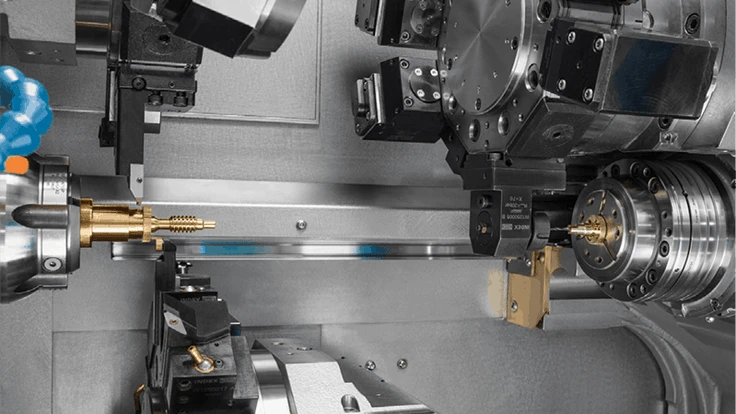
Index
Reflecting on its crisis response, Jake Grainger, CEO of Alpha Grainger Manufacturing Inc. highly praises his team for growing with technology and being eager to learn and apply new skills. These abilities have been integral to the company’s response to the coronavirus pandemic and reflect the industry’s ability to meet a massive challenge.
In early April, Grainger got a phone call from an aerospace manufacturer facing a major challenge with a medical part. The client needed to produce a very complicated body part for a pressure regulator used in a ventilator. Grainger’s customers needed to develop the part and produce 1,000 units per week to meet demand amid the COVID-19 outbreak. While no other manufacturer responded to this task, Grainger was not afraid to take on the opportunity.
Immediate solution
The blueprint files for the ventilator part included more than 150 dimensions, causing Grainger to briefly second-guess his ability to produce something so complex, but he then realized the component matched the strength of the Index C100 machine tool.
“The more I looked at it, I realized that yeah, we could get that thing going quickly. And because we had developed the skill sets, we knew how to run the very sophisticated software that’s used to design parts, generate machine tool CNC code, electronically prove out that code and make the required custom tooling – software products from Dassault Systèmes (SolidWorks), DP Technology (Esprit), and Index.”
“Later that evening, after I absorbed what I was looking at, I called my son Eric. We talked it over the next morning, we reviewed it, brought in our engineers, looked at it, and we all agreed: we can do this,” Grainger says. “We told our customer and they breathed a great sigh of relief because no one was willing to step up to the table and take on such a complex part that involved so many complex milling and turning features, so it was perfect for my alternative machine.”

The C100 multitasking, automatic production lathe offers high-speed production of parts turned from bar stock, making it well suited for the part that involved complicated milling and turning.
Within 10 days, Alpha Grainger was ready for production. They designed and produced all the custom tooling, had CNC cutting programs, the verification software had proven out the tool paths, and were ready to use the machine.
“At this point we were ready to set up the job, which involved 30 milling and turning tools. In the past, this would have taken days to load into the machine and carefully prove out, but we had already proven out the code and tool offsets with Index Virtual Machine software. The next step was to load the program into the C100, mount all 30 tools into three turrets, push the start button and get a good part the first time.”
He adds that the setup started on Monday morning and they had good parts in the afternoon. With their in-house capabilities, Alpha Grainger produced all of the custom cutting tools to turn things around quickly. They printed sample parts on their Stratasys 3D printer so they could have parts to hold and see, which helped them visualize how to machine the part.
Optimization software

The body component they were producing for the ventilator pushes out air, which requires extremely low pressure. Therefore, it had to be incredibly reliable and accurate to avoid damaging patients’ lungs.
To ensure the component functioned properly, Alpha Grainger knew they needed several software programs suitable for the design, programming, and prove-out. They chose SolidWorks computer-aided design (CAD) software and Esprit software to generate the machine tool code.
“We used SolidWorks to get a model of what the customer wants,” Grainger adds. “Normally, we need to change that so it can be manufactured correctly. We take their model, or if they don’t have a model, we create a model with SolidWorks. When we have this electronic solid model, we put it over to our Esprit software, which allows us to generate the machine tool code. In Esprit we select electronic versions of the cutting tools that we will be using and are able to see how those tools cut the various features on the part.”
They were able to take the CNC program generated in Esprit and run it on Index Virtual Machine which is an exact replication of the C100 on a desktop computer. By having the machine tool displayed on the desktop, Grainger’s team could see how the actual machine tool would perform in the real world. Everything could be optimized in the office and they would be sure that the real program would reliably run without a long and risky prove -out time. If actual tool offsets are used in Virtual Machine, the rendered part will be exactly what the C100 will be making. You can use the measuring tools in Virtual Machine to dimension the part back in the office.
“The industry has dreamed of the day that they could put the cutting tools in the machine, download the program, hit the start button and get a good part. With the different technologies we have – Solidworks, Esprit, Index Virtual Machine and the Index machine tool – we’re living that dream. We got the customer the parts that solved a huge problem for them. It’s a result of my people mastering the skill sets needed to use these very sophisticated and complicated software platforms.”
Alpha Grainger Manufacturing
https://www.agmi.com
Dassault Systèmes
https://www.solidworks.com/

DP Technology Corp.
https://www.espritcam.com

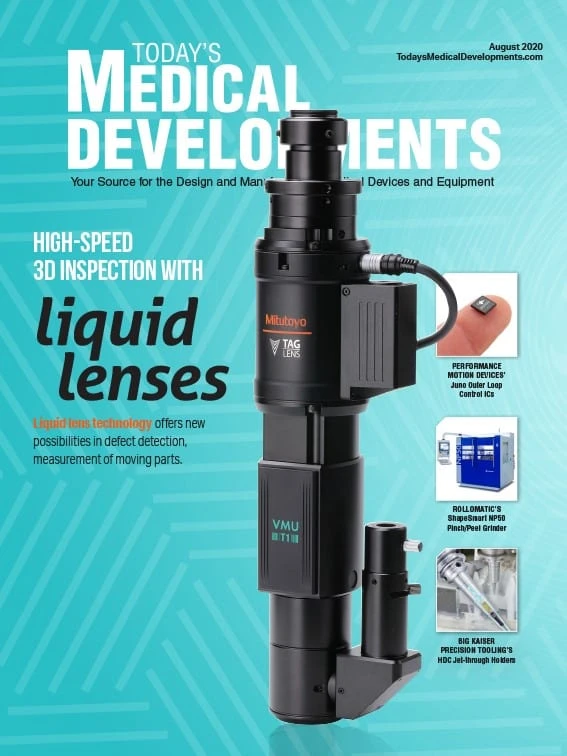
Explore the August 2020 Issue
Check out more from this issue and find your next story to read.
Latest from Today's Medical Developments
- Turnkey robotic systems are already behind the times
- You can still register for March’s Manufacturing Lunch + Learn!
- HERMES AWARD 2025 – Jury nominates three tech innovations
- Vision Engineering’s EVO Cam HALO
- How to Reduce First Article Inspection Creation Time by 70% to 90% with DISCUS Software
- FANUC America launches new robot tutorial website for all
- Murata Machinery USA’s MT1065EX twin-spindle, CNC turning center
- #40 - Lunch & Learn with Fagor Automation