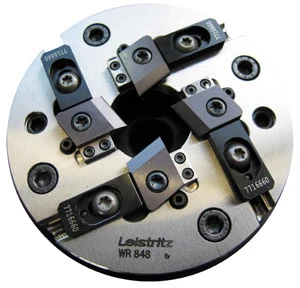
FOR MANUFACTURERS LOOKING FOR A FASTER AND MORE ECONOMICAL METHOD OF PRODUCING BONE SCREWS, WHIRLING AS A SEPARATE OPERATION MAY BE JUST WHAT YOU ARE LOOKING FOR.
Leistritz, a machine tool builder based in Nürnberg, Germany, with a branch office in Allendale, NJ, has developed a complete line of multi-axis CNC whirling machines. These machines have been designed specifically for whirling and have the inherent rigidity for cutting deep, wide profiles in tough materials. These whirling machines also have the necessary accuracy for cutting precision, close-tolerance screws, making them ideal for production environments where there is minimal time to do routine maintenance.
For the past several years, the medical device industry has seen the whirling process come into its own. This very efficient and fast method of producing threads has recently been integrated into swiss type screw machines. This combining of operations goes against the "lean" ideals of high productivity by performing many operations in a single machine. It is the philosophy of Leistritz Corporation that separating operations is more productive. The very features that make swiss-type turning centers unbeatable for turning small diameter and long shafts, screws or spindles are exactly what make them less efficient whirling machines. Feeding of the bar material through a guide collet has the disadvantage of not permitting continuous rough and finish turning over a long length, so whirling a long screw requires incremental turning and whirling steps until the whole screw length is achieved, or whirling the screw without turning the blank to the thread major diameter first. Both of these alternatives are not only time consuming, but they are also inaccurate.

A sample of bone screw variety with different lengths all whirled on one machine setup.
The Leistritz concept is to turn bone screw blanks in existing swiss-type turning centers without the thread. This would allow an even shorter cycle time and greater throughput per machine. Then, with a whirling only machine, whirl the thread. Leistritz whirling machines have the necessary following supports to permit whirling of screws with any profile in virtually unlimited lengths, in the shortest possible time. Dedicated whirling machines can outperform whirling in a turning center by a factor of 2, or a possible 3 to 1 ratio. Most bone screws, even in their longest designs and in either 316L stainless steel or Titanium, are whirled in less than one minute.

A Leistritz Pw-65-MED dedicated bone screw whirling machine with full automation for high production of screws with various lengths.
The Leistritz PW-65MED machine has a very unique automatic parts loader and hopper system. The pre-turned blanks with either finished or unfinished heads are dumped into the vibratory hopper, which aligns the screw blanks to be oriented tip first and funneled to the staging area. Once "on deck" for the loading process, each screw is measured for length with a light beam, and the proper CNC program is selected to run the appropriate screw length. This is a valuable tool, seeing as how nearly all bone screws are produced in families of the same diameter. Typical bone screws of the same family vary only in length from 10mm to a maximum of 100mm in 5mm increments. With the Leistritz PW-65MED machine, all screws within the same family can be produced simultaneously without any setup.
This processing also allows cell integration of a number of turning centers to each whirling machine. Typically, four, possibly five turning centers produce the blanks (of various lengths) for a single PW-65MED whirling machine.
Medical screw manufacturers throughout the country and in Europe are quickly discovering that this a better way to process their production. When production volumes increase to the point where more than one turning center is required, this separation of operations saves even more by maximizing the utilization of all machines in a cell. The low tooling costs, combined with short cycle times and virtually no setup time, really proves beneficial to their bottom line.
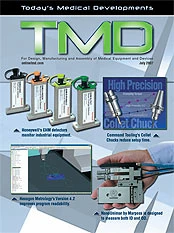
Explore the July 2007 Issue
Check out more from this issue and find your next story to read.
Latest from Today's Medical Developments
- Best of 2024: #8 Article – Perfecting the CMP process for surgical blades
- Best of 2024: #8 News – Johnson & Johnson to acquire Shockwave Medical
- Best of 2024: #9 Article – Strategy Milling combines old and new for precision dental restorations
- Best of 2024: #9 News – Global robotics race
- Best of 2024: #10 Article – Designing medical devices for every user
- Best of 2024: #10 News – 4 predictions for 2024: AI set to supercharge robotic automation
- Children’s National, FDA collaborate to advance pediatric device regulatory tools
- LK Metrology’s eco-friendliness CMMs