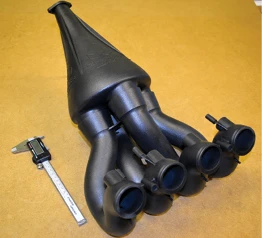

In recent years, additive manufacturing (AM) has evolved from a revolutionary technology into a mainstream process. Enabling fast, cost-effective production of complex high-quality components in a range of materials, it’s helping revolutionize manufacturing in an increasing number of industries. Despite its state-of-the-art advantages, it can also be subject to a more traditional and well recognized manufacturing problem: porosity.
To resolve this challenge, Graphite Additive Manufacturing turned to porosity sealing specialist Ultraseal Int’l. to expand applications and improve quality. Graphite AM, a 3D printing consultancy, specializes in complex designs and high-performance components in tailored materials. Graphite AM’s original customer base was almost exclusively high-tech sectors including automotive, motorsport, aerospace, and defense. While the company still serves these sectors, it has had real growth in other industries, according to Jonathan Warbrick, sales and marketing manager.
“AM is no longer a revolutionary process for prototyping and limited production runs. The cost and turnaround mean it’s a huge benefit for low-mid volumes – typically 250-to-500 component runs and tooling... It’s an area of huge potential, and has become a strategic focus of our work.”
Graphite AM primarily uses selective laser sintering (SLS), an AM process that deploys lasers to sinter powdered material, binding it together to create a solid structure. While the majority of 3D printing bureaus use standard or glass-filled nylon materials such as PA11 and PA12, Graphite AM has developed its own range of SLS blends, including fine graphite particles. With anti-static properties, graphite also improves impact and thermal resistance (up to 170°C), suitable for lightweight applications where strength and performance are critical.

However, porosity remains an issue. Traditionally a major issue with die-cast components, microscopic holes form within a part’s body during the AM process. Though invisible to the eye, they reduce component density, potentially leading to cracks, leaks, and fatigue. In applications with pressure differentials or requirements to be air or fluid tight, for example in cooling systems, this can be an especially critical issue.
In 3D printing, porosity is typically caused by the printing process itself or by the powder used in the process. Either way, it’s a long-recognized problem, transposed to state-of-the-art technology.
“To make sure our customers capitalized on the very best product quality, we needed to find a consistent, reliable solution to porosity. And for that, we needed expertise and experience,” Warbrick says.
Ultraseal develops, manufactures, and supplies porosity sealing chemicals, impregnation equipment, and services. Dr. Mark Cross, commercial sales director at Ultraseal, says the company had experience with porosity “in die-casting and electronic component manufacture. Though the technology is different, the challenge is similar, and we’ve been able to use our knowledge to create an effective solution.”

The porosity solution involves sealing the component using vacuum impregnation, a process with three key stages.
- Components are placed into an autoclave containing Ultraseal PC504/66 resin, a high-performance thermocure methacrylate sealant. The sealant is applied to the component under vacuum in an autoclave. The component is immersed in sealant, and the vacuum releases, and the pressure change draws sealant into micro-porosities and leak paths, allowing the sealant to penetrate deeply into the 3D-printed part.
- A cold wash module removes excess sealant from external component surfaces and tapped holes.
- A hot cure cycle exposes components to heat for a predetermined time period using a hot water bath which polymerizes the sealant, changing it from a liquid state to solid polymer. Components then undergo pressure testing to ensure they are leak free.
Ultraseal now delivers an end-to-end sealing service for Graphite AM from its UK Service Centre in Slough.
“Our partnership means we’re able to deliver reliable and leak free components, an essential characteristic in high performance parts,” Warbrick says. “Ultraseal also delivers reliable and rapid turnaround.”
We needed to find a consistent, reliable solution to porosity. And for that, we needed expertise and experience."
Graphite Additive Manufacturing
https://graphite-am.co.uk
Ultraseal Int’l
https://www.ultraseal-impregnation.com/

Explore the Additive Manufacturing Guide Issue
Check out more from this issue and find your next story to read.
Latest from Today's Medical Developments
- Birk Manufacturing achieves ISO 13485 recertification
- SW North America's BA 322i twin-spindle CNC
- The role of robotics in precision medical device manufacturing
- Swiss Steel Group’s UGIMA-X machinable stainless-steel sets
- #51 - Manufacturing Matters - The Impact of M&A in MedTech 2024
- Visual Components: 25 years of simulation and programming software innovation
- Zimmer Biomet announces definitive agreement to Acquire Paragon 28
- Discover an innovative technology for EMI/ESD/TVS suppression