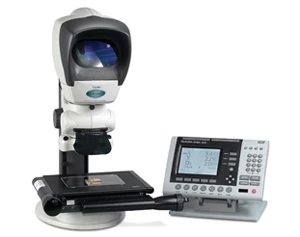
Rowan Precision has been producing precision turned components for more than 20 years. At its Birmingham, England facility, use of the lastest technology, Swiss Machining centers, allows for the production of a wide range of components ranging from 0.5mm diameter to 85mm in diameter. Rowan has an order book containing over 500 different component types, including aluminum alloys, stainless steels and plastics such as PTFE.
Rowan Precision has chosen two non-contact measuring systems from Vision Engineering, confirming that customers' tight tolerances are adhered to. Kestrel is a 2-axis system, used for rapid, shop floor gauging applications. Hawk is an automatic 3-axis platform, used for more challenging measurement tasks where pre-programmed inspection routines can be run
The products manufactured by Rowan Precision tend to be small, precision turned components with a number of complex internal and external features. A typical application is the production of defense specification connectors, which have exact requirements, backed up by component traceability. These connectors have a number of broached key features that ensure that the finished component will only locate into the correct socket. Accurate gauging of these features proved to be an extremely difficult and lengthy operation. When using a shadowgraph, the component had to be sectioned before a measurement was made. This not only destroys the part being measured, but it also consumes an extreme amount of time for the operator. The Vision Engineering equipment provides a true, optical view of the connector, allowing the operator to view both profiles and surface features. Using a combination of back lighting as well as incident illumination, even highly- reflective, curved materials can be clearly viewed and measured.
Inspectors use the Kestrel as a shop floor measuring tool because it is simple to use, robust and fast. The Kestrel is located alongside the CNC plant, allowing components to be taken directly from the machine for immediate inspection and measurement. It is straightforward to use, so operators and quality staff are comfortable making basic measurements.
The Hawk is a more capable piece of equipment and is located in the QC laboratory where it is used by specially trained Quality personnel. Hawk is a motorized 3-axis system with automatic Video Edge Detection (VED). This is run alongside a QC5000 PC package, which allows for measurement routines to be programmed and stored for future use. When frequent or multiple checks are needed on a particular component, the Hawk proves to be a useful tool for Rowan Precision, as a previously configured program can be recalled and automatically run. All the Quality Engineer has to do is locate the component on the Hawk's stage and start an inspect cycle. Once the routine is completed, a data report can be stored and printed.
Chris Kent, a director of Rowan Precision explains, "We wanted to find a measuring solution that would work for our entire range of production, from complex connectors to stainless steel and plastic medical devices. Hawk and Kestrel offer us this flexibility and give us confidence in the accuracy and repeatability of our processes."
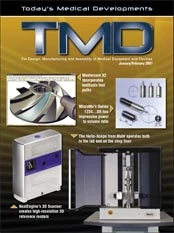
Explore the January February 2007 Issue
Check out more from this issue and find your next story to read.
Latest from Today's Medical Developments
- The role of robotics in precision medical device manufacturing
- Swiss Steel Group’s UGIMA-X machinable stainless-steel sets
- #51 - Manufacturing Matters - The Impact of M&A in MedTech 2024
- Visual Components: 25 years of simulation and programming software innovation
- Zimmer Biomet announces definitive agreement to Acquire Paragon 28
- Discover an innovative technology for EMI/ESD/TVS suppression
- Teleflex to acquire BIOTRONIK’s Vascular Intervention business
- Innovation at Global Industrie 2025