
Medical devices often remain the same, with patients or medical professionals finding work-arounds to improve functionality or safety. Medovex designers decided that those ad hoc adjustments weren’t enough to improve the standard IV pole. So, they redesigned it to offer, as their company mission states, “Better Living through Better Medicine.”
Peter Blankenship, director business development at Medovex took a few minutes to talk with Today’s Medical Developments magazine about the Streamline IV Suspension System (ISS).
TMD: Why did your team feel the need to redesign something as seemingly simple as an IV pole?
Blankenship: As hospitals are threatened with rising costs and limited resources of people, time, and money, they are faced with the obligation and the need to keep patients and staff safe. New technologies and products are needed to address these issues, which are of particular interest to both hospital administrators and front-line patient caregivers.
The need for the ISS is to correct the hazardous, costly, and potentially life-threatening ways in which patients and their equipment are transported. Increasing safety and efficiency is especially important as patients are accompanied with more and more equipment.
TMD: How does the ISS work with patients’ hospital beds and the need to move patients safely?
Blankenship: The ISS has two components, the bed-mount adapter and the ISS pole. The mount adapter is permanently attached to the patients’ bed, transport cart, gurney, or wheelchair, although it can be detached if desired. Nothing invasive is done to the beds when installing the mount adapter. The ISS pole can be easily attached to the mount adapter. Then, with the press of a pedal, it retracts off the floor and securely locks into the mount adapter. The ISS pole, mount adapter, and bed have now become one unit keeping the patient’s equipment close and secure while reducing the need for extra personnel to help move the equipment.
TMD: Where is the design for medical equipment done?
Blankenship: In-house in conjunction with outside engineering firms.
TMD: What were design considerations in developing the ISS?
Blankenship: Ease of use was key. If new products add extra steps to a caregiver’s normal process, or are difficult to use, they will simply bypass them, regardless of the safety benefits. Functioning with the patient’s bed was also considered as we did not want to hinder the complex functionality of hospital beds.
TMD: Were there any design challenges faced with specifying specific components?
Blankenship: The biggest challenge was getting the mount adapter to fit with various bed models while not invasively affecting the beds.
TMD: Are components sourced from standard products, custom-produced, or a combination of the two?
Blankenship: Production of the ISS is through a combination of standard and custom-sourced components.
TMD: How do the internal components come together for the final assembly?
Blankenship: The ISS pole uses a gas spring to power the retractable legs and base of the pole. The final product is assembled and packaged by a contract manufacturer and shipped directly to the customer.
TMD: How many contract manufacturers do you work with and for what parts?
Blankenship: We work with one contract manufacturer. There are a few components that the contract manufacturer obtains through outsourcing.
TMD: When moving from design to production with the contract manufacturer, did design or specified components change because an outside view offered a different approach?
Blankenship: Subtle changes were made to increase functionality and ease of manufacturing while reducing costs.
Elizabeth Engler Modic is the editor of TMD magazine. She can be reached at 216.393.2064 or emodic@gie.net.
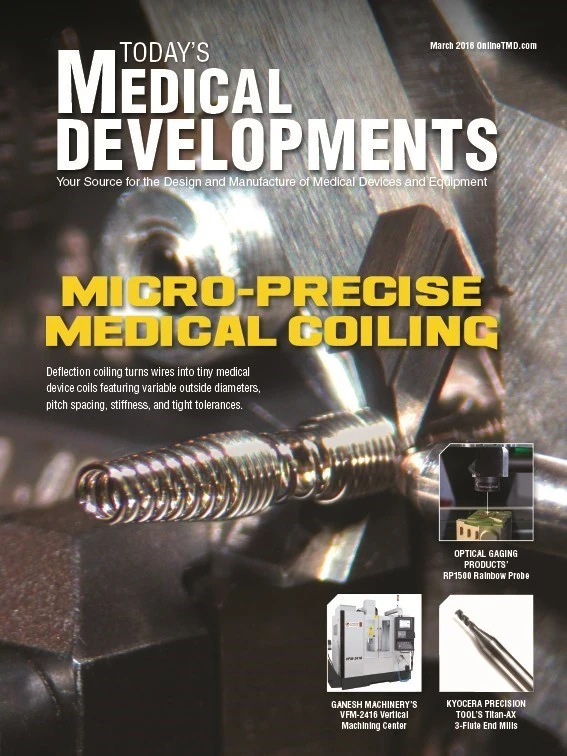
Explore the March 2016 Issue
Check out more from this issue and find your next story to read.
Latest from Today's Medical Developments
- MedTech Innovator welcomes five new industry partners
- First Article Inspection for quality control
- The manufacturing resurgence is here – are you ready?
- Workholding solutions for your business
- ZOLLER events will showcase the company’s cutting-edge innovations
- THINBIT’s MINI GROOVE ‘N TURN Acme threading inserts
- CMMC Roll Out: When Do I Need to Comply? webinar
- Metabolic research uses Siemens gas analyzers to deliver results with 99.9999% resolutions