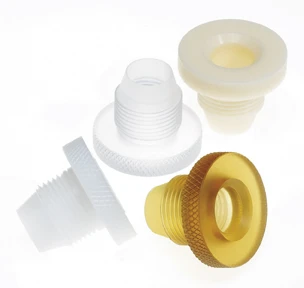
Dover High Performance Plastics (DHPP), a supplier of high performance PTFE plastic components, has seen a rise in the demand for PTFE parts and assemblies in the medical industry. DHPP has been supplying a wide variety of components to this industry for more than ten years.
DHPP fabricates many of these components from PTFE (polytetrafluoroethylene), nylon, acetal and UHMWPE (ultra high molecular weight polyethylene), which are used as seals, gaskets, seats and fittings. These components are an intricate part in products such as pumps, valves, as well as regulators and pressure controls for respiratory, anesthesia, dental, surgical, emergency care, home care and cardiopulmonary equipment. Some specific examples follow:
Mini-Vacutron Unit
Compression molded virgin Teflon ® and gold pigment filled PTFE seal discs are used in a MINI-VACUTRON unit made by Allied Healthcare Products, Inc. This unit is used by hospitals for post surgery convalescence. A tube is inserted into the patient's stomach and connected to the vacuum system to remove residual body fluids from the stomach after surgery in that area. The key is not to create a strong vacuum in any one area so as not to destroy the stomach lining. Therefore, the vacuum system must be very passive and intermittent.
The Teflon/PTFE seals are especially suited for this application because Teflon has the lowest coefficient of friction of any material available, and offers an excellent seal of moving parts under very low vacuum applications.
Surface finish and flatness of these seals are very critical as they must seal against each other and not allow any vacuum leaks. Consequently, each unit must be lapped or burnished to an ultra smooth finish. The materials used also must hold up to millions of cycles without failure, as this is a critical function of the unit.
Oxygen Separator
Plastics lend themselves well to seal applications where cost and weight are factors. Another major factor is precision. Plastics components (acetal) are CNC machined by DHPP for Sunrise Medical to be used in an oxygen concentrator, which allows patients with breathing problems to inhale pure oxygen without the use of oxygen bottles. The actuating machined discs must rotate to open and close inlet/outlet ports in order to pump the separated oxygen. This application requires the parts to have approximately a mirror finish and to be flat and parallel within .002 inches. This precision can only be accomplished by machining the components.
Other medical applications involving plastic materials such as PVC and UHMWPE include fittings for contamination suits and large slide bearings/clamps for aquatic rehabilitation. TMD
Teflon ® is a registered trademark of E. I. Dupont DeNemours

Explore the July 2005 Issue
Check out more from this issue and find your next story to read.
Latest from Today's Medical Developments
- Unlocking GenAI's potential: Insights from the Supply Chain Horizons 2025 report
- Celebrating 75 years of innovation at Jorgensen Conveyor and Filtration Solutions
- Free webinar to offer expert advice on optimizing machining operations
- How collaboration between companies can elevate manufacturing
- AI meets innovation: Cambridge's device transforms heart screening
- Mazak and Premier Engineering team up for greater agility in Florida
- Struggling with inventory or supply chain pressures? Find answers in our free webinar
- Free webinar: Advanced manufacturing solutions to support the Navy