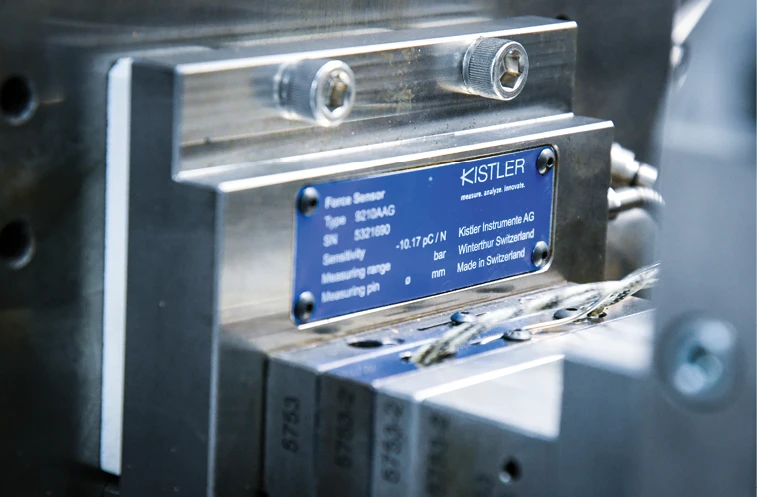
KISTLER

Custom medical device and consumer component contract manufacturer Tessy Plastics, with several facilities in Central New York, engineers, manufactures, assembles, and distributes a range of products. Using a scientific injection molding (SIM) approach allows Tessy engineers to define and optimize the company’s molding process from start to finish. Ben Passetti, research & development engineer at Tessy, takes the quality of their molded parts seriously.
“Our product portfolio is split 50/50 medical/consumer. We focus primarily on value-added, high-dollar items with very complex manufacturing and tight toler- ances – everything from 720 tons down to micro-molding – so our molding portfolio is large from a versatility standpoint,” Passetti says. “We focus on micro-molding in the medical sector because it is challenging and difficult. We accomplish tight tolerances because of the tooling partners we have.”
Overcoming complexities
Continuous process monitoring and control of the entire production measuring chain are essential in meeting requirements, and Swiss sensors and equipment company Kistler’s cavity pressure systems and sensors handle the task – from measurement through documentation of cavity pressure. Customized monitoring of tolerance limits by piezoelectric sensors results in visible process deviations, detectable at an early stage, minimizing rejects and scrap. Combining Kistler’s process monitoring systems and sensors optimizes process efficiency, offers quality assurance, and gives Tessy a competitive edge.
“There has been a visible shift in the plastic molding market within the past 5 years. Customers are more educated and understand a lot more about the injection molding process than in the past and they are actively searching for more technological, savvy solutions,” Passetti says. “They are more willing to accept risk with applications to gain technological reward in order to advance in this competitive market.”

Versatility for success
After reviewing Kistler’s product portfolio, Tessy engineers decided to implement and combine products.
“Tessy has been using several Kistler products,” says Jay Sklenka, field sales engineer at Kistler. “This includes the Kistler ComoNeo, maXYmos, load cells, and pressure sensors. They are also using our amplifiers mounted on the injection molding machines to bring the pressure signals back into the machine controller.”
Understanding how versatility among several components can be integrated to achieve maximum success, Passetti notes that, “Bridging the gap from technology to manufacturing; integrating current technology into our customer’s parts design, is the primary goal of our daily operations.”
Passetti adds that he and his team must ask themselves how they can speed up part production with higher quality and more cost-efficiency for the company and the customer. The answer, Passetti says, is Kistler process monitoring sensors and systems.
“Prior to the implementation of Kistler products, we were seeing process inconsistencies. We had used pressure sensors in the past but never on a micro-scale. We decided to test Kistler’s pressure sensors on a micro-scale to see if we could identify the variation between the machines,” Passetti says. “Once we saw how effective Kistler’s pressure sensors were, we chose to implement them on our machines. They have proven invaluable for seeing the variation between the molding machines, preventing the mold from being overpacked, and detecting short-shots in real-time. From an assembly standpoint, Kistler pressure sensors allow us to detect the force that drives the components back and forth so we can make any necessary adjustments with reliable, visible, sustainable results.”
The maXYmos gives a better understanding of what components look like, ensuring they are fully formed and can move into the production stage with 100% zero-defects. Implementing Kistler’s ComoNeo process monitoring system revealed what was happening in the mold to achieve accuracy and repeatability.
Gaining control
“In one of the first stages of the molding process for our medical components, the parts are inserted with the automation directly into the medical component. Here, we are monitoring the cavity pressure to ensure parts are fully formed and that we do not overpack the mold using a visible envelope/reference curve over the injection profile so that we can monitor the fill,” Passetti says. “Sometimes, we will see a spike in this curve because we are injecting the mold so fast that the machine cannot slow down in time to prevent mold damage. To overcome this issue, we are watching that pressure sensor data on the Kistler process monitoring system, waiting for the curve to start rising, and if it rises too soon, we stop the machine.”
“Later in this molding stage, it gets an actuator placed in it and then a retainer clipped over the entire product. It then goes to a final inspection station, where we use a Kistler sensor and the maXYmos to fire that sled and drive all those components into place. We then measure the forces to actuate and retract the medical assembly so that we get a complete profile of the actuation to determine the pass/fail percentage and the actuation numbers that we need to form a quality assured, repeatable medical assembly,” he adds,
Passetti says they use Kistler process monitoring systems and sensors to glean information from processes, and without this, they would likely struggle to meet the demands of today’s market.
“The presses that we purchase for our medical assembly line now have Kistler amplifiers built directly into them; they are integrated into the human machine interface (HMI) so that the reference curves and data can be transferred directly. We also have a stand-alone ComoNeo unit with its own monitoring system and a maXYmos with its own monitoring unit for other purposes,” Passetti explains.
Since implementing Kistler products, Passetti says the company has experienced success in terms of efficiency, repeatability, quality assurance, and cost-effectiveness.
“We are definitely reducing scrap because we can identify when we are making scrap in real-time,” Passetti says. “Being able to see what is going on directly in the mold – identifying non-conforming parts sooner – reduces scrap and improves our efficiency across the measuring chain.”
Looking at the reduced rate of scrap and increased return on investment (ROI), Passetti notes, “We are definitely satisfied with Kistler solutions. Kistler is continuously working to provide smaller systems and sensors, especially on the micro-scale side, and we are happy with how much easier it allows for integration into our machinery.”

Choosing to partner with Kistler has also paved the way for future success and process improvement.
“Our plan is to integrate more Kistler pressure sensors and systems into future molds and to retrofit our existing molds. Process systems and sensor technology from Kistler, integrated into our core processes, helps us stay ahead of the competition from a quality assurance and efficiency standpoint,” Passetti concludes.
Kistler
https://www.kistler.com
Tessy Plastics
https://www.tessy.com

Explore the May 2019 Issue
Check out more from this issue and find your next story to read.
Latest from Today's Medical Developments
- How to Reduce First Article Inspection Creation Time by 70% to 90% with DISCUS Software
- FANUC America launches new robot tutorial website for all
- Murata Machinery USA’s MT1065EX twin-spindle, CNC turning center
- #40 - Lunch & Learn with Fagor Automation
- Kistler offers service for piezoelectric force sensors and measuring chains
- Creaform’s Pro version of Scan-to-CAD Application Module
- Humanoid robots to become the next US-China battleground
- Air Turbine Technology’s Air Turbine Spindles 601 Series