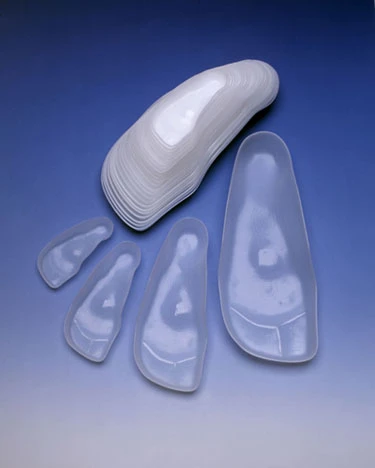
The use of computer aided design and manufacturing software plays a key role in accurately and consistently producing footplates for children's braces.
Cascade DAFO of Ferndale, Wash., custom tailors flexible foot and ankle braces to meet the needs of children with neurological or neuromuscular problems that disrupt muscle control and inhibit their ability to stand and walk. A DAFO (Dynamic Ankle Foot Orthoses) brace correctly positions the foot and ankle to increase stability and help the child walk on his or her own.
"The majority of our braces are for kids, although we do some for adults as well," says manufacturing engineer Mike Walls. "For a brace to be effective, the child must want to use it. It has to be comfortable and should also be fun to wear."
The design of a custom brace begins at a practitioner's office, where a cast is made of the child's foot and ankle. During the casting process, the patient's foot rests in a sole-shaped footplate and the casting material is wrapped around both the foot and the footplate. The footplate positions the foot and helps assure the accuracy of the cast. When the cast is complete, it is carefully removed and the footplate is taken out for re-use. The cast is sent to Cascade DAFO, where it is filled with plaster. The resulting form is an exact replica of the child's foot, and it is used to size the brace components to achieve a personalized fit.
From about the time of its founding in 1982, Cascade DAFO made the footplates using resin molds taken from hand-carved originals. According to Walls, those footplates worked better than no footplates, but not much."
Because each mold was hand carved, there was no simple way to make changes or scale the molds to create different sizes. Left and right footplates weren't exactly the same. And because they were rather flat, the footplates tended to move around under the foot, requiring careful placement to produce an accurate cast. "Repeatability was an absolute nightmare," recalls Walls.
To improve the process, Don Buethorn, the company's founder and a certified prosthetist orthotist, designed a new footplate to grip the foot and provide more stability and consistency. Hand-carving a shape with the contours and details that he envisioned, the new footplates were made of polyethylene and named "Polly Ethels."
A key factor in accurately and consistently producing Polly Ethels was the use of computer aided design and manufacturing software. Walls researched the various packages available and choose CopyCAD, PowerSHAPE, and PowerMILL from Delcam International for its versatility and ease-of-use.
CopyCAD is a reverse engineering program for the quick creation of high quality engineering surfaces from point cloud data captured through the scanning of physical objects; PowerSHAPE is a hybrid modeler combining surface and solid modeling capabilities; and PowerMILL is a CAM program that combines an easy-to-use interface with the latest strategies for multi-axis machining.
"We started with the mold Buethorn approved, laser scanned it, and brought it into CopyCAD. There we made modifications, trued things up a bit, and added a little more definition. We took that file into PowerSHAPE and created the outright mold shape and trim lines. We figured a scaling system and used it to scale the 28 different sizes we needed. Then we brought those files into PowerMILL and created the machining program. Finally, we milled the shapes of the molds into Renshape polyurethane tooling boards, using a Haas four-axis milling machine and carbide tooling. The tooling board molds are then used in an automated thermoformer to produce the footplates," explains Walls
"Using CAD software guarantees that the left and right footplates are symmetrical. Scaling is absolutely uniform, so we are very much in control of our sizing," continues Walls.
Producing the 28 required sizes (56 footplates) was simply a case of making mirror image files for left and right and scaling the results. Changes and modifications are made across the entire range of sizes immediately. "Using the hand-carving method, it would take a couple of hours to make one footplate mold. You would be lucky to get two pairs a day," comments Walls.
Walls feels the main advantage of the Delcam software is the ability to work with a polygonized model. "That's a huge savings because we don't have to worry about the added process of having to wrap a surface around the model. If we want to use a shape as a base for a product, we are able to just grab the raw data and start working with it in PowerSHAPE." He pointed out that PowerMILL also offers the capability to work with a polygonized model. "We don't have to turn the model into surfaces to bring it into the milling program," he said. "I've done a lot of programming and used a lot of systems, just about anything out there, certainly CAD wise. There are a lot of good CAD and milling programs out there, and a lot of them are less money than Delcam software. But when it comes right down to all you get, it was worth the difference.
"The footplates aren't a direct product for the patient, but they are such a help to the practitioner when casting. They help the brace fit, which is the only thing that Buethorn really worries about. With the savings in labor and manufacturing time, the cost is less than the original footplates, and it's passed on to the customer," adds Walls. "Delcam's family of software is a large part of our ability to achieve our main goal of helping children walk."
Delcam International Inc.
Windsor, Ontario
delcam.com
Circle 202
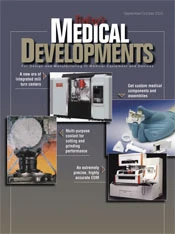
Explore the September 2005 Issue
Check out more from this issue and find your next story to read.
Latest from Today's Medical Developments
- Turnkey robotic systems are already behind the times
- You can still register for March’s Manufacturing Lunch + Learn!
- HERMES AWARD 2025 – Jury nominates three tech innovations
- Vision Engineering’s EVO Cam HALO
- How to Reduce First Article Inspection Creation Time by 70% to 90% with DISCUS Software
- FANUC America launches new robot tutorial website for all
- Murata Machinery USA’s MT1065EX twin-spindle, CNC turning center
- #40 - Lunch & Learn with Fagor Automation