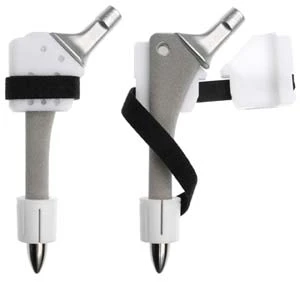
De PuyOrthopaedics specializes in the design, manufacture, and development of orthopaedic devices. At the company headquarters in Warsaw, Indiana, Jon Heckman, supervisor of the tool room, works with products like the Preservation Uni-Compartmental Knee implant and the S-ROM hip every day, creating lean fixturing solutions for the company. Although DePuy has 6,000 employees, their model shop and tool room operate as small job shops, where being lean is a way of life. The tool room focuses on fixturing applications while the model shop concentrates on conventional prototyping. "We're a cost efficiency center. People don't want to put money into fixtures, so it's important that we be effective from the top down," says Heckman. Although making fixtures might not be the most glamorous part of the orthopaedic device industry, it's critical to the entire process. Because orthopaedic implants end up inside patients' bodies, it's important the implant isn't touched improperly as it is moved from one point to another during the manufacturing process. "The fixturing has to replicate the product, which means tolerances are tight and the prints don't exist," says Heckman, who leads a team of 12 machinists. Both the tool room and model shop rely on specific equipment to get each project done efficiently. Although these two departments both have Hurco VMX series vertical machining centers, they use them differently based on the varying requirements of each job and the skills of the individual operator. Ultimately, the technology has to be flexible enough to give the machinist control to operate the machine the way that works best for the specific task. By: Maggie P. Smith, Hurco Companies, Inc. Edited by: Tom J. Grasson, Editor-in-Chief According to Heckman, the Hurco CNC machines work well when it comes to flexibility and usability, giving the machinist more control to be efficient. "I don't know of another machine where you can pull down the file and 30 minutes later have a form. You can be mediocre in math, mediocre in geometry, and still successfully make a part," says Heckman. Heckman's group uses the shop floor programming features on their CNC mill whereas Bill Sellers' prototyping group uses NC programming and the Hurco control's DXF transfer software feature. "We just send the DXF file straight to the machine," says Sellers. Sellers leads eight people in the Prototyping Services department. "We have one shift with about 800 projects running through this shop each year," reports Sellers. The Prototyping Services group gets a plastic form and a CAD file from the Rapid Prototyping department and must find the best way to manufacture the part. "We focus on conventional prototyping, our goal being the manufacturability of the part," explains Sellers. DePuy Orthopaedics runs 17-4, 300 series stainless steel, titanium, and cobalt in the prototyping services model shop. Ability to adapt and revise is key, as parts from Prototyping end up in the cadaver lab for the first rounds of tests. Back in the toolroom , Heckman explains the advantages of Hurco's shop floor programming (Hurco Conversational Programming). The controls on the tool room's Hurco VMX 2 4 a n d VMX 30 are intuitive and reduce the bottleneck and cost associated with CAD/CAM seats. "The Hurco is simplistic to the point that it makes anybody productive. And that's rare to have a machine tool that is this user friendly," says Heckman. His group often uses the lines and arcs part of Hurco's control programming software and utilizes the AutoCalculation feature that eliminates time-consuming data entry and the hassle of trigging out the part. Industry experts speculate the orthopaedic implant industry will have continued growth, though on the downside, much of the payment for these life - saving implants will be from Medicaid, where the reimbursement rate has remained static and companies are squeezed to produce better products using less money. With help from Hurco machines, DePuy can ensure their "lean" way of manufacturing with innovation continues. Hurco Companies, Inc. Indianapolis, IN hurco.com

Explore the September October 2006 Issue
Check out more from this issue and find your next story to read.
Latest from Today's Medical Developments
- HERMES AWARD 2025 – Jury nominates three tech innovations
- Vision Engineering’s EVO Cam HALO
- How to Reduce First Article Inspection Creation Time by 70% to 90% with DISCUS Software
- FANUC America launches new robot tutorial website for all
- Murata Machinery USA’s MT1065EX twin-spindle, CNC turning center
- #40 - Lunch & Learn with Fagor Automation
- Kistler offers service for piezoelectric force sensors and measuring chains
- Creaform’s Pro version of Scan-to-CAD Application Module