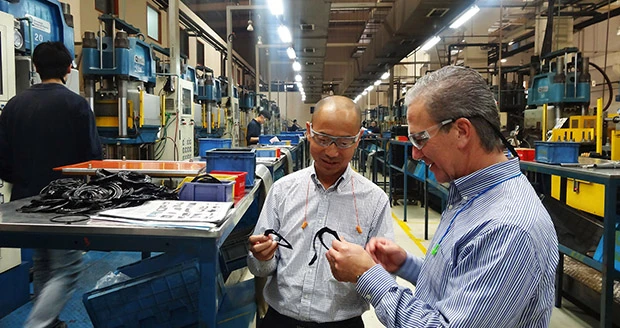
Greater efficiency and less time are the key advantages for Parata Systems’ next-generation pharmacy automation for dispensing pill prescriptions. Its’ new Parata Max holds and automatically dispenses up to 232 finished prescriptions, more than the 196 average prescription volume at U.S. pharmacists.
Behind this improved performance is a critical seal-coupler device designed and manufactured by Minnesota Rubber and Plastics (MR&P). An earlier system design caused the system’s compressor to overwork while allowing counting speeds to dip below Parata’s aggressive expectations.
MR&P developed a new seal-coupler design that was incorporated into Parata’s next generation system prior to general availability. That early success led to an expanded role for MR&P in helping Parata drive numerous design and production enhancements to Max and its semi-automated companion, Parata Mini, which automates pill counting. MR&P worked closely with Parata on design, manufacturing, assembling and testing of cell assembly components, and related components used in the system.
“MR&P became a ‘start-to-finish’ supplier for us,” reports David Calderwood, vice president, Engineering. “Their initial success designing a solution for the seal-coupler, manufacturing the device and providing 100% testing led to a significant amount of front-end design and prototyping work on the dispensing cell and related components. MR&P provided comprehensive program management and manufacture of the cell assembly. It has been a very successful relationship.”
Parata Max and Mini Automation
Parata Max is the first and only next-generation automation introduced to the retail pharmacy market. It is used in chain, community, government and institutional pharmacies to improve prescription-dispensing efficiency and capacity and reduce errors.
How fast is fast?
The Max system automates 60% of an average pharmacy’s total prescription volume with upkeep of less than an hour a day. The system does not make drug or dose errors, the source of 88% of medication errors, and delivers counting accuracy 10 times higher than the industry standard. Also important, the high capacity system is very compact, occupying just 12 square feet, so it replaces a single shelving unit in most pharmacies.
Parata Mini is an entry-level automation solution that provides fast accurate counting, with a user experience that creates seamless scalability to Max as the pharmacy’s volumes grow.
Seal-Coupler is Key
Parata’s pneumatically actuated system is designed using the latest technology to provide trouble-free operation. The seal-coupler is a critical intermediary device in the pneumatic motion high pressure system. Positive sealing is imperative in the system so no pressure changes occur that could affect compressor function, air flow rate, and ultimately pill count speed and accuracy.
When activated, carefully regulated pneumatic pressure moves the pills from individual cells that have the dual purpose of both storage and dispensing. These are “smart cells” with an electronic circuit board that broadcasts the cell’s location on the system, so the robot always selects the correct cell for dispensing.
With a long history of manufacturing complex seals for many demanding applications including medical, MR&P brought its high level of experience with molding and unique material formulations and provided a complete solution including program management for Parata. This included design and prototype work, large volume, automated manufacturing and 100% part verification for quality for all cell components.
Molded Elastomer Lip Seal
The seal-coupler MR&P designed is a spring-loaded assembly with an upper and lower housing molded from a nylon material that is ultrasonically welded together. Within this housing, a spring is centered on a retainer at one end and a poppet core on the other end. This poppet core, under tension from the spring, locks into a special lip seal molded from a very durable, high performance proprietary elastomer material.
MR&P’s new lip seal design addressed the initial problem of seal alignment with a more precise-fitting lip configuration at the seal end, precision molded from a specially engineered elastomer material. This material greatly improved wear resistance with a leak-proof connection to the high-pressure system, 100% tested for quality.
“Minnesota Rubber and Plastics did a nice job with the seal coupler design,” Calderwood says. “That gave us confidence in their abilities and we saw that they had large-scale molding capabilities, including mold design and build, and complete testing facilities, so we began discussing other ways they might help us.”
Prototype Development, Large-Volume Manufacturing
Next, Parata challenges MR&P to challenge the components to which the seal-coupler was connected. First was the air manifold assembly. MR&P designers ensured that the overall manifold’s profiles were designed and fabricated to strict specifications so that the manifold ports sealed and connected properly. Similar improvements and efficiencies were brought to several other components including vial descrambler fingers and cradle assemblies.
Once these components and assemblies successfully passed prototype testing, large-volume production was initiated at MR&P’s River Falls, Wisconsin, manufacturing facility. Testing was especially important to the success of this project with MR&P providing three stages of comprehensive testing during the design/manufacture cycle. According to Calderwood, “That testing was very important to the quality of our results.”
The extent of MR&P’s contribution to improving the component and assembly designs and overall quality is evidenced by the fact that MR&P became an assignee of the patent application made on the system’s cell calibration mechanism.
“Through all of Parata’s design phases, MR&P provided a single-source solution and complete program management team,” Calderwood says. “Their dedicated team covered the full spectrum of product design assistance, material formulation, prototyping, mold design and manufacture, prototype testing, large-volume molding, assembly and final testing. They were flexible and responsive, reacting to new needs as they emerged, providing design direction and production alternatives to best meet common goals. MR&P facilitated tooling changes while meeting ongoing production demands, and provided finished products that were on-time and defect free.”
The overall project spanned an abbreviated development period from preliminary design planning to the onset of large-volume production.

Explore the August 2009 Issue
Check out more from this issue and find your next story to read.
Latest from Today's Medical Developments
- German robotics and automation in a downturn
- Blueshift’s AeroZero
- November USMTO grow from October
- Platinum Tooling’s custom and special tooling
- Top 5 global robotics trends 2025
- Accumold’s micro molding innovations
- Methods Machine Tools, Multiaxis, announce AI solution investment
- MGS to showcase global expansion and healthcare CDMO expertise