
The injection molding process lends itself to producing high-precision, complex components for medical applications, especially when part-to-part integrity is required in high volumes.
For medical applications, the primary material recommended for molding is silicone. It is versatile and, as a liquid raw material, it offers advantages in processing for technical components in high volumes.
Silicone is the highest purity and demonstrates biocompatibility to ISO 10993 and USP Class VI standards, and is compliant with European Pharmacoepia 3.2.9. The material easily withstands common sterilization methods.

Liquid injection molding (LIM) is often used to produce silicone medical devices. Producing components by simultaneous injection of liquid silicone rubber (LSR) in combination with engineered plastics is commonly referred to as 2K, 2-shot, multi-component injection molding, or co-injection. Trelleborg calls it 2C LSR and it allows combining two, three, or more materials into one fully-bonded, component.
2C LSR enables complex components, ideal for parts with a large amount of detail, and offers designers great latitude, integrating multiple components into one, such as for medical applications where dead space needs to be avoided and hygienic designs created.
These advantages can only be realized if there is close collaboration between the device maker’s engineering team and the injection-molding engineering experts at the silicone component manufacturer.
At the root of any successful injection molded component is the tool. However, developing a tool-grade steel mold, hot- or cold-runner blocks, and related process automation equipment can be expensive, but must be considered. The high initial tooling cost should never be judged on cost alone, but calculated as an investment throughout the tool’s lifetime. Liquid injection molding can produce high-integrity parts in high volumes, making the tooling relatively inexpensive when considered piece-by-piece throughout a program’s life.
Mold efficiency depends on cavitation, parting-line geometry, gating, venting, surface finish, and supporting automation. It’s important to ensure the mold is robust enough to mitigate the inherent lot-to-lot variability of raw silicone. The mold will need to integrate seamlessly with equipment that pumps, mixes, injects, compresses, heats, and ejects components.
In processing, watch points include restrictions on part thickness to avoid shrinkage problems. Parts can also require de-flashing with added cost. These issues can be mediated through close collaboration between the device designer and silicone component manufacturer. For instance, if the tool and process equipment are expertly designed, flash can be nearly eliminated.
Injection molding of liquid silicone can produce compounds with complex geometries and designs unachievable by other manufacturing methods. Beyond LIM, 2C LSR technology can provide opportunities for part design and additional benefits.
To take full advantage of possibilities offered by silicone injection molding, suppliers must understand the details involved with manufacturing silicone rubber parts and complex medical devices. The key to best solutions, extended life, hygienic design, meeting standards, and cost-effectiveness throughout total product life is early and close collaboration between the medical device designer and the silicone component manufacturer.
Trelleborg Sealing Solutions
www.tss.trelleborg.com
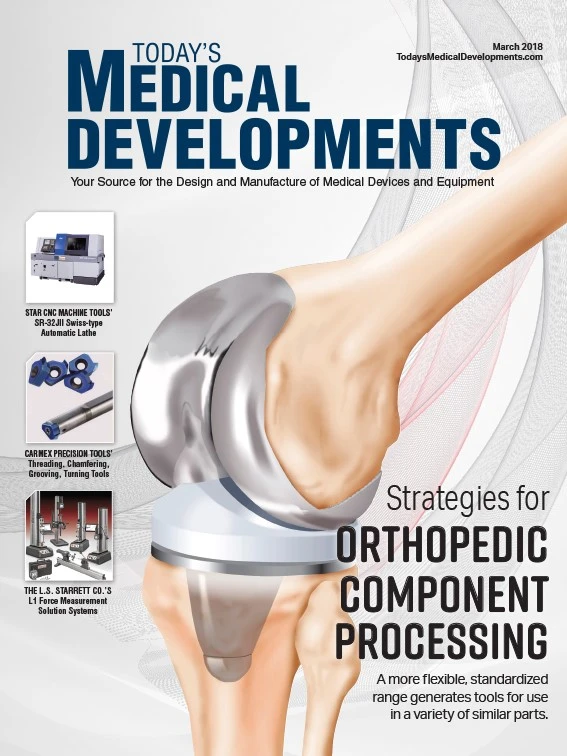
Explore the March 2018 Issue
Check out more from this issue and find your next story to read.
Latest from Today's Medical Developments
- A 30-year journey through CAM: Insights on simulation technology
- Behringer Saws’ HBE663A Dynamic horizontal bandsaw
- North America's supply chains face sharp decline due to tariffs
- Experience precision: GF Machining Solutions' CUT F Series wire EDM
- Mastering high-temp alloys with Kennametal Inc.
- Integer expands operations in Salem, creating 83 jobs
- Siemens unveils new Teamcenter X: Revolutionizing SaaS PLM for all manufacturers
- 3 Questions with an Expert with Allied Machine & Engineering