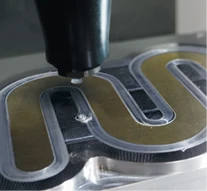

A part of Mazak’s family of Hybrid Multi-Tasking machining centers, the VTC-300C FSW combines milling and friction-stir welding (FSW) capabilities. With a full traveling-column design, automatic tool changer, and powerful 40-taper spindle in addition to the FSW package, the machine helps shops reduce lead times and achieve greater part accuracy with less required capital equipment – all while enabling methods for processing parts with stronger welds than ever before.

Designed and manufactured in Kentucky in partnership with the Provo, Utah-based Mazak MegaStir, the VTC-300C FSW joins Mazak’s series of Hybrid Multi-Tasking machines, which adds capabilities such as advanced additive, joining, and gear-cutting technologies to the multi-tasking capabilities found in Mazak machines.
The machine’s FSW package uses a process that involves frictional heat and forging pressure to create full-penetration, defect-free welded joints stronger than conventional methods.
A solid-sate joining process with a non-consumable tool, the Mazak FSW head joins two metal plates without melting the workpiece. Commonly considered a forging process, FSW is well-suited for joining alloys with low melting points, including aluminum, copper, and brass, among others.

The new welding technology complements the existing VTC-300C machine platform, which delivers a standard 15,000rpm, 30hp, 40-taper spindle that can handle a wide variety of metal-cutting applications. Additionally, the machine and way-cover design has been enhanced to provide 1,574ipm rapid feed rates on all axes. Its fixed 78.74" x 30" table provides process flexibility for a wide range of applications, while an optional center partition can divide the machine’s work envelope into two separate work areas to allow the machine to be in cycle in one area while loading, unloading, or setting up a part in the other. The machine’s axis travels measure 65.35" in X, 30" in Y, and 25.6" in Z.
The machine also features Mazak’s MAZATROL SmoothG CNC, which makes it easy to generate programs for highly complex parts production. Several innovative programming, performance, and monitoring functions bring optimum speed and accuracy to complex part production. Advanced hardware, including a tilting CNC panel and multi-touch control screen, allows for complete ease of use. https://www.mazakusa.com

Explore the Additive Manufacturing Guide Issue
Check out more from this issue and find your next story to read.
Latest from Today's Medical Developments
- Birk Manufacturing achieves ISO 13485 recertification
- SW North America's BA 322i twin-spindle CNC
- The role of robotics in precision medical device manufacturing
- Swiss Steel Group’s UGIMA-X machinable stainless-steel sets
- #51 - Manufacturing Matters - The Impact of M&A in MedTech 2024
- Visual Components: 25 years of simulation and programming software innovation
- Zimmer Biomet announces definitive agreement to Acquire Paragon 28
- Discover an innovative technology for EMI/ESD/TVS suppression