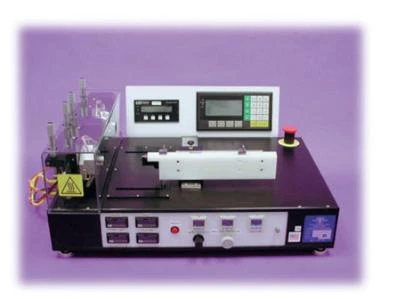
A miracle of modern medicine, interventional stent therapy opens up clogged heart and peripheral vessels to restore normal blood flow, minimize damage to the heart muscle, and reduce incidence of heart attacks. Manufacturing stent delivery systems, however, was a slow, laborintensive manual process often taking 45 minutes per system.
That changed when Machine Solutions Inc. (MSI), Flagstaff, AZ in 2001 introduced equipment engineered around patented technology to automate the processes and deliver unmatched precision and repeatability, while cutting processing time down to seconds. The automated equipment pleats and folds balloon catheters and crimps metal stents, compressing them down to small enough diameter and optimized profile for insertion into the body through a blood vessel.
The MSI machines combine patented segmental compression technology (US#6,629,350) with Renishaw RGH24/25 optical encoders to "pack the charge" for precise, predictable expandability when positioned at the point of blockage. The innovative designs have quickly made Machine Solutions a global leader of automation technologies for stent and catheter manufacturers.
30 Second Pleating and Folding
Balloon Form/Fold/Set (FFS) equipment from MSI uses the patented compression capability in a unique WavePleat Technology mechanism to pleat and compactly fold angioplasty and stent deployment balloon catheters. The WavePleat Technology process quickly produces precise, consistent, and repeatable balloon profiles without the need for operator hand folding. The automated process takes 30 seconds on average, says Scott Mickelson, project manager on MSI's design team. This compares with up to 45 minutes or longer for sequential manual pleating, folding and thermal stabilization.
"Besides the enormous labor saving for stent manufacturers, automation also ensures a more precise and repeatable process," says Mickelson. Such precision is critical. The balloon needs to be uniformly folded, he explains, so there is no interference when the stent is crimped down around it and no irregularities when the balloon and stent are expanded inside the blood vessel.
A Renishaw RGH24 encoder, mounted in a partial arc, controls wave pleat and folder motion to 5micron resolution, notes Mickelson. "We've used the RGH24 as original equipment since the introduction of the FFS machine, but recently started upgrading new machines to the smaller RGH25."
Segmental Compression Crimping
Machine Solutions also selected Renishaw encoders for its SC family of stent crimping machines. Configured as a diameter encoder, the RGH24 performs continuous crimp diameter monitoring as the stent is compressed around the folded balloon. MSI's segmental compression mechanism applies even, highly repeatable radial compression. The versatile machines accept all kinds of stent configurations bare metal, polymercovered, drugcoated, balloonexpandable or selfexpanding. The stent machines accommodate each manufacturer's' unique strut design while protecting the surface integrity of the crimped stent. The uniform crimping control especially protects vulnerable stent edges, says Mickelson. Beyond quality advantages, automating the process eliminates prereduction crimp steps, greatly reduces cycle times, and significantly improves production yields, he points out. MSI offers the medical industry's largest range of stent crimping equipment, he notes. It offers units suited to R&D, pilot production, and varying manufacturing requirements.
Application Flexibility
MSI did a comprehensive search and evaluation of encoders for its stent automation machines, according to Mickelson. A combination of factors led to the final selection of the Renishaw RGH24 optical encoder high resolution and repeatability, small physical size, nowear optical design, LEDguided alignment simplicity, and the application versatility of Renishaw's flexible metal tape scale, which allows use in linear or radial applications.
The RGH24 readhead measures only 1.42" x 0.55" x 0.60" LWH (36 mm x 13.5 mm x 14.8 mm) and weighs just 0.4 oz (12 g). The RHG25 readhead, with separate interpolation electronics, has the same length and width, but is only 0.51" (10.5 mm) high and weighs only 0.3 oz. (9 g).
The Renishaw encoders combine the compact readheads with flexible, adhesivebacked steel tape scale. "The flexible scale allowed us to mount the linear encoders in partial arc configurations to meet our design needs," notes Mickelson. "We order the scale in a 15 ft. roll and just cut the length we need." Goldplated and protectively coated, the reflective 20micron pitch scale provides a linearity and slopecorrected accuracy of 3 microns/m.
The optical readhead rides above the scale at a slight standoff. The open, noncontact design avoids problems from hysteresis and seal friction/wear. Patented filtering optics in the readhead provide excellent immunity to dust and scratches. The readhead averages the reflections from over 80 scale facets, effectively filtering out signals which do not match the scale period to ensure signal accuracy and stability despite contamination or minor damage.
A red/green LED on the readhead or interface allows speedy setup and provides confirmation of optimum scale alignment. The LED is also tied into a signal monitoring circuit, providing visual alert of low signal amplitude to prevent unrecognized loss of encoder count. "It's critical for us and our customers to know that the unit is aligned," says Mickelson. "If it's not, our machine is missing counts, which means that our diameter could be off. The LED shows if we're aligned or not."
"The LED gives the Renishaw opticals a major advantage over magnetic encoders," he adds. "You don't know if a magnetic is aligned or not. That's a huge downside. Should customers do routine maintenance, they wouldn't know if the machine is aligned. "
Further assuring accuracy, the RGH25 provides an error line output that can be used to cause the machine to error if there is a fault, rather than carrying on with the possibility of a miscount.
The Renishaw encoders are available with either digital or analog (1V peaktopeak or microcurrent) outputs. Digital readheads produce differential linedriven quadrature signals to industry standard EIA/RS422. The differential line driver outputs provide exceptional noise immunity in harsh electromagnetic environments, enhanced by doubleshielded, highflex cable.
The Renishaw encoders give MSI a robust, versatile design with demonstrated reliability in industrial environments as it seeks to expand applications for its sequential compression technologies. MSI says that nearly any application which requires even, radial compression or processing of shapememory materials could potentially benefit from its proprietary segmental crimping technology. According to Mickelson, the company is currently exploring niche applications in microelectronics, fiber optics, wireand cable, and consumer products manufacturing. TMD
For more information on Renishaw encoders, contact Howard Salt, business managerEncoder Systems, Renishaw Inc., 5277 Trillium Boulevard, Hoffman Estates IL 60192.
Tel: 8472869953.
Fax: 8472869974.
Email: Howard.SaltRenishaw.com.
Internet: www.Renishaw.com.
For more information on segmental compression technologies, contact: Machine Solutions Inc., 2901 West Shamrell Blvd. Suite 101, Flagstaff AZ 86001. Tel: 9285563109. Fax: 9285563084. Internet: www.machinesolutions.org.

Explore the May 2005 Issue
Check out more from this issue and find your next story to read.
Latest from Today's Medical Developments
- Tariffs threaten small business growth, increase costs across industries
- Feed your brain on your lunch break at our upcoming Lunch + Learn!
- Robotics action plan for Europe
- Maximize your First Article Inspection efficiency and accuracy
- UPM Additive rebrands to UPM Advanced
- Master Bond’s LED415DC90Med dual-curable adhesive
- Minalex celebrates 60 years of excellence in miniature aluminum extrusions
- Tormach’s Chip Conveyor Kit for the 1500MX CNC Mill