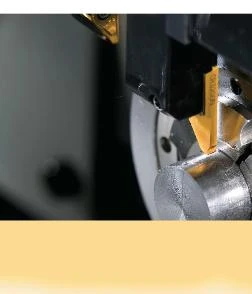
The demand for small, precision components is growing. In addition to the masses ofrelatively simple parts,various manufacturingindustries have developedapplications where there is a growing need for increasinglycomplex components made from barstock material.Machine tools have taken big steps in this very competitivearea, and the focus is now on the development of cuttingtools to provide the performance needed for machineutilization and component output.
A rapidly growing sector in the manufacturing industry isthat of small, precisionturned components. There is a growingdemand for these parts for products made by the medical,connector, automotive, IT and appliance industries. In addition, suppliers to the aerospace anddefense industries are now users ofsmall tools because of the growingrole of electronics, hydraulics andsuch for control units and mechanisms.This development means that agrowing number of small componentsare machined in batches thatare smaller than those of traditionalautomatic machines. The componentsare mostly of smaller dimensionsthan those made generally inthe engineering industry and arenearly always made frombar stock.
Manufacturingmediumsized to large batches ofsmall components is a very competitivebusiness. Many parts are relativelysimple in design and are oftenmade from easytomachine materials,but the demand for more complexcomponents and materials that aredifficult to machine is growing. In thiscostsensitive area of the manufacturingindustry, using modern means andmethods of production determineshow competitive production is.
Today, the manufacture of smallcomponents is carried out to anincreasing extent with CNCsliding headstock automaticmachines in diameters rangingfrom .020 to 1.260 inches. Theseare barfed machines, achieving thezaxis movement by the bar movingthrough the head stock, instead ofthe tool performing the feed movement.The advantage of this is thatthe tool is very close to the spindlecollet, supporting but not holding thebar. This means good support duringmachining, which is especiallyadvantageous when machining alongthe length of a component.
In machines for small parts, themachining zoneis a lot more compactthan it is for many other machinetools. Tools have to be small, as thereis limited access for adjusting andchanging tooling. Cutting tools areoften placed in gangs or on turretsso as to be able to machine close tothe spindle collet and to minimizethe toolchanging time. Cutting toolsfor this area have also tended to becomplicated and of special design,often unnecessarily expensive,leading to a higher toolcost portionof the total production cost than inother machining areas.
Generally, it can besaid that thetool technology for small, precisionturned partshas up to now consisted ofoutdated concepts, when comparedwith tools for other areas.
Developments in machine toolsand manufacturers expectationshave influenced the developmentof Sandvik Coromants growingprogram of cutting tools for smallpartmachining. Yesterdays levels ofground chipbreakers and cutting geometries,the use of carbide blanks tomake tools and outdated indexableinsert tools are not representativeof todays levels of cuttingtool technology for use in slidinghead machines.Todays tool concepts are based on developments in modern indexable inserttechnology, of which cutting off and internal machining are two areas thathave seen recent innovations.
Cutting off ba r mater ial and grooving are part of nearly everysmallpart manufacturing sequence, and too often these actions areperformed with inferior tools that do not utilize the capacity of slidingheadmachines. Today, there are highperformance solutions for this area within theCoroCut program from Sandvik Coromant. CoroCut 2 and 3 have been speciallydeveloped to meet the criteriaof todays slidinghead operations,such as allowing easy insert indexingin cramped spaces and the need formaximum cutoff length.
The built in stability of the toolholder and insert combinationallows turning to widen grooves andperform other operations, thus helpingto reduce the number of requiredtool types. Conventional feed ratescan usually be doubled with CoroCut tools, significantly cutting thetime needed to part off the masses ofcomponents produced. The parting off width, as determined by thetool, is reduced with CoroCut, whichmeans less material waste.
Chip control is an importantperformance factor in turning operationsand becomes more emphasizedwhen the machining zone is limited,as it often is in machining smallholes in small parts. One of the mainfeatures of CoroTurn XS is improvedchip control. This newly developedsolid carbide range for very smallholes, down to .039 inch in diameter,has additional advantages, such asproviding short cycle times throughhigher cutting data and higherproduction security through morepredictable tool life.CoroCut XS has been developed toprovide new levels of performanceand results. Grooving is improvedby providing a combination of positivefeatures such as improved chipcontrol, where chips are more easilyevacuated out of grooves, andachieving the required surface finish,ensuring security and quality. Forturning, a new combination of insertgeometry and carbide grade meanshigher cutting speed and greater feedcapability. Chipbreaker developments,with a sharp, tight geometry,give shorter cutting times and goodsurface finish. When parting off, highstability in the insert seat leads toi m p r o v e d m a c h i n i n g p e r f o rmance,better tool life and a secureprocess with less downtime.
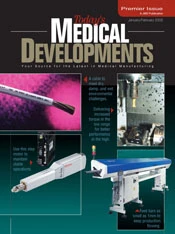
Explore the January 2005 Issue
Check out more from this issue and find your next story to read.
Latest from Today's Medical Developments
- Midwest DISCOVER MORE WITH MAZAK
- Reshoring survey to provide insight for US industrial policy
- NB Corporation of America's ball splines
- Zimmer Biomet to acquire Paragon 28
- Industrie 4.0 award for Paul Horn GmbH
- CMMC requirements and your business
- Stryker exiting spinal implant business
- Perfecting the manufacture of microscopically thin films for tech, medical applications