeon and patient. Additionally, many devices require a second, thermal barrier coating to protect surgeon and patient from an increase in the temperature of the device surfaces not intended for tissue sealing.

Ground zero for dielectric coatings
Almost from the inception of the first bipolar electrosurgical devices, TST Engineered Coating Solutions, a Sun Prairie, Wisconsin division of Fisher Barton, has been at the forefront of developing and applying advanced dielectric coatings, as well as thermally insulating coatings, coatings for extreme wear resistance, and coatings with antimicrobial properties. Bipolar electrosurgical devices have benefited from specialized coatings and the surface properties they deliver. Devices of this type operating with a TST engineered coating now number in the millions.
The tremendous variations in instrument size, shape, geometry, material, and end application prohibit a one-size-fits-all approach when developing a coatings solution. At TST, the process starts with a dedicated R&D team, including materials engineers working closely with customers to fully understand the instrument and the desired surface properties, along with the environment in which the instrument will function. A variety of coating properties are considered along the way, including dielectric strength, porosity content, adhesion, oxidation, hardness, and microstructure – all metallurgically examined and tested during the development process to ensure optimum engineered coating design.
Ultimately, a coatings material is selected and paired with the correct thermal spray process. TST can apply coatings through a variety of processes all characterized as thermal spray, each uses combustion of gasses or electrical energy to melt feedstock material in wire, powder, or rod form. The melted material is atomized and propelled to a prepared surface where the material immediately freezes and builds up to create a coating. Thermal spray coating processes are extremely versatile and can create coatings from an almost endless number of materials.
Since its first thermal spray coating application for a bipolar electrosurgical device, TST developed a family of oxide ceramic coatings proven to deliver dielectric properties across the widest spectrum of applications, whether for high or low voltages, DC or RF. Ceramics are more durable, and wear- and corrosion-resistant than other coatings such as polymers, and can be formulated from common materials including oxides of different metals, as well as other materials, alloys, and compounds. Oxide ceramic coatings can meet or exceed the performance criteria specified for the majority of devices, including:
- Dielectric strengths of 1000V/mil or greater
- Typical hardness of 1,100 Vickers
- High density with porosity levels less than 0.5%
- Excellent adhesion with bond strengths greater than 8,000psi
- Coating thickness: 0.001" to 0.020"
- High compressive strength
- Effective dielectric properties across a wide range of temperatures
TST has perfected the thermal spray technologies and techniques for applying these coatings with pinpoint accuracies, down to an area as small as 0.012" (0.3mm) in diameter. Special TST fixturing, tooling, cell design, and process controls are engineered to meet the needs of each application, holding the tightest tolerances for volumes of as few as one part to thousands.

This family of oxide ceramic coatings also include versions to provide thermal insulation. The thermal conductivity of these coatings can be controlled with variations to the composition of the coating chemistry and its structure, with conductivity as low as 0.5W/mK easily achieved.
Where wear resistance is needed, coatings composed of oxide ceramics, carbides, or hard metals can be deposited to add extreme wear resistance. These coatings with hardnesses as high as 1,500 Vickers and densities greater than 99.5% can greatly extend product life and add considerable value.
More resources, faster development
Centrally located in the Midwest, TST has an R&D team dedicated to the development of new solutions. Depending on the tooling/fixturing requirements of a particular product, TST can have the first prototypes available to the customer for testing and validation in a few weeks. TST additionally has access to all the resources of its parent company, Fisher Barton, to improve the design and functionality of customers’ products. The Fisher Barton Technology Center is fundamental in its ability to understand and apply the materials and coatings needed to improve customer products.
TST Engineered Coating Solutions, A Fisher Barton Co.
https://www.tstcoatings.com
https://www.fisherbarton.com

Explore the December 2022 Issue
Check out more from this issue and find your next story to read.
Latest from Today's Medical Developments
- Machine learning framework enhances precision, efficiency in metal 3D printing
- SkillMill – 60-year-old milling machine with digital twin
- Lumetrics’ OptiGauge II EMS
- EMI completes installation of 128-axis CNC turning & milling machine
- Ottobock invests in innovative technologies from MIT start-ups
- Air Turbine Technology's high-speed live tools for Swiss Lathes
- Sandvik announces several software acquisitions
- Dart Controls’s EZ VFD, variable frequency drives